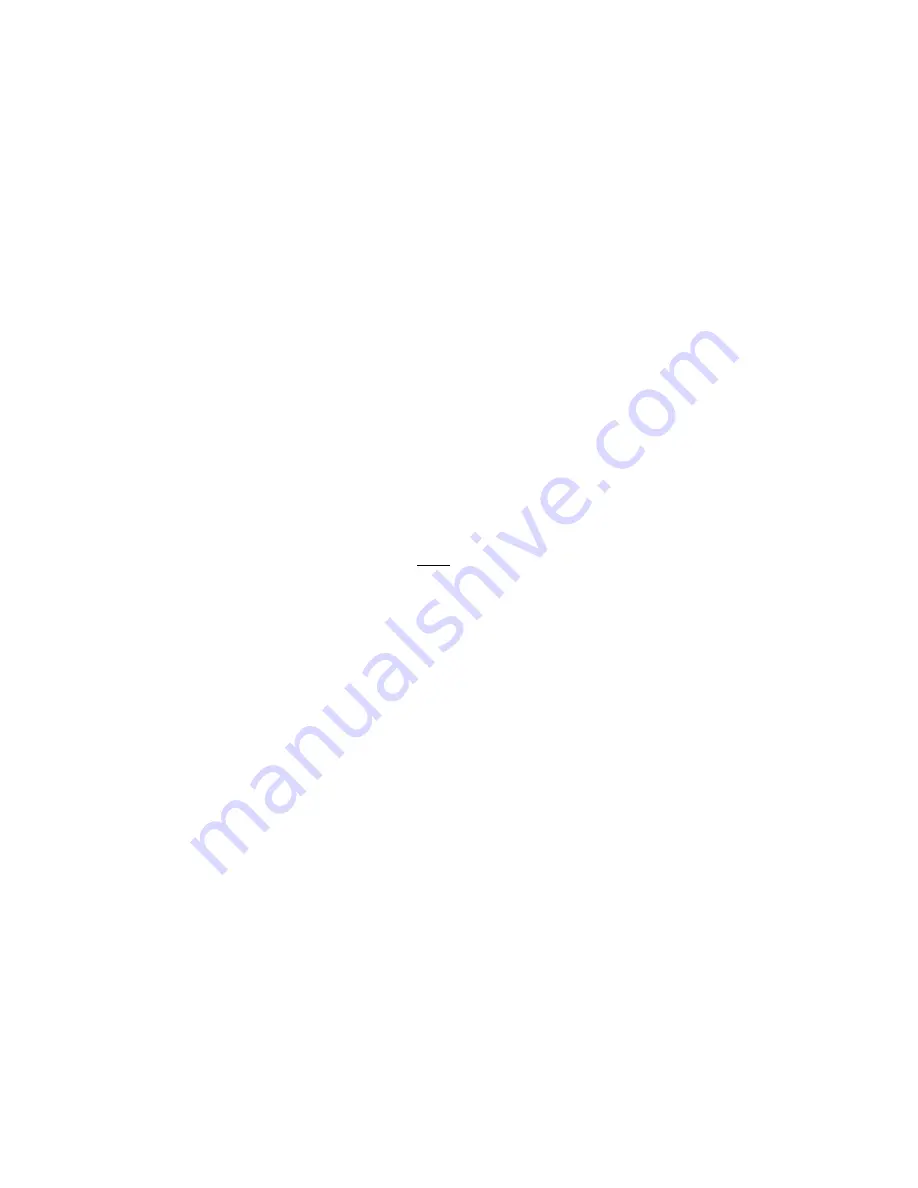
3 - 2
walls of the cell. This is especially true near the working electrode, which may represent the major heat
escape pathway. It is not unusual to find the electrolyte temperature near the working electrode is of 5-
20
°
C lower than that of the bulk of the electrolyte.
If you cannot prevent thermal inhomogenieties, you can at least minimize their effects. One important
design consideration is the placement of the RTD used to sense the cell temperature. You should get the
RTD as close as possible to the working electrode. This will minimize the error between the actual
temperature at the working electrode and the temperature setting.
A second problem concerns the rate of temperature change. You would like to have the rate of heat
transfer to the cell's contents high, so that changes in the cell's temperature can be made quickly. A more
subtle point is that the rate of heat loss from the cell should also be high. If it is not, the controller risks
gross overshoots of the set point temperature when it raises the cell temperature. Ideally, the system will
actively cool the cell as well as heat it. Active cooling can consist of a system as simple as tap water flow
through a cooling coil and a solenoid valve.
Temperature control via an external heater such as a heating mantle is moderately slow. An internal
heater, such as a cartridge heater is often quicker.
Tuning the TDC4 Temperature Controller -- Overview
Closed loop control systems such as the TDC4 must be tuned for optimal performance. A poorly tuned
system will suffer from slow response, overshoot and/or poor accuracy. The tuning parameters depend
greatly on the characteristics of the system being controlled.
The temperature controller in the TDC4 can be used in an ON/OFF mode or a PID (Proportional, Integral,
Derivative) mode. The ON/OFF mode uses hysteresis parameters to control its switching. The PID mode
uses tuning parameters. The controller in PID mode reaches the set point temperature quickly without
much overshoot and maintains that temperature within a closer tolerance than the ON/OFF mode.
When to Tune
The TDC4 is normally operated in PID (proportional, integrating, derivative) mode. This is a standard
method for process control equipment than allows for rapid changes in the set parameter. In this mode
the TDC4 must be tuned to match it to the thermal characteristics of the system that it is controlling.
It is shipped configured for PID control mode. You must explicitly change it to operate in any other
control mode.
The TDC4 is initially configured with parameters appropriate for a Gamry Instruments Flex Cell heated
with a 300 W jacket and cooled using solenoid valve controlling water flow through a cooling coil. The
tuning settings are described below:
Summary of Contents for TDC4
Page 15: ...2 6...