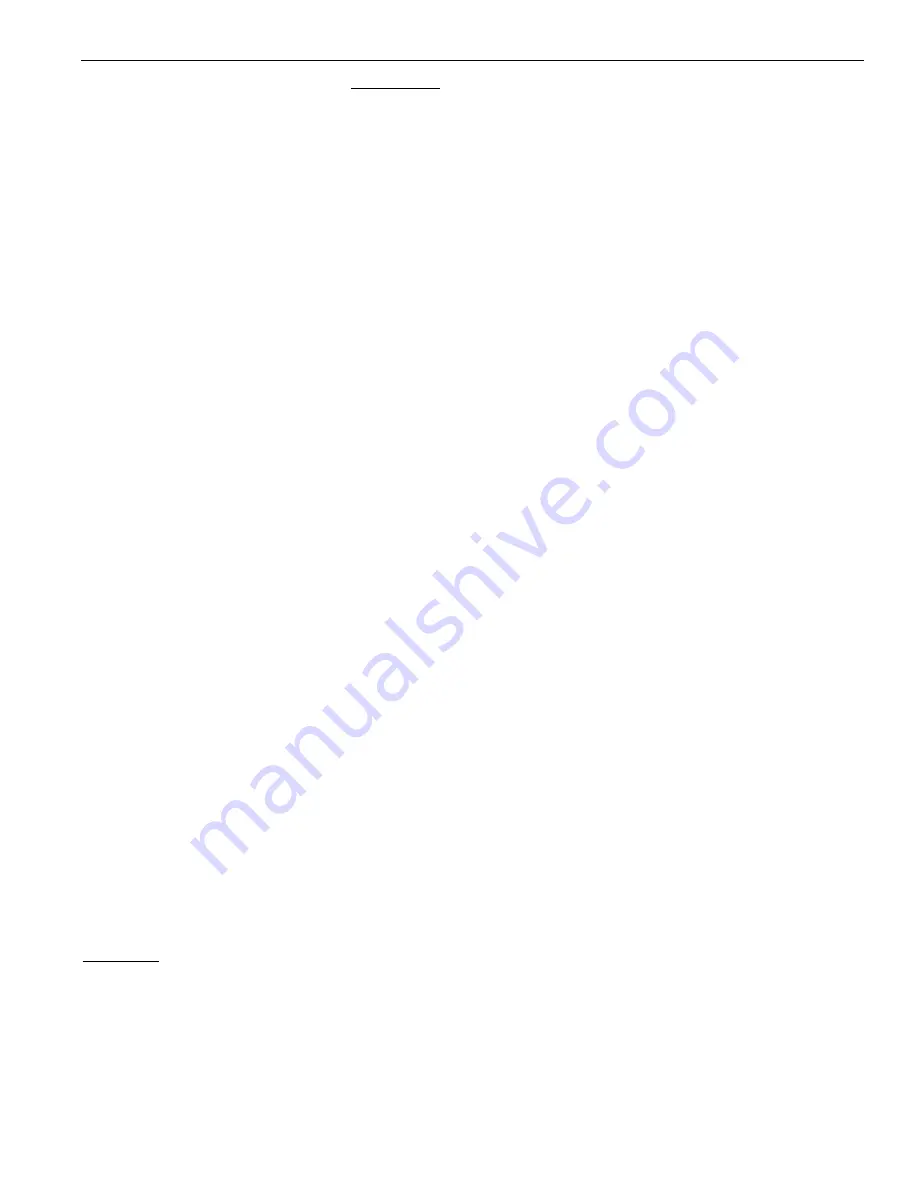
Water Supply
a)
Feed water contains solids and
dissolved gases. These may promote
incrustation of scale; foaming, prim-
ing, surging, and solids in steam; cor-
rosion and pitting; or caustic embrittle-
ment. To prevent this, feedwater must
be studied individually and treated
accordingly by reputable profession-
als specializing in this field. It is
strongly recommended that a compe-
tent water treatment company be con-
sulted prior to the installation of the
boiler.
b)
The purpose of this treatment
should be to provide quality feedwater
to the boiler such that corrosion and
deposition in the boiler will be mini-
mized. Dissolved oxygen, high chlo-
ride levels and low pH can all be
major causes of corrosion. Untreated
hardness is the major cause of
deposits. Poor quality feedwater
requires increased blow off and
increased chemical treatment costs to
prevent boiler corrosion and scaling.
c)
One way to lower the amount of
dissolved oxygen in the boiler feed
water is the sparge tube option. This
option injects live steam into the
feedwater to increase the water
temperature to 180 degrees F
(82 degrees C) which removes
oxygen from the water.
d)
Chlorides can be controlled by
increasing the number of blow downs
per day from one to four.
e) The Fulton Warranty does not
cover damage or failure that can be
attributed to corrosion, scale or dirt
accumulations. Oxygen is a cor-
rosive.
See the Warranty Section of
this manual for full details.
Recommended Water Treatment
a)
Following are recommendations
for feed water and boiler water.
Contact your local water treatment
professional for testing and treatment
recommendations. It is very important
that a strict water treatment program
be followed.
Feedwater:
Dissolved Oxygen.............less than 0.05 ppm
pH Value............................9-11 (tested at room
temperature)
*Hardness..........................less than 70 ppm
in the form of CACO
3
Oil.......................................none
Suspended Solids.............none
Organic Matter ..................less than 5.0 ppm
Chloride .............................less than 50.0 ppm
Total Dissolved Solids.......less than 300ppm
Boiler Water:
Phosphate....................30 to 50 ppm
in the form of PO
4
Alkalinity .......................less than 300 ppm in
the form of CACO3
Chloride........................less than 500 ppm
pH Value.......................9 to 11 tested
at room temperature)
Total Dissolved Solids..400 to 2,000 ppm
Iron................................1 ppm maximum
Silica.............................180 ppm max. as SIO
2
Hardness......................less than 50.0 ppm
Dissolved Oxygen........none
ppm = parts per million; CACO3=Calcium
Carbonate; PO4=Phosphate; SiO2=silicon
dioxide; * 1 Grain Hardness = 17.118 ppm
Therefore: 70 ppm = 4.10 grains hardness
b)
It is critical that the boiler pH be
alkaline (9-11) whenever water is in
the boiler. Solids that enter in with the
feed water concentrate in the boiler.
Daily boiler blow down is recommend-
ed to prevent corrosion and/or
deposits from forming.
Glossary of Water
Supply Corrosives
and Inhibitors
Dissolved Oxygen:
Oxygen that is
dissolved in the feedwater will cause
the steel in the boiler and the feedwa-
ter system to be attacked by the water
in a manner described as “pitting”.
The pits that are produced can vary
from tiny depressions to holes large
enough to penetrate the boiler metal
and are usually covered with tuber-
cles of iron oxide. Once pitting starts,
it may be extremely hard to arrest.
Pitting can proceed at a surprisingly
rapid rate and can occur not only in
the boiler proper, but also in pre-boiler
equipment such as economizers,
feedwater heaters, and feedwater
lines.
Sodium Sulfite:
Its purpose is to
chemically remove the dissolved oxy-
gen left in the feedwater.
Sodium Sulfite reacts chemically
with dissolved oxygen, producing
sodium sulfate. Since it is desirable to
remove dissolved oxygen from the
feedwater before it reaches a boiler.
Sodium sulfite is best introduced con-
tinuously at some suitable point in the
feedwater system. Chemical residual
control is based on the maintenance
of a specific excess of sodium sulfite
in the boiler water. The essential
requirement being to maintain in the
feedwater at all times slightly more
than enough sodium sulfite to con-
sume all of the dissolved oxygen.
When sodium sulfite is not fed contin-
uously, protection of the boiler against
oxygen attack must depend on the
reserve of sodium sulfite that is pre-
sent in the boiler water. In this case, it
is important that the feedwater and
the boiler water are mixed thoroughly
and as quickly as possible so that
boiler water sodium sulfite may con-
sume feedwater oxygen before the
latter can cause damage to the boiler.
Sulfite as a treatment represents
a second line of defense against oxy-
gen corrosion. A vigorous mainte-
nance program to safe guard against
oxygen leakage into the pre-boiler
system should be followed.
Suspended Solids:
Suspended
solids are the undissolved matter in
water, including dirt, silt vegetation,
and any other insoluble organic mat-
ter. Normally suspended solids are
expressed in terms of turbidity.The
presence of suspended solids in cool-
ing water can increase impingement
type corrosion. Suspended solids may
also deposit in low velocity areas and
create differential aeration cells.
Pitting can result. The most common
cause of high suspended solids is
high hardness feedwater. Of the
agents which cause foaming, sus-
pended solids probably have the least
effect. Reasons for the increased
hardness or other suspended solids
should be determined.
In line filters, or various types of
pretreatment can be used to lower
the suspended solids level. Various
polymers assist in holding solids in
suspension.
Alkalinity:
Alkalinity is the capacity of
a water to neutralize acids.
Common water alkalinities consist of
bicarbonate, carbonates, hydroxide,
phosphate, and silicate. These alka-
linities, especially bicarbonates and
carbonates, break down to form car-
bon dioxide in steam, which is a major
factor in the corrosion on condensate
lines. High alkalinity also causes
foaming and carry over in boilers.
Both foaming and carry over cause
erratic boiler operation. When foaming
occurs an anti-foam should be added
or increased. The reason for the high
alkalinity should be determined. It
may result from lack of sufficient blow
off. Pretreated makeup water and
condensate should also be checked.
Quite often the source of alkalinity is
an overdose of alkaline internal water
treatment chemical.
Description/Instructions
37-G 1/01
Summary of Contents for FB-A 10
Page 2: ......
Page 4: ......
Page 6: ......
Page 8: ...2 G 1 01...
Page 9: ...Safety Warnings Precautions 1 3 G 1 01...
Page 10: ...4 G 1 01...
Page 12: ...6 G 1 01...
Page 13: ...7 G 1 01 Description Instructions LE...
Page 14: ...8 G 1 01...
Page 17: ...11 G 1 01 Operation LE...
Page 18: ...12 G 1 01...
Page 20: ...14 G 1 01...
Page 21: ...15 G 1 01 Maintenance LE...
Page 22: ...16 G 1 01...
Page 29: ...23 G 1 01 Parts LE...
Page 30: ...24 G 1 01...
Page 32: ...26 G 1 01...
Page 33: ...Boiler Description Instructions Gas Fired Boiler 2 27 G 1 01...
Page 37: ...30 G 1 01 Description Instructions I E K K J K D C H B A G F...
Page 50: ...42b G 1 01...
Page 51: ...43D G 1 01 Operation 3...
Page 52: ...43b G 1 01...
Page 59: ...Maintenance 4 5 G 1 01...
Page 60: ...51 G 1 01...
Page 73: ...Parts 5 6 G 1 01...
Page 88: ...79 G 1 01 Parts...
Page 90: ...81 G 1 01 Parts Gas Burner Ignition Assembly Gas Burner Components...
Page 95: ...Warranty 6 8 G 1 01...
Page 96: ...87 G 1 01...
Page 98: ...89 G 1 01...
Page 100: ...91 G 1 01...
Page 101: ...Component Data Sheets 7 G 1 01...
Page 102: ......