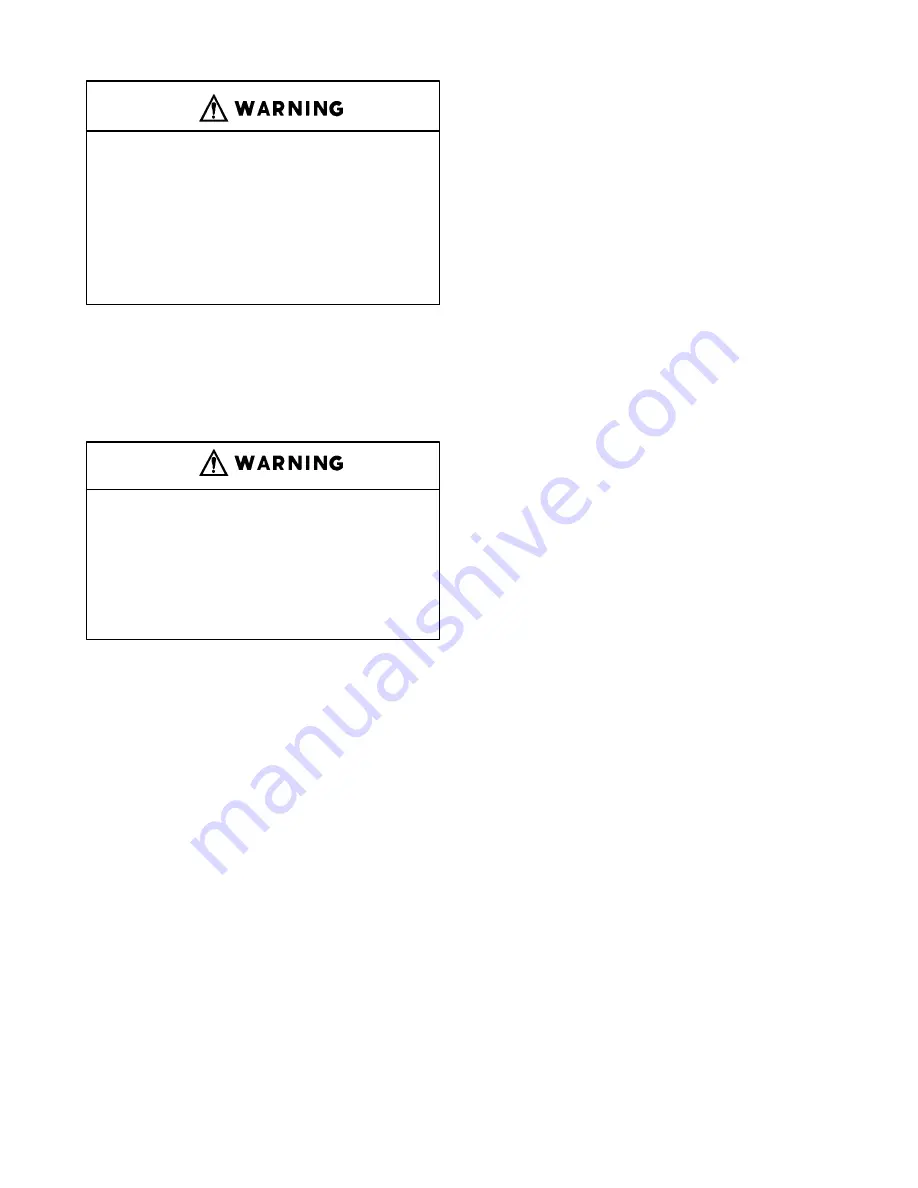
13–10–612 Page 17
Operation with incorrect motor rota-
tion can damage equipment and
cause oil eruption from the compres-
sor inlet. When checking motor rota-
tion, induce minimum rotation (less
than one revolution if possible). Nev-
er allow the motor to reach full speed.
9.
System Pressure – Set the controls to the de-
sired unload pressure and differential. DO NOT
EXCEED MAXIMUM OPERATING PRESSURE
ON THE COMPRESSOR NAMEPLATE. See
”Programming and Setup Instructions for the Auto
Sentry–ES
Controller, pages 27, 28 & 29.
Operation at excessive discharge air
pressure can cause personal injury or
damage to equipment. Do not adjust
the full discharge air pressure above
the maximum stamped on the unit
nameplate.
10. Operating Mode – Refer to Section 4 for detailed
information on the control system.
11. Enclosure – Check for damaged panels or doors.
Check all screws and latches for tightness. Be
sure doors are closed and latched.
STARTING THE UNIT – OBSERVE UNIT COLD OR
UNIT HOT STARTING PROCEDURES –
Unit Cold – If the unit is a water–cooled heat exchang-
er model, open any manual water inlet valves wide
open. Start the unit by pushing either the ”CONSTANT
RUN” button or one of the ”AUTO” buttons. Since the
unit is equipped with a minimum (65 psig) pressure dis-
charge valve, no special procedure to maintain unit res-
ervoir pressure is required.
Unit Hot – No warm–up period is required. If the unit
is a water–cooled heat exchanger model, open any
manual water inlet valves wide open. Start the unit by
pushing either the ”CONSTANT RUN” button or one of
the ”AUTO” buttons.
DAILY CHECK – Refer to Section 8, ”Maintenance
Schedule”.
STOPPING THE UNIT – Press ”STOP–RESET” but-
ton. The oil reservoir will automatically blow down as
the motor stops. If the unit is a water–cooled heat ex-
changer type, close any manual water inlet valves.
SEQUENCING COMPRESSORS
Sequencing compressors with the AUTO SENTRY–
ES controller is as simple as plugging in a telephone to
a wall jack. The only item required to make the system
functional is a standard telephone cable identical to
cables that connect nearly every telephone to its wall
jack. One less cable than the number of compressors
to be sequenced is required. For example, to sequence
four compressors, three cables are required. A kit,
200EAP752, is available which contains all material
needed to sequence up to five compressors. This kit
contains 500 feet of cable, eight modular connectors
and a crimping tool to install the connectors.
In spite of the fact that it is a standard feature, and its
inherent installation simplicity, the sequencing function
of a multi–compressor ”AUTO SENTRY–ES” system is
the most fully–featured, functionally–complete control
available today.
I.
INSTALLATION
A proper sequencing installation requires two or more
Gardner Denver rotary air compressors complete with
”AUTO SENTRY–ES” controllers, piped into a com-
mon air system, interconnected as described above.
All standard practices common to sound air compres-
sor installations such as proper sizing of discharge pip-
ing, proper electrical supply and conductor sizing, and
grounding are to be observed. The serial communica-
tions interface meets RS–485 standards, the most
widely used interface in harsh, industrial environments
today. However it is still recommended that the com-
munications cables be routed through metallic conduit
to provide them with both mechanical protection and
electromagnetic shielding.
Each control circuit board has two modular jacks which
accept standard RJ–12 telephone plugs. One jack is
Summary of Contents for ELECTRA-SAVER EAU PD - 200 HP
Page 13: ...13 10 612 Page 3 FIGURE 1 4 STARTER BOX FIGURE 1 5 PACKAGE CONTROLLER AND STARTERS...
Page 16: ...13 10 612 Page 6 DECALS 206EAQ077 212EAQ077 218EAQ077 211EAQ077 207EAQ077...
Page 17: ...13 10 612 Page 7 DECALS 216EAQ077 217EAQ077 222EAQ077 221EAQ077 208EAQ077...
Page 40: ...13 10 612 Page 30 FIGURE 4 8 CONTROL SCHEMATIC COMPRESSOR AT FULL LOAD 214ECM797 Ref Drawing...
Page 42: ...13 10 612 Page 32 FIGURE 4 10 WIRING DIAGRAM 212EAP546 Ref Drawing...
Page 43: ...13 10 612 Page 33 FIGURE 4 11 AUTO SENTRY ES CONTROLLER DISPLAY...
Page 45: ...13 10 612 Page 35 FIGURE 5 1 FLOW DIAGRAM AIR OIL SYSTEM 215EAU797 Ref Drawing...
Page 65: ......