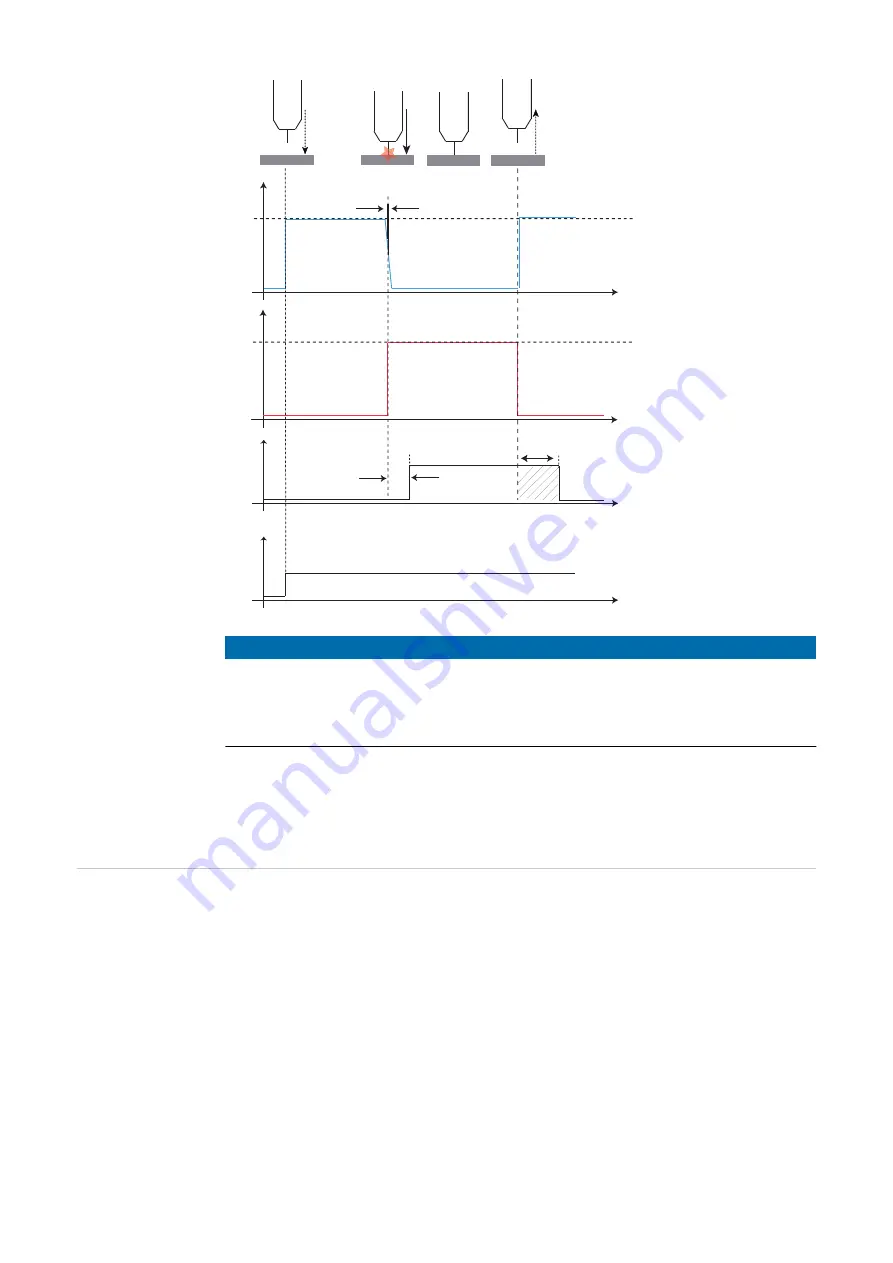
t
t
t
U
plus. 300ms * or as long as the wire touches the work piece
I
< 15ms *
t
* timing depends Interface
delta u (rising voltage) --> delta t (time)
Condition: voltage drop i.e. 1,5 volt (adjustable)
max. Open circuit voltage
depends on PowerSource type (i.e. 60V)
max. current aprox. 3A
digital I/O
digital I/O
Touch
voltage
Touchcurr
en
t
Output signal
Input signal
NOTE!
Risk of signal overlap.
This can lead to problems in connection with the Wirebrake option.
▶
After deactivating the Touch sensing signal, wait 4 seconds before setting another
signal.
Additional information for TWIN systems:
-
Touch sensing is always carried out using one wire electrode
-
In single wire mode, the wire electrode of the active process line is used
-
In TWIN mode, the wire electrode of the leading process line (Lead) is used
Gas nozzle touch
sensing (Gas
nozzle position
search) - Single
Bit
If the position detection is carried out by touching the workpiece with the gas nozzle
(instead of the wire electrode), the gas nozzle must be connected to the welding current
lead using an RC circuit.
The use of an RC circuit is required so that if the gas nozzle comes into contact with the
workpiece during welding:
-
Unacceptable currents in the connection between the gas nozzle and the welding
current lead are avoided
-
The welding process is not influenced
When contact is detected by the gas nozzle, the short circuit current only flows for
approx. 4 ms, until the capacitors in the RC circuit are charged. To ensure safe contact
detection by the robot controller, the Arc stable and Touch sensing signals are on for 0.3
s longer than the short circuit current.
12