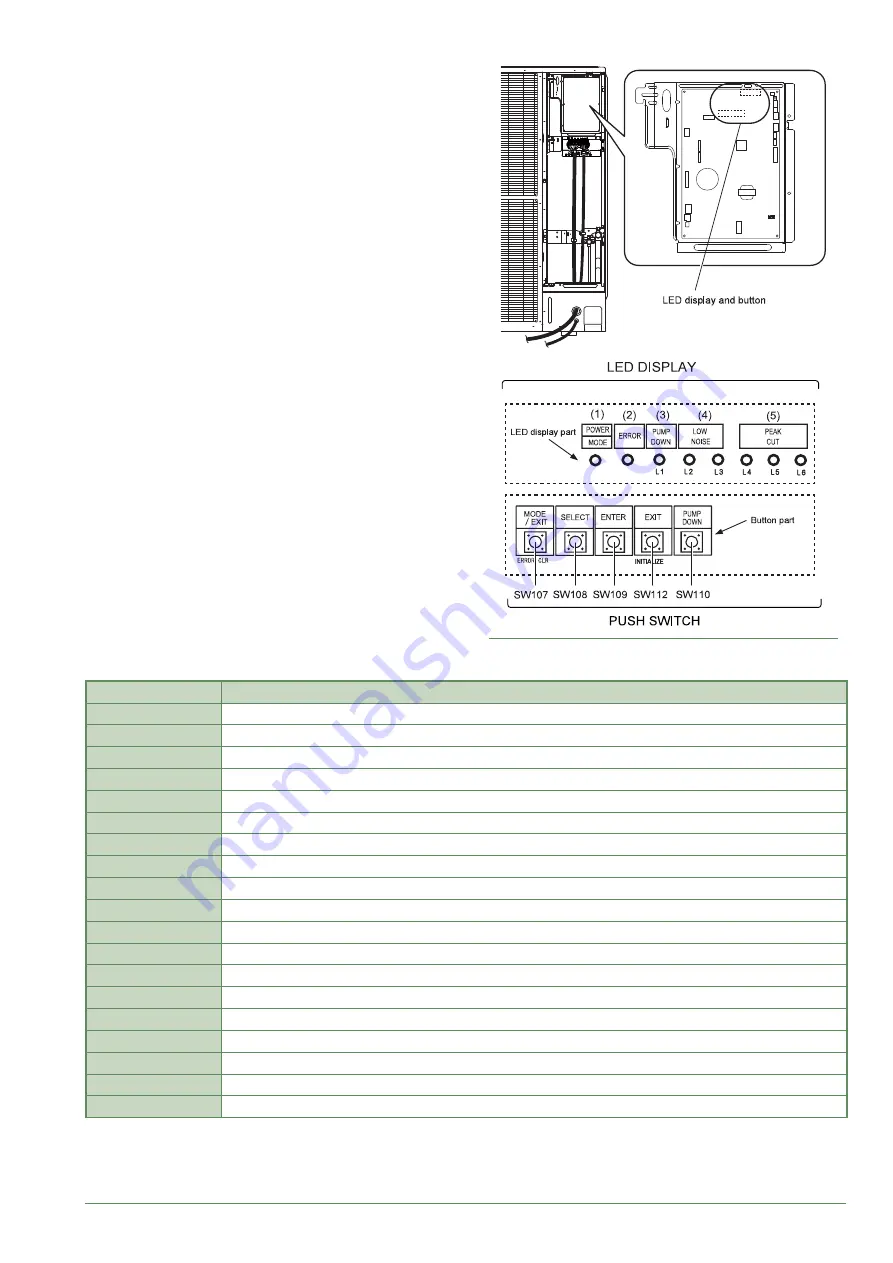
- 77 -
Waterstage / Installation / 2011 - EN
►
Faults displayed on the 3-phase
outdoor unit
To access the electronic board, you must remove the
front (right-hand) facing from the outdoor unit.
Faults are coded by LED flashes.
When an error occurs:
The LED "
ERROR
" (2) blinks.
Press once on the switch "
ENTER
" (SW109).
The "
ERROR
" (2) LED blinks several times depending
on the error's type (see below).
LED display
Error contents
1 Flash
Serial forward transfer error.
2 Flashes
Discharge thermistor error.
3 Flashes
Pressure switch error.
4 Flashes
Heat-exchange thermistor (outlet) error.
6 Flashes
Expansion valve thermistor error.
7 Flashes
Outdoor temperature thermistor error.
8 Flashes
Compressor thermistor error.
9 Flashes
Transistor PCB error.
11 Flashes
Discharge temperature error (permanent stoppage).
12 Flashes
Compressor temperature error (permanent stoppage).
13 Flashes
Over current error (permanent stoppage).
14 Flashes
Detection of compressor position error (permanent stoppage).
15 Flashes
Compressor start up error (permanent stoppage).
16 Flashes
Fan motor 1 error (permanent stoppage).
17 Flashes
Fan motor 2 error (permanent stoppage).
18 Flashes
Inverter error.
20 Flashes
Low pressure abnormal.
23 Flashes
Discharge pressure sensor error.
24 Flashes
Suction pressure sensor error.
fig. 46 - Location of switches and LED on 3-phase
outdoor unit
Summary of Contents for Waterstage WOYK150LJL
Page 17: ... ...
Page 37: ... ...
Page 39: ... 39 fig 33 Cable passages Power cables Sensor cables Waterstage Installation 2011 EN ...
Page 67: ... ...