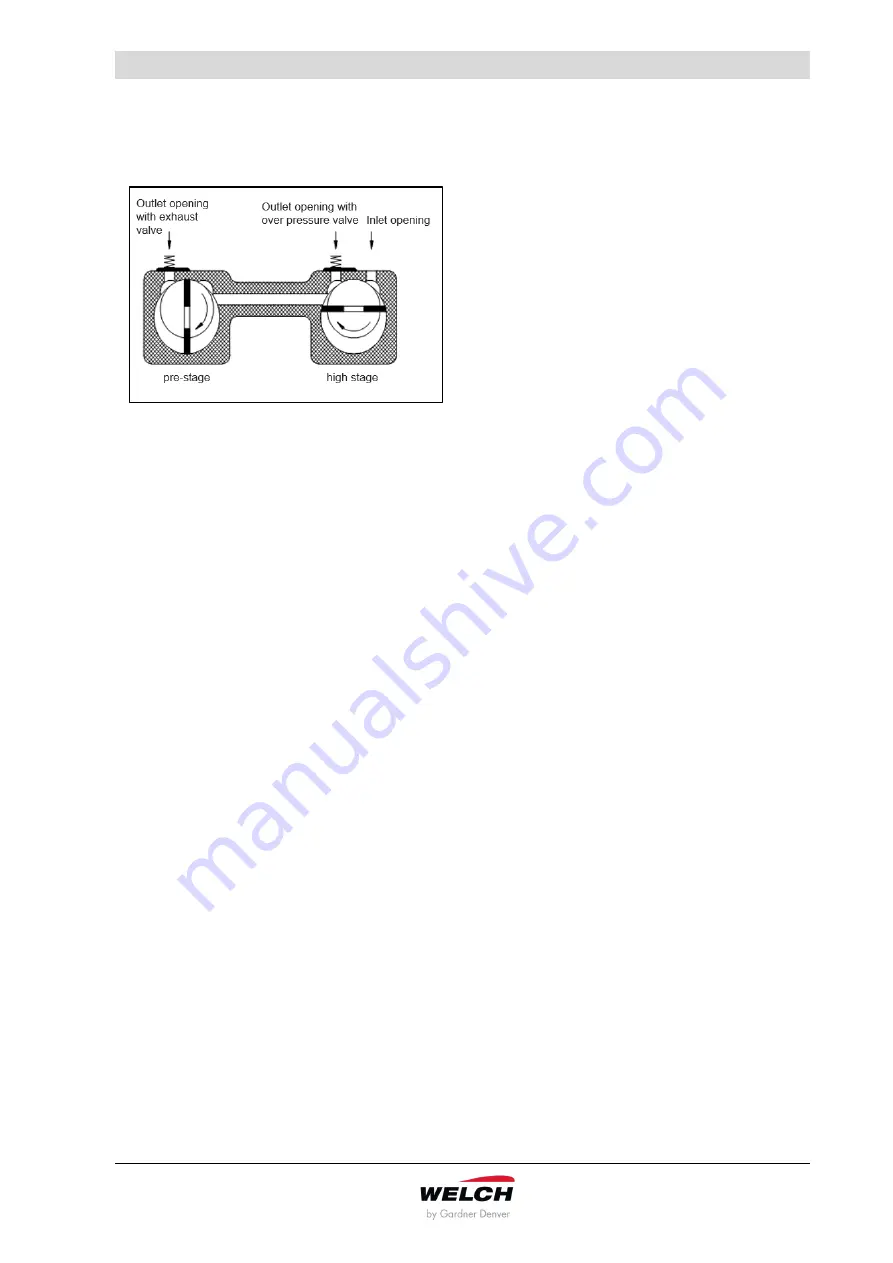
Description
P1700040
9
Two pump stages (fore-stage and high-stage) are arranged in series in order to improve the end
pressure and the pumping speed at lower pressures. The intake takes place in the first stage (high-
stage), the compression and the outlet in the second stage (fore-stage).
Fig. 3 Pre-stage / high stage
When in operation, the intake stage is at lower pressure and the exhaust stage is at higher pressure
relative to each other. Each stage contains a rotor assembly consisting of a rotor with two vanes and a
stator. The two rotors are combined on one shaft, and the two stators are combined in a common
housing. The pump shaft turns the rotors, causing the vanes in each chapter to sweep the surface of
their stators. The vanes are pressed against the stators by centrifugal force. Each stage has an
exhaust valve. Gas expelled from the first stage exhaust passes through an inter stage port to the
intake of the second stage. The second stage compresses the gas further, then expels it from the
second stage exhaust valve to the atmosphere. The oil carried along with the gas is separated out by
a filter (available accessory).
An adjustable gas ballast valve is located in the pump’s exhaust stage. The purpose of the gas ballast
is to prevent vapours condensing in the vacuum pump. A dosed quantity of air (gas ballast) can be let
into the pump body during the compression by opening the gas ballast valve. The function of the gas
ballast valve is described more in detail in chapter 3.4.7
“Gas Ballast”.
Effects of Continued Pressure Reduction
The quantity of gas in the vessel (6) is reduced with each evacuation cycle. The gas remaining in the
vessel expands to fill the vessel and consequently with each cycle the pressure in the vessel is
reduced. This is a manifestation of Boyle’s Law which states that, for a constant temperature, the
volume of a body of gas is inversely proportional to its pressure; i.e., if the volume is enlarged the
pressure must be reduced.
As the amount of gas in the vessel is steadily diminished, its pressure is correspondingly reduced. The
action of the pump must therefore compress a successively smaller quantity of gas with each cycle to
something greater than atmospheric pressure in order to expel it from the pump.
At the beginning of an evacuation sequence, the compression ratio is very small. In the first cycle of
operation the pump draws in a volume of gas at atmospheric pressure and expels it at approximately
atmospheric pressure. Since the exhaust valve is generally spring loaded to provide a good seal, the
pressure required to open it is somewhat greater than atmospheric pressure.
Ultimate Pressure
As described previously, a quantity of gas is removed from the system with each cycle of the pump.
Therefore, the pressure of the gas remaining in the system is reduced with each pump cycle. Since
the pump can remove only a small portion of the gas with each pump cycle, it is obvious that this
method of evacuation can never completely remove all the gas in the vessel. In addition to this, all the
components of the system contain minute sources of gas leakage which are impossible to seal
completely against atmospheric pressure. Outgassing of materials within the system provide additional
sources of gas.
As a result, after prolonged pumping, a state of equilibrium is reached in which the gas introduced
from all the leakage sources is balanced by the ability of the pump to remove gas from the system.