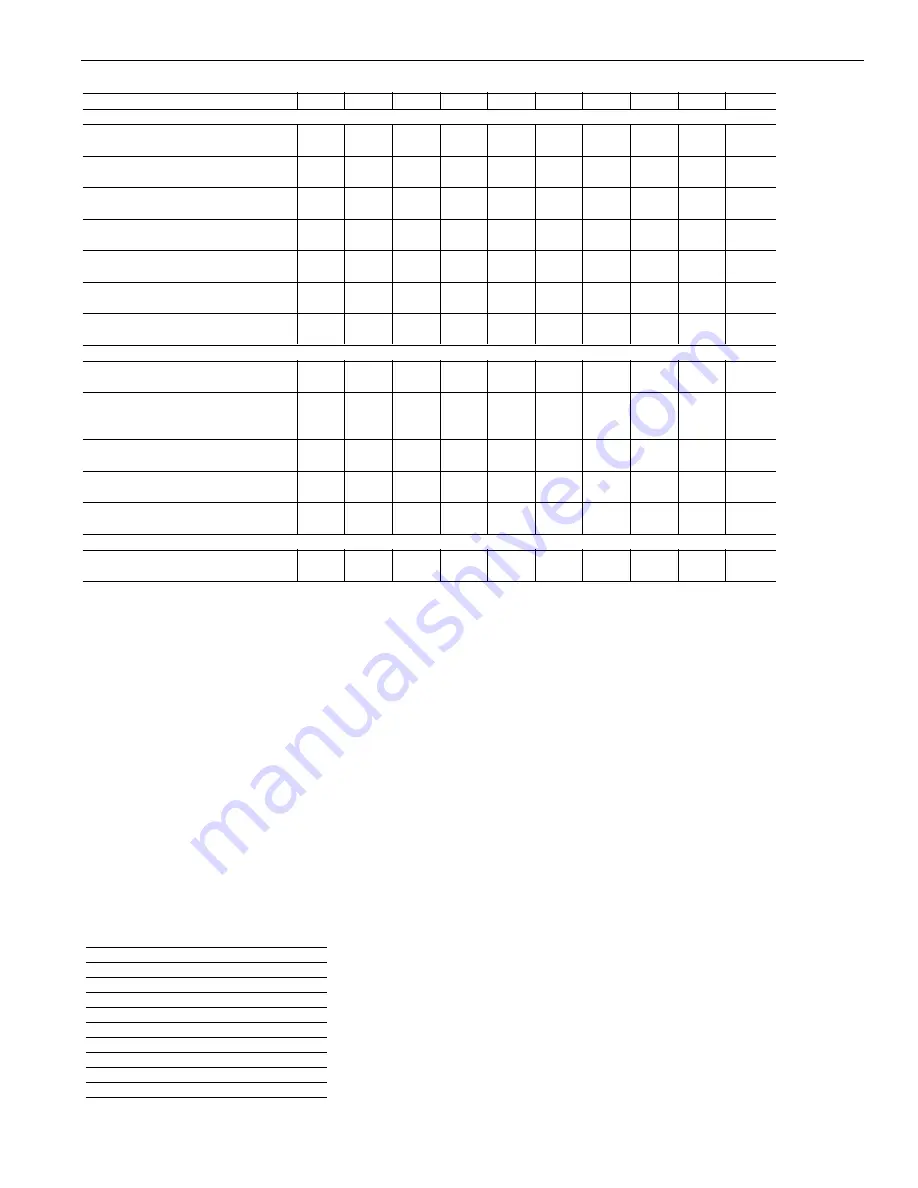
Description/Instructions
Locating the Boiler
a
) The boiler should be located in dry
surroundings on a level base, making
sure that there is sufficient room
around the boiler to enable the opera-
tor and/or the maintenance engineer
to gain access to all parts of the boiler.
Check location for ease of water sup-
ply and electrical connections.
b)
Place the boiler on a non combus-
tible floor with clearances to unpro-
tected combustible materials, includ-
ing plaster or combustible supports.
c)
It is necessary to have the follow-
ing vertical clearance from the floor to
the ceiling for removal of the burner
for servicing:
Minimum Vertical Clearances
BHP
IN
MM
6
82
2083
9.5
86
2184
10
86
2184
15
92
2337
20
9
2 2
438
30
106
2692
40
104
2642
50
114
2896
60
124
3
150
The Gas Supply
a)
Gas Piping should be installed in
accordance with National Fuel Gas
Code, ANSI-Z223-1-1984 or latest
addenda and any other local codes
which may apply. In Canada gas
installations must be in accordance
with the current CAN/CGA B149.1
and .2 and/or local codes.
b)
Install a dirt trap ahead of all of the
gas valves.
c)
The pipe and the fittings used
must be new and free of dirt or other
deposits.
d)
The piping must be of the proper
size to ensure adequate gas supply to
the gas head assembly. Consult your
gas company for specific recommen-
dations.
e)
For natural gas a pressure of 7" to
11" (178mm to 279mm) of water col-
umn pressure at the gas train is
required with burner firing. Do not
exceed 13" of water column.
f)
For propane or butane gas the
pressure required is 11" (279 mm) of
water column pressure. Again, do not
exceed 13" of water column.
g)
When making gas piping joints,
use a sealing compound resistant to
the action of liquefied petroleum
gases. Do not use teflon tape on
gas line threads.
h)
The main and the pilot gas pres-
sure regulators must be vented to the
atmosphere.
i)
After gas piping is completed care-
fully check all piping connections, (fac-
tory and field), for gas leaks. Use a
soap and water solution.
CAUTION
Some soaps used for leak testing
are corrosive to certain types of
metals. Rinse all piping thoroughly
with clean water after leak check
has been completed.
j)
The boiler must be disconnected at
the boiler shut off valve from the gas
supply piping system during any pres-
sure testing of the system at pressure
in excess of 1/2 PSIG--14" W.C.
k)
The boiler must be isolated from
the gas supply piping system by clos-
ing the shut-off cock during any pres-
sure testing of the gas supply piping
system at pressures equal to or less
than 1/2 PSIG--14" W.C.
31-G 1/01
SEE PRODUCT DATA SUBMITTAL ON
PREVIOUS PAGES
72
1828
4
Summary of Contents for FB-A 10
Page 2: ......
Page 4: ......
Page 6: ......
Page 8: ...2 G 1 01...
Page 9: ...Safety Warnings Precautions 1 3 G 1 01...
Page 10: ...4 G 1 01...
Page 12: ...6 G 1 01...
Page 13: ...7 G 1 01 Description Instructions LE...
Page 14: ...8 G 1 01...
Page 17: ...11 G 1 01 Operation LE...
Page 18: ...12 G 1 01...
Page 20: ...14 G 1 01...
Page 21: ...15 G 1 01 Maintenance LE...
Page 22: ...16 G 1 01...
Page 29: ...23 G 1 01 Parts LE...
Page 30: ...24 G 1 01...
Page 32: ...26 G 1 01...
Page 33: ...Boiler Description Instructions Gas Fired Boiler 2 27 G 1 01...
Page 37: ...30 G 1 01 Description Instructions I E K K J K D C H B A G F...
Page 50: ...42b G 1 01...
Page 51: ...43D G 1 01 Operation 3...
Page 52: ...43b G 1 01...
Page 59: ...Maintenance 4 5 G 1 01...
Page 60: ...51 G 1 01...
Page 73: ...Parts 5 6 G 1 01...
Page 88: ...79 G 1 01 Parts...
Page 90: ...81 G 1 01 Parts Gas Burner Ignition Assembly Gas Burner Components...
Page 95: ...Warranty 6 8 G 1 01...
Page 96: ...87 G 1 01...
Page 98: ...89 G 1 01...
Page 100: ...91 G 1 01...
Page 101: ...Component Data Sheets 7 G 1 01...
Page 102: ......