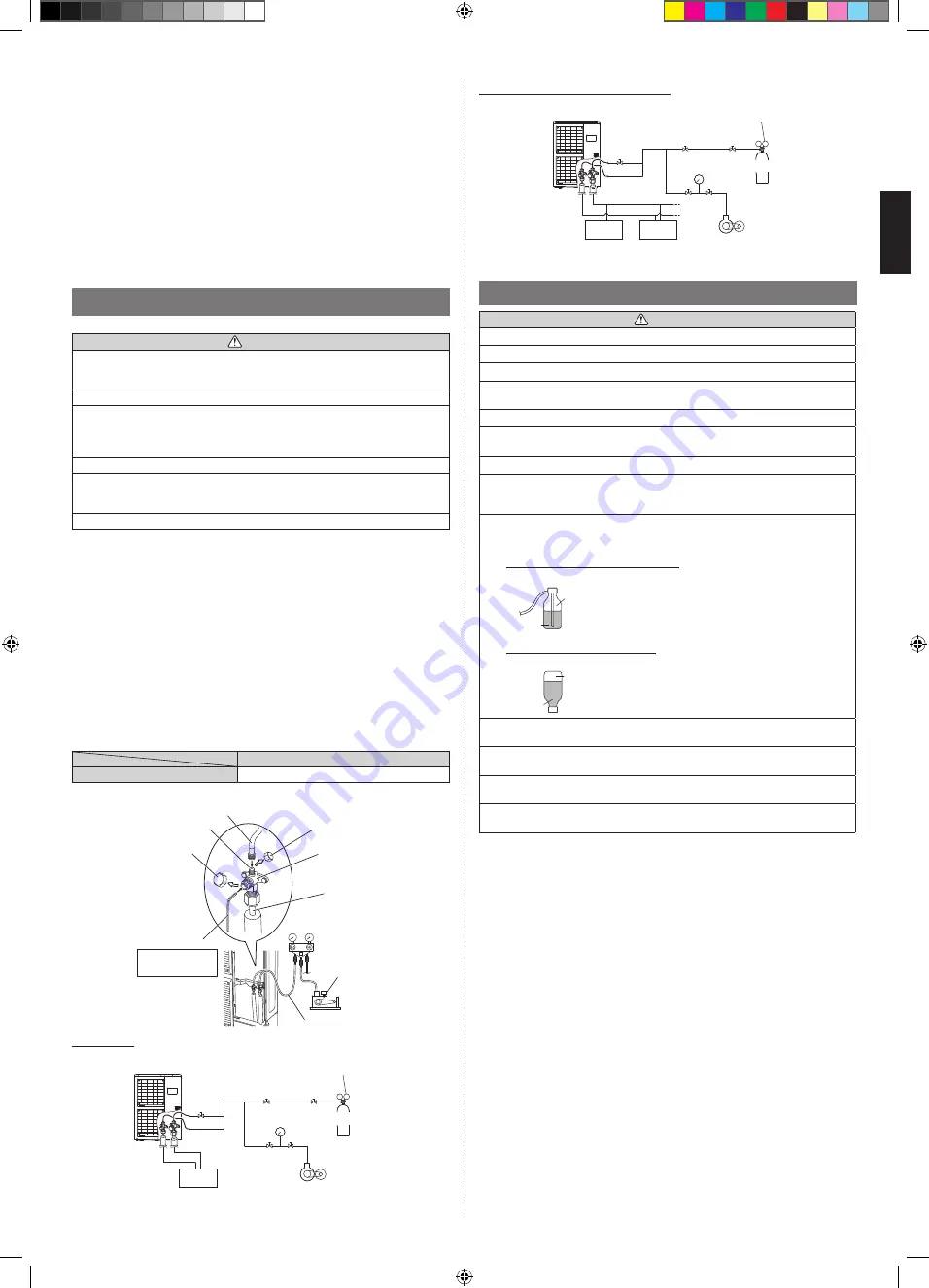
En-8
Simultaneous operation multi type
Outdoor unit
Indoor unit
Vacuum pump
Pressure gauge
Pressure regulating valve
Nitrogen
5.6. Additional charging
CAUTION
Do not turn on the power unless all operations are complete.
After evacuating the system, add refrigerant.
Do not charge the system with a refrigerant other than R410A.
Always keep to the limit on the total amount of refrigerant. Exceeding the limit on the
total amount of refrigerant will lead to malfunction during charging of refrigerant.
Do not reuse recovered refrigerant.
Use an electronic scale to measure the charging amount of refrigerant.
Adding more refrigerant than the speci
fi
ed amount will cause a malfunction.
Add refrigerant by charging the system with the refrigerant in the liquid state.
When charging the refrigerant, take into account the slight change in the composition
of the gas and liquid phases, and always charge from the liquid phase side whose com-
position is stable. Adding refrigerant through the gas pipe will cause a malfunction.
Check if the steel cylinder has a siphon installed or not before
fi
lling. (There is an indi-
cation “with siphon for
fi
lling liquid” on the steel cylinder.)
Filling method for cylinder with siphon
Set the cylinder vertical and
fi
ll with the liquid.
(Liquid can be
fi
lled without turning bottom up with the
siphon inside.)
Liquid
Gas
R410A
Filling method for other cylinders
Turn bottom up and
fi
ll with liquid.
(Be careful to avoid turning over the cylinder.)
Liquid
Gas
R410A
Be sure to use the special tools for R410A for pressure resistance and to avoid mixing
of impure substances.
If the units are further apart than the maximum pipe length, correct operation cannot be
guaranteed.
Make sure to back closing valve after refrigerant charging. Otherwise, the compressor
may fail.
Minimize refrigerant release to the air. Excessive release is prohibited under the Freon
Collection and Destruction Law.
5.6.1. If additional refrigerant is required
• When the piping is longer than chargeless piping length, additional charging is neces-
sary.
1) Remove the charging cap from the liquid pipe.
2) Attach a charging hose to the refrigerant cylinder, and connect it to the charging
port.
3) Add refrigerant by calculating the additional refrigerant volume in accordance with
the table below.
4) Remove the charging hose and install the charging cap.
5) Remove the body caps (gas pipe, and liquid pipe), and open the valves.
6) Close the body caps.
* Tighten the body caps and charging caps to the torque values speci
fi
ed in the Table A.
To open and close the valves,
Use an M5 hexagon wrench for liquid pipes.
Use an M10 hexagon wrench for gas pipes.
• After connecting the pipes, perform a sealing test.
• Make sure that the 3-way valves are closed before performing a sealing test.
• Pressurize nitrogen gas to 4.15 MPa to perform the sealing test.
• Add nitrogen gas to both the liquid pipes and the gas pipes.
• Check all
fl
are connections and welds. Then, check that the pressure has not
decreased.
• Compare the pressures after pressurizing and letting it stand for 24 hours, and check
that the pressure has not decreased.
* When the outdoor air temperature changes 5 °C, the test pressure changes
0.05 MPa. If the pressure has dropped, the pipe joints may be leaking.
• If a leak is found, immediately repair it and perform the sealing test again.
• After completing the sealing test, release the nitrogen gas from both valves.
• Release the nitrogen gas slowly.
5.5. Vacuum process
CAUTION
Perform a refrigerant leakage test (air tightness test) to check for leaks using nitrogen
gas while all valves in the outdoor unit are closed. (Use the test pressure indicated on
the nameplate.)
Be sure to evacuate the refrigerant system using a vacuum pump.
The refrigerant pressure may sometimes not rise when a closed valve is opened after
the system is evacuated using a vacuum pump. This is caused by the closure of the
refrigerant system of the outdoor unit by the electronic expansion valve. This will not
affect the operation of the unit.
If the system is not evacuated suf
fi
ciently, its performance will drop.
Use a clean gauge manifold and charging hose that were designed speci
fi
cally for use
with R410A. Using the same vacuum equipment for different refrigerants may damage
the vacuum pump or the unit.
Do not purge the air with refrigerants, but use a vacuum pump to evacuate the system.
(1) Check that the valves are closed by removing the blank caps from the gas and
liquid pipes.
(2) Remove the charging port cap, and connect the gauge manifold and the vacuum
pump to the charging valve with the service hoses.
(3) Vacuum the indoor unit and the connecting pipes until the pressure gauge
indicates –0.1 MPa (–76 cmHg).
(4) When –0.1 MPa (–76 cmHg) is reached, operate the vacuum pump for at least
60 minutes.
(5) Disconnect the service hoses and
fi
t the charging port cap to the charging valve to
the speci
fi
ed torque. (Refer to below table)
(6) Remove the blank caps, and fully open the 3-way valves with a hexagon wrench
[Torque: 6 to 7 N·m (60 to 70 kgf·cm)].
(7) Tighten the blank caps of the 3-way valve to the speci
fi
ed torque. (Refer to Table A
on page 7.)
Tightening torque [N·m (kgf·cm)]
Charging port cap
10 to 12 (100 to 120)
Service hose
Service hose with valve core
Charging port
Blank cap
Hexagon wrench
Connecting pipe
Gauge manifold
Vacuum pump
Charging port cap
3-way valve
Use a 4 mm
hexagon wrench
Single type
Pressure regulating valve
Pressure gauge Nitrogen
Indoor unit
Outdoor unit
Vacuum pump
9380545231_IM.indb 8
9380545231_IM.indb 8
7/14/2017 8:53:12 AM
7/14/2017 8:53:12 AM