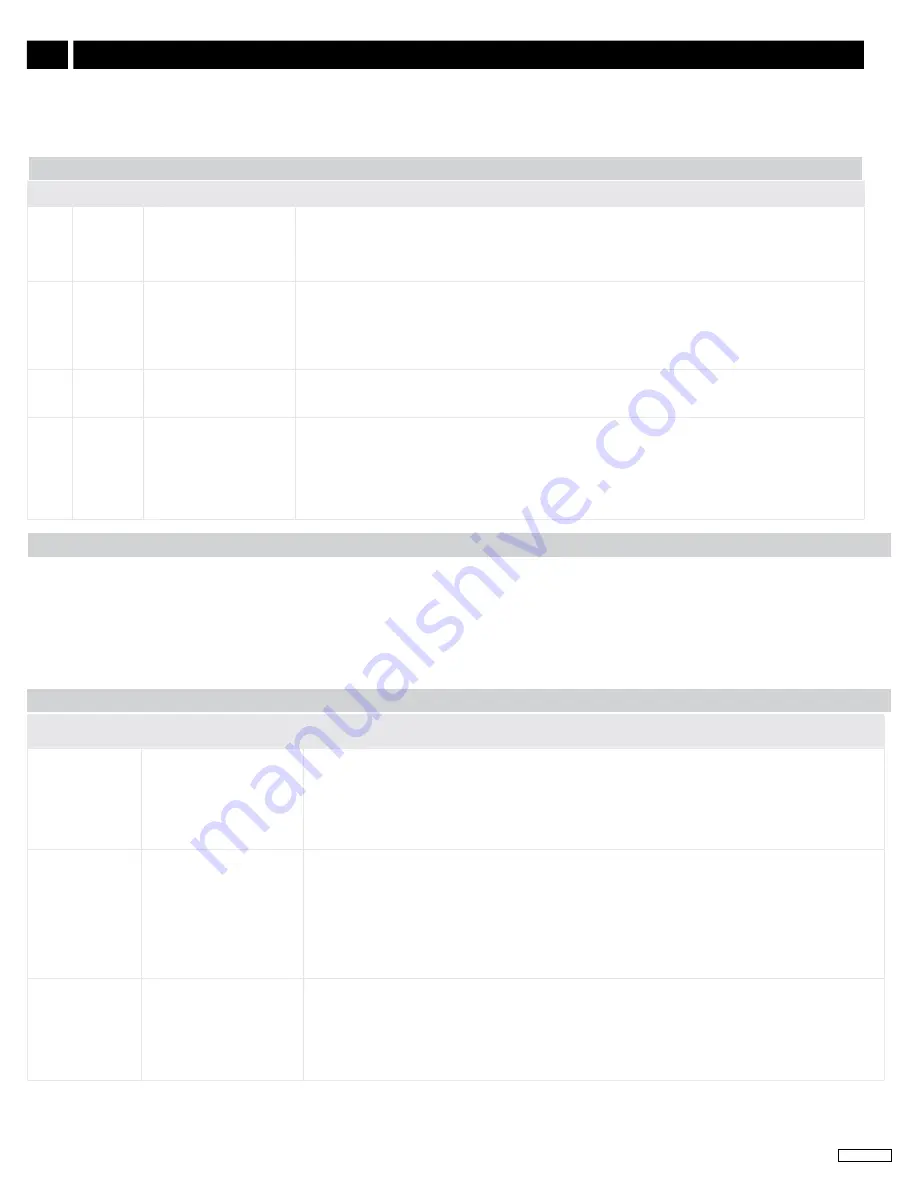
8
Governors America Corp. © 2020 Copyright All Rights Reserved
ESD5500E Series Speed Control Unit 9-2020-F PIB1002
SteP
WIreS
cHecK
ProBaBLe cauSe
1
F(+) & E(-)
Battery Supply
Voltage
(12 or 24 V DC)
1. DC battery power not connected. Check for blown fuse.
2. Low battery voltage
3. Wiring error
2
C(+) & D(-) 1.0 V AC RMS min. while
cranking
1. Gap between speed sensor and gear teeth too great. Check Gap.
2. Improper or defective wiring to the speed sensor. Resistance between D and C should be 160 to
1200 Ω. See your specific mag pickup data for resistance.
3. Defective speed sensor
3
P(+) & G(-) 10 V DC, Internal Supply
1. Short on Terminal P
2. Defective speed control unit
4
F(+) & A(-)
1.0 - 2.0 V DC while
cranking
1. SPEED potentiometer set too low
2. Short/open in actuator wiring
3. Defective speed control
4. Defective actuator, see your actuator manual for troubleshooting
SYStem InoPeratIve
12
TROUBlEShOOTINg
If the engine governing system does not function, the fault may be determined by performing the voltage tests described in Steps 1 through
4. Positive (+) and negative (-) refer to meter polarity. Should normal values be indicated during troubleshooting steps, and then the fault may
be with the actuator or the wiring to the actuator. Tests are performed with battery power on and the engine off, except where noted. See your
actuator publication for actuator testing procedures.
InSuffIcIent maGnetIc SPeeD SIGnaL
A strong magnetic speed sensor signal eliminates the possibility of missed or extra pulses. The speed control unit will govern well with 1.0 V RMS
speed sensor signal. A speed sensor signal of 3 V AC or greater at governed speed is recommended. Measurement of the signal is made at
Terminals C and D.
The amplitude of the speed sensor signal can be raised by reducing the gap between the speed sensor tip and the engine ring gear. The gap
should not be any smaller than 0.02 in [0.5 mm]. When the engine is stopped, back the speed sensor out by 3/4 turn after touching the ring gear
tooth to achieve a satisfactory air gap
.
InStaBILItY
InStaBILItY
cHecK
ProBaBLe cauSe
Fast Periodic
The engine seems to jitter
with a 3 Hz or faster irregu-
larity of speed.
1. Make sure switch C1 is set to OFF.
2. Readjust the GAIN and STABILITY for optimum control.
3. Remove the E1 to E2 jumper. Readjust GAIN and Stability afterward.
4.
Turn off other electrical equipment that may be causing interference.
Slow Periodic
An irregularity of speed
below 3 Hz.
1. Readjust the GAIN and STABILITY
2. Adjust the DEAD TIME COMPENSATION by adding a capacitor from posts E2 to E3 (negative on
E2). Start with 10 mF and increase until instability is eliminated.
Check fuel system linkage during engine operation for:
•
binding
•
high friction
•
poor linkage
Non-Periodic
Erratic Engine Behavior
Increasing the GAIN should reduce the instability but not totally correct it.
If this is the case, there is most likely a problem with the engine itself. Check for:
•
engine mis-firings
•
erratic fuel system
•
load changes on the generator set voltage regulator
If throttle is slightly erratic, but performance is fast, move switch C1 to the OFF position.