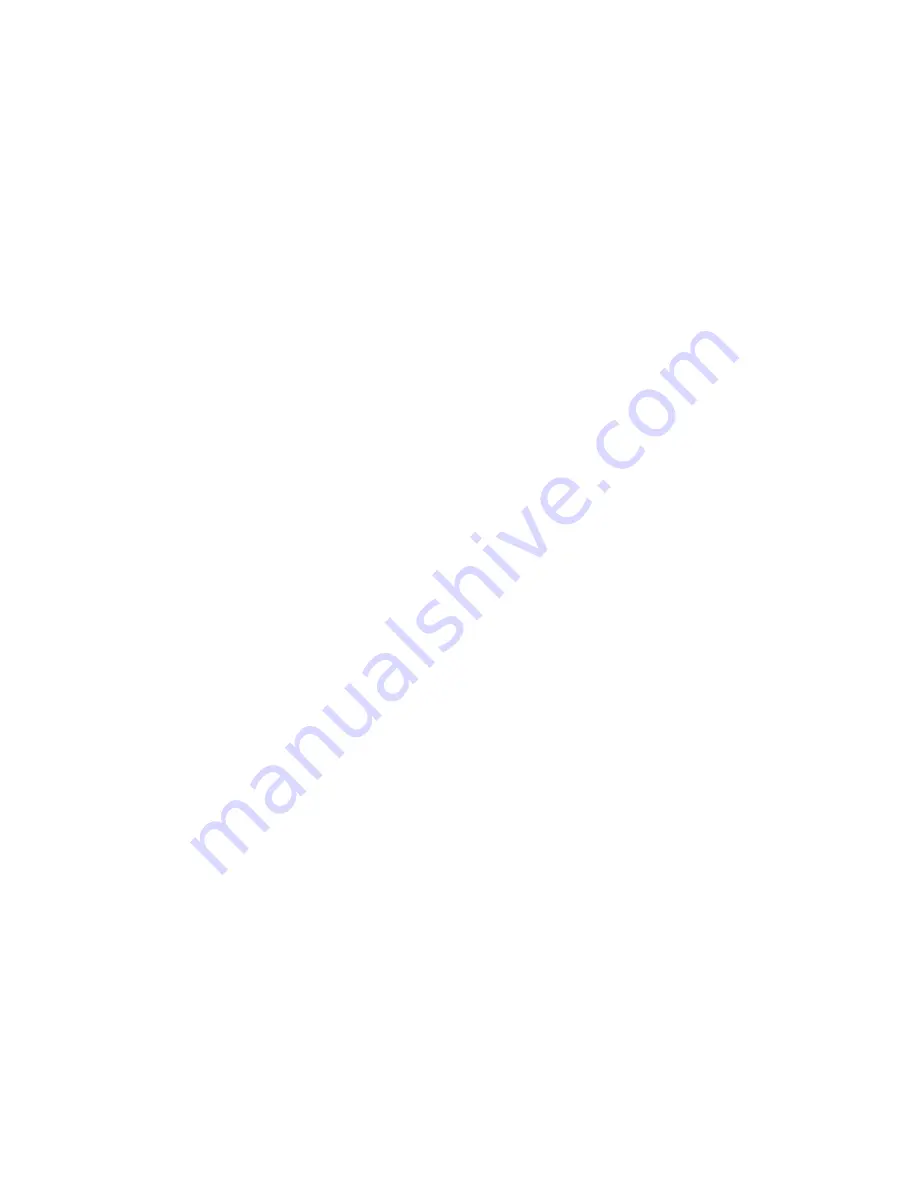
13-9-653 Page 6
Main Adjustments Menu
1. The compressor must be stopped prior to making any adjustments. If the unit is running, press the
[STOP/RESET] key to place the control in the
"READY"
state.
2. Adjustments can also be performed from the
"SHUTDOWN"
state. After adjustments are completed, the
controller returns to the this state until the cause is repaired and the controller is manually reset.
3. Press the [ENTER] key to begin programming. This enters the adjustments menu. The adjustments are broken
into five groups as shown in
figure 1-2.
To select a group, press [+] or [-] until the desired group is shown on the
bottom line of the display. Press [ENTER] to proceed to the group adjustments detailed below.
Note: Configuration adjustments are normally required only at the time of assembly or after parts have been
replaced. Unit setup adjustments are normally required only at the time of unit installation. To prevent accidental
access, these will not be available if the "SET" switch is in the position closest to the corner. The "SET" switch is
located on the bottom of the controller chassis, on the side behind the program keypad area. If the switch is towards
the center of the controller, all five adjustment sections are accessible.
Operation Adjustments
1. In the top line,
"LANGUAGE"
is indicated. The bottom line will indicate
"ENGLISH"
or an alternate language for
display messages. Select the desired display language and press [ENTER] to proceed.
If a controller is set for another language, press the [STOP/RESET] key, press [ENTER] twice, and press the [+]
or [-] key to select ENGLISH at this step. Then press [ENTER] to select the language.
2. In the top line,
"DISPLAY UNITS"
is indicated. The bottom line will indicate
"ENGLISH"
(PSIG, Fahrenheit) or
"METRIC"
(Bars, Celsius) units of measurement. Select the desired display units and press [ENTER] to
proceed.
3. In the top line,
"START TIMER"
is displayed. The bottom line will indicate a time between 3 and 10 seconds.
This is the time that the controller spends in the unloaded 'start' mode. This also controls the operation of
package-mounted wye-delta starters, if so equipped. Set this adjustment for the amount of time needed for the
motor to reach its highest speed while starting. This is typically 3 seconds for full-voltage starters, 7-9 seconds
for wye-delta starters.
If a remote-mounted, reduced voltage starter is used, set this adjustment 1-2 seconds longer than the starter's
internal timer.
4. In the top line,
"SET PRESSURE"
is displayed. The bottom line will indicate a pressure value. It is to be set at
the nameplate rating of the compressor for normal operation.
Under NO circumstances
, is this adjustment to
be set in excess of the compressor nameplate pressure. It may be set lower, if desired, to reduce pressure and
power consumption.
5. In the top line,
"RESET PRESSURE"
is displayed. The bottom line will indicate a pressure value. This setting
determines the point at which machine startup occurs in AUTO and SEQUENCE modes and when the
compressor will load up from the blown down condition. Note that RESET PRESSURE can be set up to 5 PSI
below SET PRESSURE. Set this lower to reduce compressor cycling. All sequenced machines must have the
same SET and RESET PRESSURE setpoints.
6. In the top line,
"BLOWDOWN TIME"
is displayed. The bottom line will indicate a time between 1 and 20
minutes. It is factory set at 10 minutes. This is the minimum time interval between blowdowns. A longer
blowdown time minimizes wasteful dumping of compressed air when loading is likely to occur in a short time.
7. In the top line,
"AUTO TIME"
is displayed. The bottom line will indicate a time between 1 and 20
minutes. It too, is factory set at 10 minutes. Its function is to prevent too frequent motor starting, and
to allow the motor a 'cool-down' period before stopping.
8.
"IV CONTROL MODE"
is displayed on the top line. Select
"MODULATING"
for standard operation.
"LOAD-UNLOAD"
may be selected for systems with large storage and wide pressure differential.
9. In the top line,
"REMOTE HALT"
is displayed. The bottom line indicates either
"TIMED"
or
"IMMEDIATE"
. Refer to the description of "Remote On / Off" later in this section for additional
details. Select the desired response to the remote input and press [ENTER] to proceed.
Summary of Contents for AUTO SENTRY-ES+
Page 19: ...13 9 653 Page 15 Figure 1 3 WIRING DIAGRAM 216EAP546 B Ref Drawing Page 1 of 2...
Page 20: ...13 9 653 Page 16 216EAP546 B Ref Drawing Page 2 of 2...
Page 21: ...13 9 653 Page 17 Figure 1 4 WIRING DIAGRAM 304EBH546 C Ref Drawing Page 1 of 2...
Page 22: ...13 9 653 Page 18 304EBH546 C Ref Drawing Page 2 of 2...
Page 23: ...13 9 653 Page 19 Figure 1 5 WIRING DIAGRAM 301EAQ546 B Ref Drawing Page 1 of 2...
Page 24: ...13 9 653 Page 20 301EAQ546 B Ref Drawing Page 2 of 2...