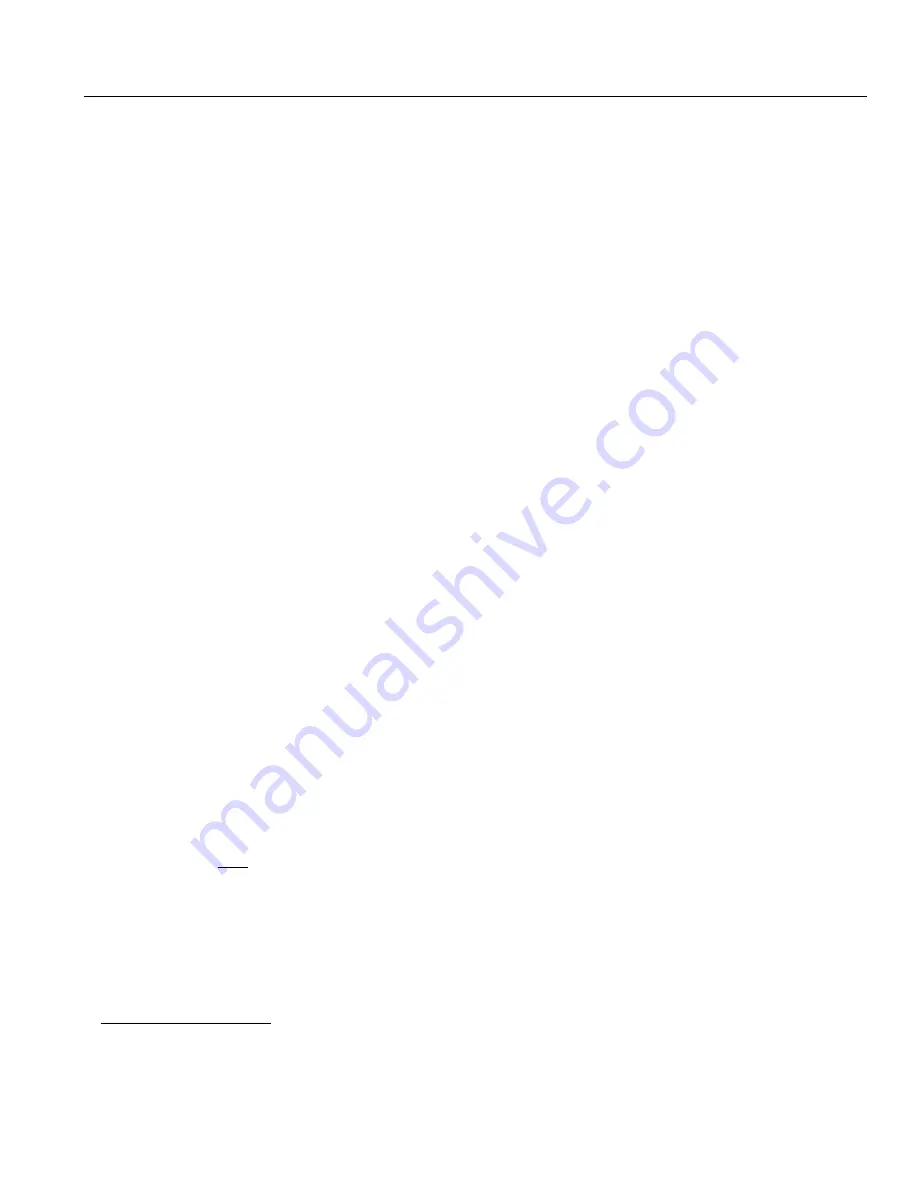
Sequence of Operation
for Modulated Pulse
Water Heaters
1. When the water heater receives a call
for heat, the prepurge cycle is initiated.
2. The mod motor is driven to high fire.
3. After the high fire switch in the mod
motor is closed, the prepurge count
begins.
4. Following prepurge, the spark
generator energizes and the gas valves
open.
5. Upon proof of flame, the fan and spark
are turned off.
6. At this point, the modulation
temperature controller controls the mod
motor and firing rate of the water heater.
7. When the water heater outlet
temperature reaches set point, the water
heater is turned off and prepurge begins.
8. The water heater control then monitors
the outlet temperature and waits for the
next call for heat.
NOTE
A series of relays are used in the above
sequence of operation. Please refer to
the wiring diagram for details.
Programming Instructions
for Yokogawa UT320
Standard Program
1. Hold SET/ENT key until control is in
Operator mode. PV display will show
oppa.
2. Press Down Arrow key until control is in
Set Up mode. PV display will show
stup
.
3. Press SET/ENT key twice until control
is in Function mode. PV display will show
func.
4. Press Down Arrow key until control is in
Input/Output mode. PV display will show
I/o.
5. Press SET/ENT key to bring you to the
first parameter in the Input/Output mode.
Parameter Setting Procedure: The
values for each parameter that are
shown in the PV display should match
the values entered at the factory. If
they differ, press the Up Arrow key or
Down Arrow key until the factory value
is displayed. Some values, such as
High Temperature Range
(rh)
, can be
adjusted according to system design.
Once the desired value is displayed,
press the SET/ENT key to maintain it in
the control’s memory.
Only those values that are Shaded with
Bold & Italic values in the menu pertain
to the program constructed for Fulton
pulse water heaters.
NOTE
It is important to know that if the
following parameters are altered, the
entire set of factory values will be
altered: (In) or (UNIT) located in the
Input/Output Menu; (AL1) in the
Functional Parameters Menu; (A1) in
the Operating Parameters Menu.
6. After the Input/Output values have
been confirmed or entered, return to
Function mode by holding the SET/ENT
key until the PV display shows
func
.
Repeat Parameter Setting Procedure.
The
HY1
parameter or Hysteresis
may be adjusted to overshoot the
setpoint temperature by half the value
of
A1
entered. The unit will also start
again only after the supply tempera-
ture decreases half the value entered
below setpoint.
7. After the Function values have been
confirmed or entered, hold the SET/ENT
key until the Setpoint Temperature
appears in the PV Display.
8. Repeat the last step until the control
is in Operator mode. The PV Display will
show
oppa
. Repeat Parameter Setting
Procedure.
9. When the
PID
parameter appears in
the PV Display, press one of the Arrow
keys until
(1)
appears in the SP Display,
press SET/ENT--this will take you to a
subset of parameters. Repeat
Parameter Setting Procedure.
10. After confirming or entering the
PID
value
(1.MR)
, the control automatically
returns to the remaining Operating
parameters. Repeat Parameter Setting
Procedure.
11. When finished, hold SET/ENT key to
return to Setpoint Temperature. Water
heater is ready for operation.
NOTE
If the rh (Range High) value has been
changed in the Input/Output Menu,
the Setpoint Temperature will read
zero (0) after return from the menus.
Simply press the Up Arrow key until
the desired setpoint value is shown.
Hit SET/ENT once to store and begin
operation.
Worksheets
Use the worksheets to record the values
set at site under
Customer Value
. If the
unit is not operating correctly, call your
Fulton representative. Have your
customer values handy for trouble
shooting.
Advanced Programming
Features
The Yokogawa UT320 is a sophisticated
temperature control with “smart” features
that internally calculates how close the
appliance is to setpoint and adjusts it
proportionally to arrive without
overshooting. The smart logic must be
initiated in the Operating parameters by
setting the following values:
1. Under the Functional Parameters
menu, scroll to
HY1
and set the value to
20.
2. When the process temperature is within
10
o
F of the setpoint temperature, scroll to
AT
in the Operating Parameters menu
and set the value to 1.
3.
AT
or Auto-Tune will increase the
modulation (mod) motor output to 100%
until the process temperature is 2% of
input span above setpoint. The output will
go to 0% until the process temperature
decreases to 2% of input span below
setpoint.
4. The control will increase the mod motor
again to 100% until the process
temperature is 2% of input span above
setpoint. During this time the manual
mode light on the temperature control will
be flashing until completed.
5. If the three samples are not the same,
an error message will be displayed and
the temperature will drop out of Auto-Tune
mode. Reset the zero and span
adjustments on the mod motor and/or
adjust modulation linkage accordingly.
6. PID values will be set when this
procedure is successfully completed.
7. Repeat Step 1 and change the
HY1
value back to 10 (standard).
8. Scroll under Operating Parameters to
SC
(Super Function) and adjust the value
to “on”. This parameter works with Auto-
Tune in calculating the target setpoint.
9. Return to Auto mode.
Operation
30-PDWH
Summary of Contents for PDWH1000
Page 5: ...Section 1 Safety Warnings and Precautions 3 PDWH...
Page 9: ...Section Installation 7 PDWH 2...
Page 28: ...PAGE INTENTIONALLY LEFT BLANK...
Page 29: ...3 Operation Section 26 PDWH...
Page 37: ...Section 4 Maintenance 34 PDWH...
Page 41: ...Section 5 Parts and Warranty 38 PDWH...
Page 42: ...PAGE INTENTIONALLY LEFT BLANK...
Page 46: ...PAGE INTENTIONALLY LEFT BLANK 42 PDWH...
Page 48: ...PAGE INTENTIONALLY LEFT BLANK...
Page 49: ...PAGE INTENTIONALLY LEFT BLANK...