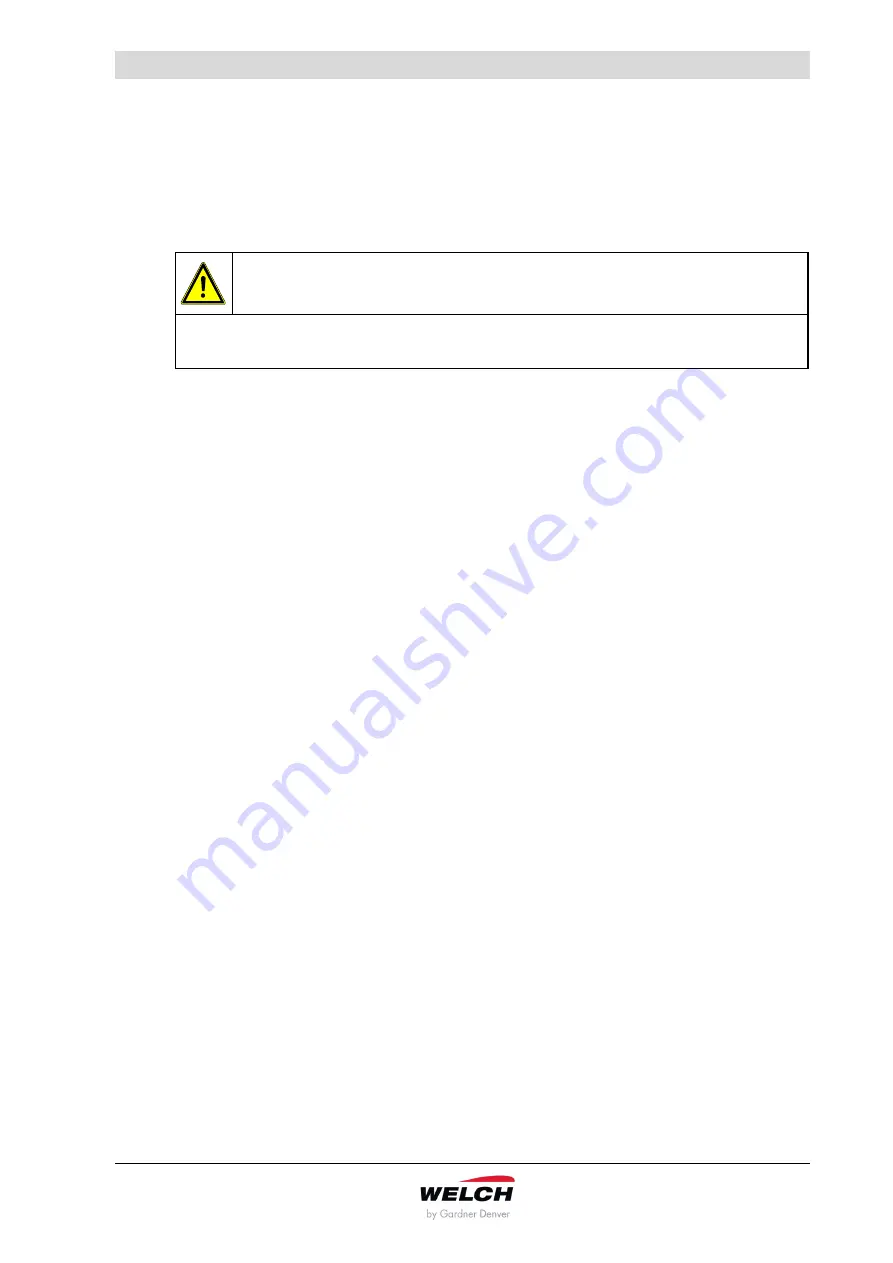
Description
P1700040
11
When pumping condensable vapours, they may be compressed during the compression phase above
the saturated vapour pressure and condense.
This causes considerable deterioration in the vacuum pump’s performance:
ultimate pressure is not achieved
corrosion occurs
heavy oil contamination and formation of emulsions
CAUTION!
Operating with gas ballast increases the operating temperature of the vacuum pump
by 5
– 10 K.
The gas ballast valve can increase the pump’s water vapour tolerance. In many vacuum pump
applications the gases being pumped from a system are a combination of permanent gases and
undesirable vapours such as water vapour. Under some conditions, the vapours condense in the
second stage of the pump and contaminate the oil. The gas ballast valve reduces oil contamination by
decreasing or eliminating vapour condensation.
Vapour condensation is most likely to take place when the gas compression ratio is high, i.e. when the
pump compresses a relatively large volume of gas to a small volume. Whether or not condensation
takes place is dependent upon several factors, including the proportion of permanent gases to
vapours at the pump intake. If the gases being pumped consist entirely of vapours, condensation will
definitely occur unless the gas ballast valve is opened. The gas ballast valve adds a small amount of
air at atmospheric pressure to the gas being compressed in the second stage. This reduces the
compression required to push the gas out past the exhaust valve (less reduction in volume is
required), and therefore reduces or eliminates condensation.
When the gas ballast valve is open, the pump has to work a little harder, resulting in a slight increase
in operating temperature. The increase in temperature is small, however, and is not harmful to the
pump. Also, the pump is slightly noisier, and the pump’s ultimate pressure is somewhat reduced.
Therefore, the gas ballast valve should be kept closed when it is not needed. Note that the gas ballast
is not equally effective on all different types of chemical vapours, so it may not always eliminate
condensation completely.
Should condensate form despite actuation of the gas ballast device, the suction port must be closed
and the pump operated with gas ballast for a lengthy period (about 2 hours).