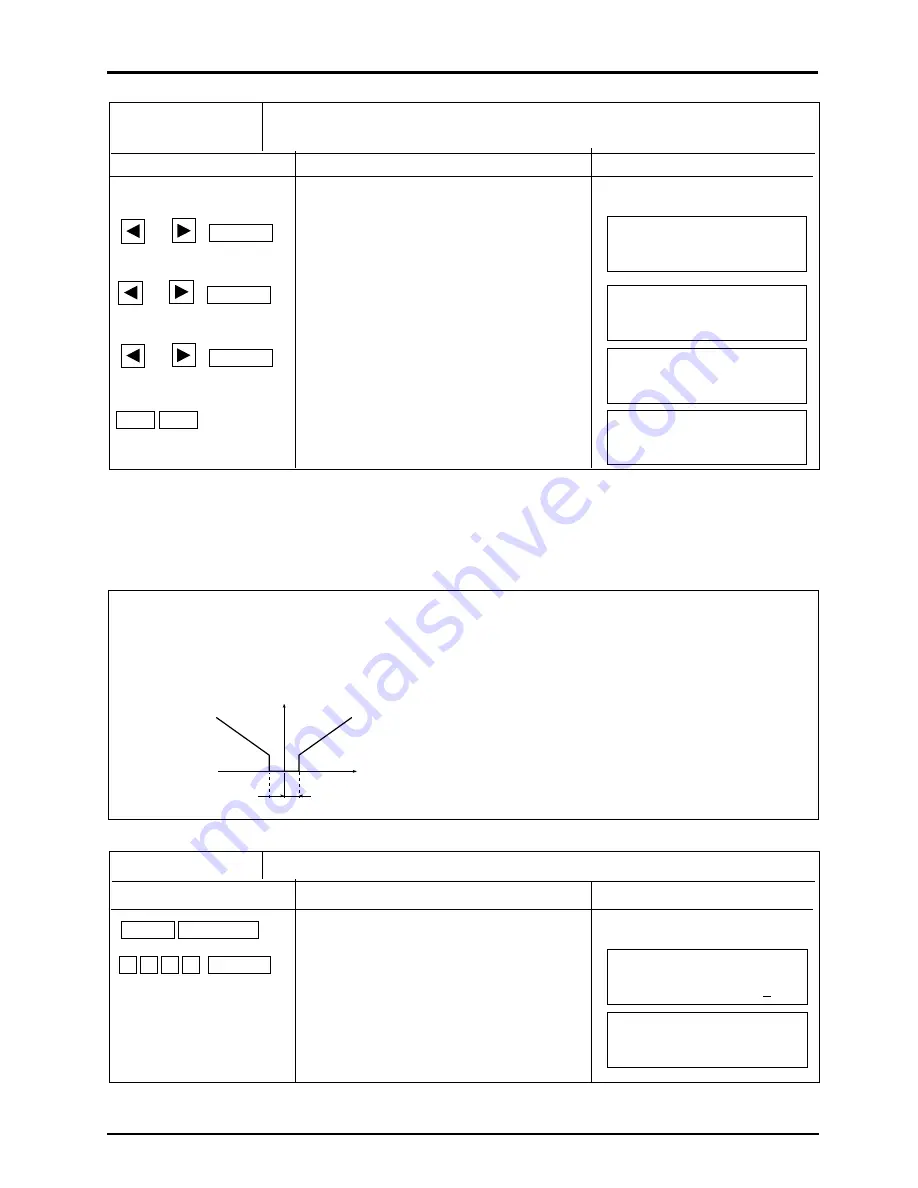
21
5.4 (8) Low flow output cut
Description
A low flow output can be cut.
This flowmeter will display the flow rate, when the fluid in the piping is moving with the
valve closed due to a convection current. The cutting point should be set as needed.
(Setting range : 0 to 16.4 ft./s in terms of flow velocity value)
Operation (example) Setting of cutting point to 0.05m/s.
Key operation
FUNC CUT OFF
0 . 0 5 , ENTER
Description
Enter “0.05” with ten keys.
CUT OFF
(Measurement display)
Display
Flow rate
Cutting set value
Outlet
0.05 m/s
Operation (example) Display instantaneous flow velocity and instantaneous flow unit in m3/h, and
instantanous flow rate in 3 digits after decimal point.
Key operation
FUNC DISP
or
, ENTER
or
, ENTER
or
, ENTER
ESC ESC
Description
Select “Flow velocity”.
Select :m
3
/h”.
Select “00000.000”.
1: DISPLAY KIND
VELOCITY
(Measurement display)
Display
2: FLOW UNIT
m3/h
2: DECIMAL POINT
00000.000
m3/h