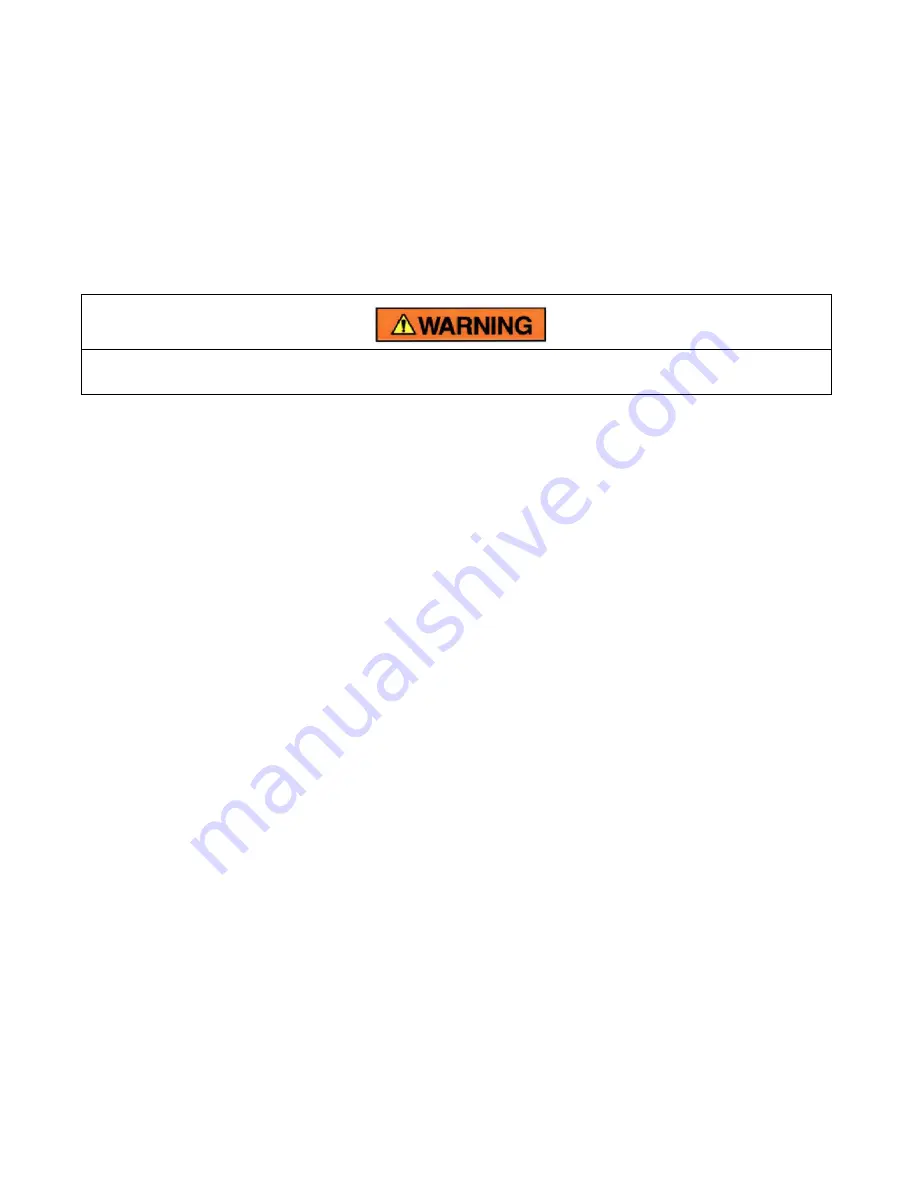
RB-7-100 Page 10
Blower inlet and outlet are temporarily capped to keep out dirt and other contaminants during shipment. These
covers must be removed before start-up.
The internal surfaces of all RBS units are mist sprayed with a rust preventative to protect the machine during
shipment. Remove this film upon initial startup, using any commercial safety solvent. Position the blower so that
the inlet and discharge connections are in the vertical position (vertical airflow). On vertically mounted units, it will
be necessary to lay the unit on its side supporting the ends of the unit so as not to restrict the port on the bottom
side. Place a shallow pan on the underside of the unit. With the blower disconnected from power, spray the
solvent in the top port, rotating the impellers by spinning the shaft manually. Continue this procedure until the unit
is visibly clean.
Rotating components will cause severe injury in case of personal contact. Keep hands and loose
clothing away from blower inlet and discharge ports.
Summary of Contents for RBS 15
Page 2: ......
Page 16: ...RB 7 100 Page 15 RBS OVERHUNG LOAD...
Page 26: ...RB 7 100 Page 25 SECTION 5 MAINTENANCE FIGURE 5 1 MAINTENANCE CHECK LIST...
Page 29: ...RB 7 100 Page 28 SECTION 7 PARTS LIST 7 1 RBS 15 25 Sectional drawing FIGURE 7 1...
Page 31: ...RB 7 100 Page 30 7 2 RBS 35 106 Sectional drawing FIGURE 7 2...
Page 34: ...RB 7 100 Page 33 7 3 RBS 115 225 Sectional drawing FIGURE 7 3...
Page 37: ...RB 7 100 Page 36 OVERHAUL KIT...
Page 38: ...RB 7 100 Page 37...
Page 39: ...RB 7 100 Page 38...
Page 41: ......