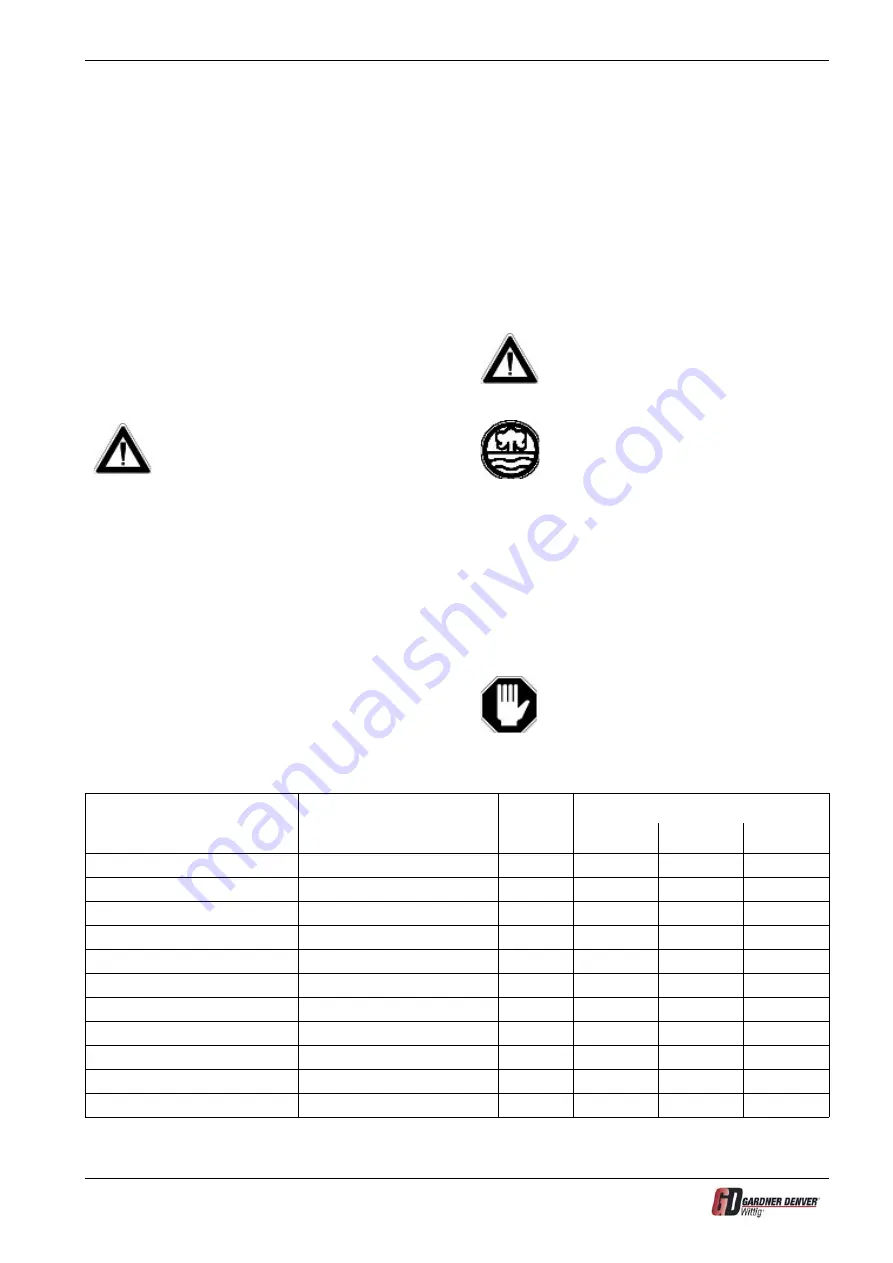
7.0 Maintenance
T-BA/ET-1250-0-GB-
10
-
11
17
7.0 Maintenance
7.1 Warranty
Please note that we accept no liability in the event of
failure to comply with the installation and operating
manual.
It should be noted that repairs on the rotary compres-
sors, respectively compressor vacuum pumps may
only be carried out by authorized workshops using ori-
ginal spare parts; failure to comply with this require-
ment will result in the warranty becoming void. A list of
our customer service stations is separately enclosed
with the order documentation.
7.2 Maintenance, maintenance schedule
Please follow the safety notes on page 5
when carrying out maintenance and
inspection work.
Disturbances due to inadequate or improper mainte-
nance can incur very high repair costs and prolonged
machine downtime. Regular maintenance is thus
essential.
The operating safety and service life of the machine
depends primarily on proper maintenance.
The following table contains time, control and mainte-
nance information for normal use of the machine.
The stated maintenance periods are based on a daily
operating time of about 5 hours. The maintenance
period can be extended if the specified number of
operating hours is not achieved.
Due to the different operating conditions it is impossi-
ble to predict when the check up for wear, repairs,
maintenance and inspections will be required. A suita-
ble inspection routine needs to be specified in accor-
dance with your operating conditions.
Upon completing the work, the protective
devices must be properly reattached.
When removing oil, grease, solvents or
parts, e.g. filter cartridges, please com-
ply with the regulations for safeguarding
the environment.
7.2.1 Cooling
The cooling air requires a free passage.
Check the cooling air inlets and outlets every week
and clean away the adhering dirt and dust where nec-
essary.
For an optimum cooling effect, unrestric-
ted circulation of the air is essential. Fou-
ling reduces the cooling effect and can
cause the machine to overheat and fail.
Maintenance schedule
Maintenance points
Type of work
see
Maintenance periods
Chapter
1 week
1 month
3 months
Cooling air guide
check, clean
•
Compressor vacuum pump
clean
•
Vacuum filter
clean
•
Combination air filter check,
clean
•
Safety valve
check
•
Vent valve
check, clean
•
V-belt, belt tension
check, retighten
•
Oil tank
clean
•
Check valve
check
•
Vent valve
check, clean
7.2.8
•
Rotary slide valve
Check for wear (intake flange)
•