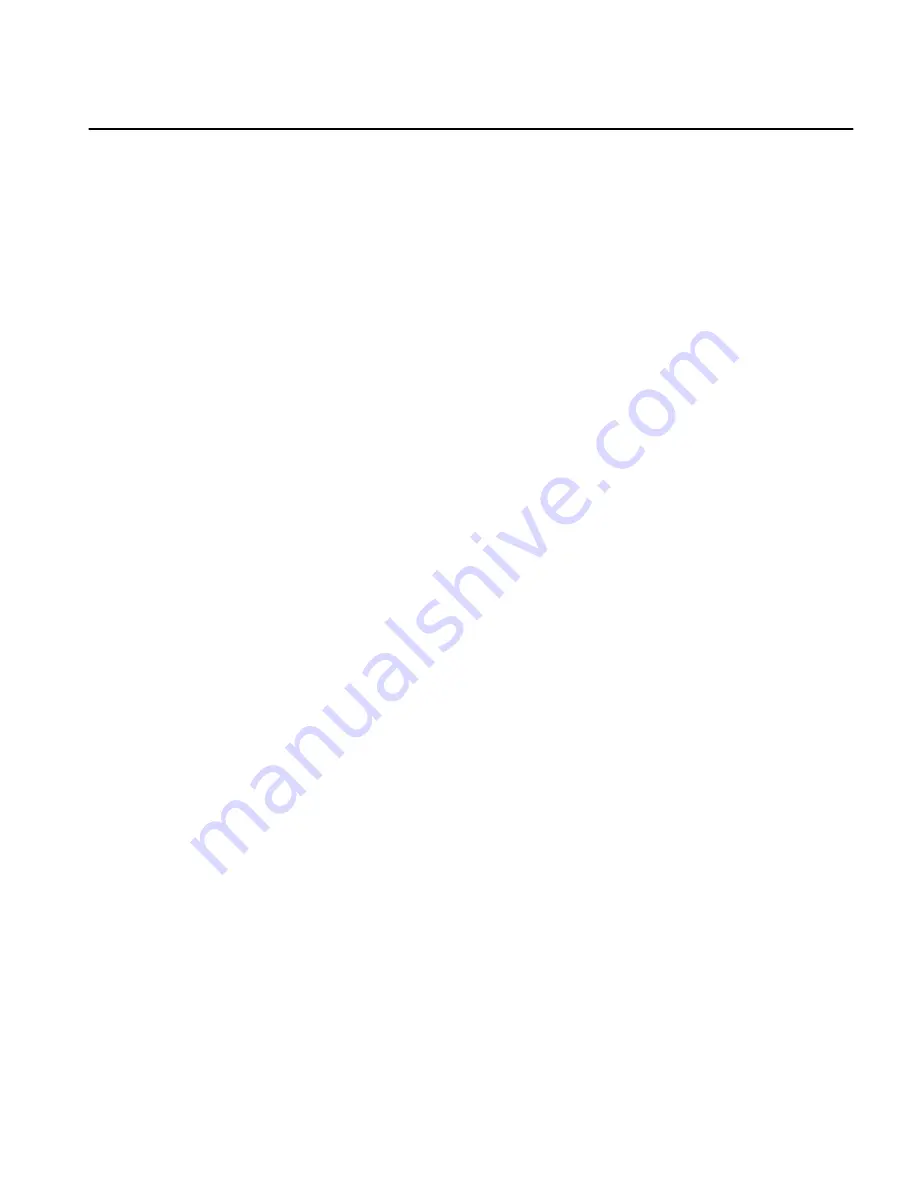
3-1-618 Page 24
PROBLEM
POSSIBLE
CAUSE SUGGESTED
ACTION
Cavitation, Fluid Knock or Hammer
5.
High fluid temperature or
5.
Reduce pump speed per
(continued).
viscosity.
chart
in
manual.
6.
High fluid vapor pressure.
6.
Increase NPSH.
7.
High acceleration head.
7.
Increase supply line size.
Decrease supply line length.
8.
Suction valve spring too stiff
8.
Use more flexible spring.
with
low
NPSH.
Remove inner spring from
two
spring
valve.
9.
Air/Gas in pumped fluid.
9.
Allow more settling time
in
supply
tank.
Reduce
pump
speed.
10. Air entering suction line.
10. Repair suction line.
11. Air entering charging pump.
11. Tighten or replace shaft
packing
or
seal.
12. Air entering or charge gas
12. Repair and recharge
escaping from suction stabilizer.
stabilizer.
13. Multiple pumps operating in
13. Use a suction stabilizer
phase.
on each pump. Separate
lines may also be needed.
Suction or Discharge Line Vibration.
1.
Line(s) not supported.
1.
Install supports or hangers.
2.
Pump cavitating.
2.
See Cavitation, Fluid Knock
or
Hammer
problem.
High Crankcase Oil Temperature.
1.
High ambient temperature.
1.
Use an oil heat exchanger
with a circulating pump.
2.
Improper type/grade oil used.
2.
Use recommended oil.
3.
Pump overloaded.
3.
Reduce pump speed and/or
pressure.
4.
Improper clearance in main or
4.
Check and adjust clearance.
rod bearings, crossheads or
Replace parts as required.
bushings.
Knock In Power End.
1.
Improper main bearing clearance. 1.
Check and adjust clearances.
2.
Incorrect pump rotation.
2.
Reverse rotation.
4.
Loose bearing housings/covers. 4.
Check and tighten. Replace
if
damaged.
5.
Worn crosshead pin.
5.
Replace.
6.
Worn crosshead pin bushing.
6.
Replace.
7.
Worn connecting rod to
7.
Replace.
eccentric
bearing.