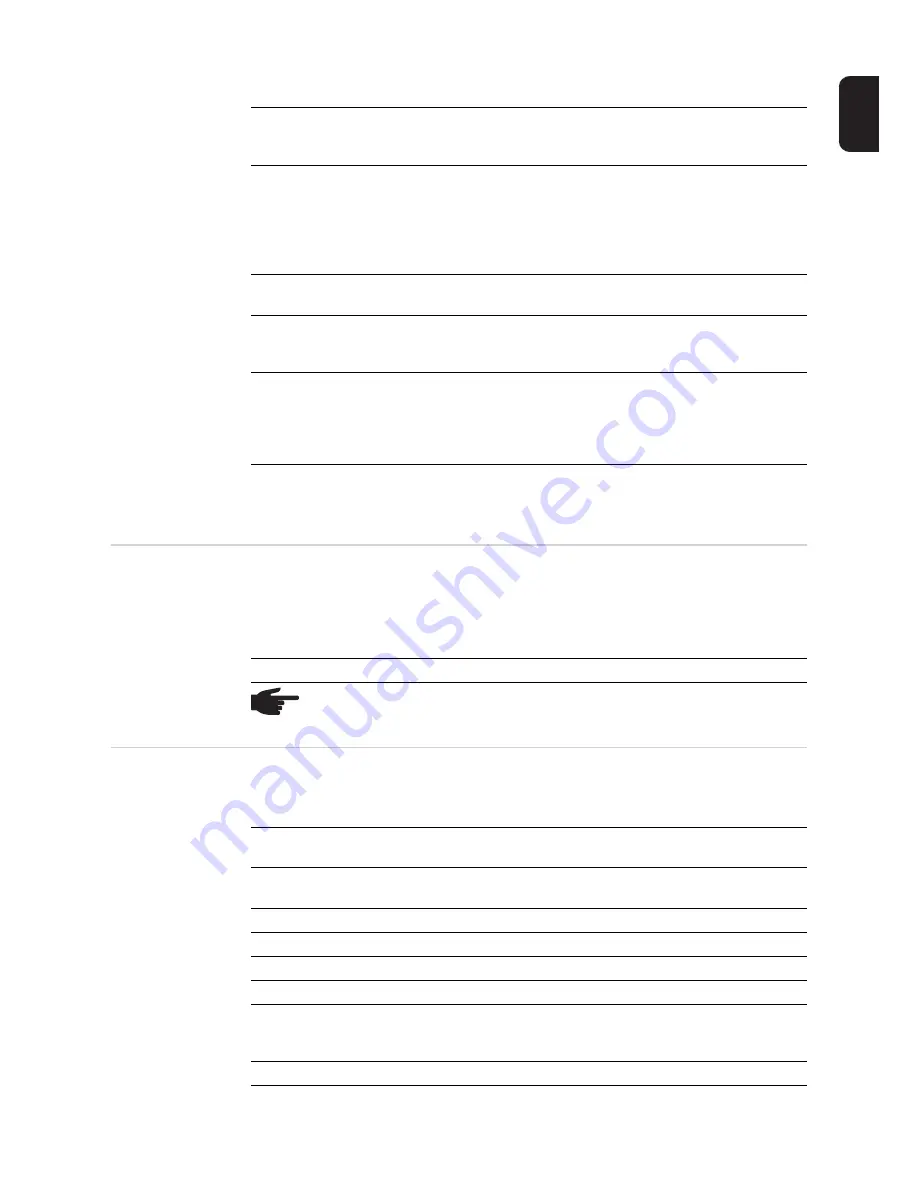
15
EN
Risk of scalding from escaping coolant. Switch off cooling unit before disconnecting cool-
ant flow or return lines.
Observe the information on the coolant safety data sheet when handling coolant. The cool-
ant safety data sheet may be obtained from your service centre or downloaded from the
manufacturer's website.
Use only suitable load-carrying equipment supplied by the manufacturer when transporting
devices by crane.
-
Hook chains and/or ropes onto all suspension points provided on the load-carrying
equipment.
-
Chains and ropes must be at the smallest angle possible to the vertical.
-
Remove gas cylinder and wire-feed unit (MIG/MAG and TIG devices).
If the wire-feed unit is attached to a crane holder during welding, always use a suitable,
insulated wirefeeder hoisting attachment (MIG/MAG and TIG devices).
If the device has a carrying strap or handle, this is intended solely for carrying by hand. The
carrying strap is not to be used if transporting with a crane, counterbalanced lift truck or
other mechanical hoist.
All lifting accessories (straps, handles, chains, etc.) used in connection with the device or
its components must be tested regularly (e.g. for mechanical damage, corrosion or chang-
es caused by other environmental factors).
The testing interval and scope of testing must comply with applicable national standards
and directives as a minimum.
Odourless and colourless shielding gas may escape unnoticed if an adapter is used for the
shielding gas connection. Prior to assembly, seal the device-side thread of the adapter for
the shielding gas connection using suitable Teflon tape.
Factors affecting
welding results
The following requirements with regard to shielding gas quality must be met if the welding
system is to operate in a correct and safe manner:
-
Size of solid matter particles < 40 μm
-
Pressure dew point < -20 °C
-
Max. oil content < 25 mg/m³
Filters must be used if necessary.
NOTE!
There is an increased risk of soiling if ring mains are being used
Danger from
shielding gas cyl-
inders
Shielding gas cylinders contain gas under pressure and can explode if damaged. As the
shielding gas cylinders are part of the welding equipment, they must be handled with the
greatest of care.
Protect shielding gas cylinders containing compressed gas from excessive heat, mechan-
ical impact, slag, naked flames, sparks and arcs.
Mount the shielding gas cylinders vertically and secure according to instructions to prevent
them falling over.
Keep the shielding gas cylinders well away from any welding or other electrical circuits.
Never hang a welding torch on a shielding gas cylinder.
Never touch a shielding gas cylinder with an electrode.
Risk of explosion - never attempt to weld a pressurised shielding gas cylinder.
Only use shielding gas cylinders suitable for the application in hand, along with the correct
and appropriate accessories (regulator, hoses and fittings). Only use shielding gas cylin-
ders and accessories that are in good condition.
Turn your face to one side when opening the valve of a shielding gas cylinder.
Summary of Contents for TPS/i Robotics Pull
Page 2: ...2...
Page 4: ...4...
Page 19: ...General information...
Page 20: ......
Page 41: ...Controls connections and mechani cal components...
Page 42: ......
Page 57: ...Installation conventional robot...
Page 58: ......
Page 60: ...60...
Page 70: ...70 3 3 Steel inner liner 1 1 1 1 2 3...
Page 73: ...73 EN 1 2...
Page 75: ...75 EN 2 Fitting the inner liner unreeling wirefeeder Split Box SB 500i R 1 2 3 4 2 1 2 3 4...
Page 76: ...76 Fitting the inner liner SplitBox WF 25i with inter nal inner liner 1 2 3 4 1 2 3 4...
Page 78: ...78 3 Fitting the inner liner unreeling wirefeeder wire buffer 1 2 3 4 3 1 2 3 4...
Page 79: ...79 EN 5 Fitting the inner liner unreeling wirefeeder Split Box SB60i 1 2 3 4 5 1 2 3 4...
Page 84: ...84...
Page 85: ...Installation PAP...
Page 86: ......
Page 88: ...88 Fitting the SplitBox Fitting the SB 500i R PAP 1 2 1 2...
Page 91: ...91 EN 5 6 Installing the CrashBox i Dum my on the robot 1 2 3 6 7 1 2 3...
Page 95: ...95 EN 3 3 Steel inner liner 1 1 1 1 2 3...
Page 98: ...98 1 2...
Page 101: ...101 EN 2 3 4 Fitting the inner liner unreeling wirefeeder wire buffer 1 2 2 3 4 1 2...
Page 104: ...104...
Page 105: ...Start up...
Page 106: ......
Page 109: ...109 EN Inserting replac ing the WF 25i Ro bacta Drive feed rollers 1 2 3 4 5 6 1 2 3 4 5 6...
Page 110: ...110 7 8 9 10 11 12 7 8 9 10 11 12...
Page 111: ...111 EN Inserting replac ing the WF 60i Ro bacta Drive CMT feed rollers 1 2 3 4 5 6 1 2 3 4 5 6...
Page 112: ...112 7 8 9 10 11 12 7 8 9 10 11 12...
Page 117: ...Troubleshooting maintenance and disposal...
Page 118: ......
Page 126: ...126 Replacing the WF Robacta Drive gas saver nozzle 1 2 3 4 5 6 1 2 3 4 5 6...
Page 127: ...127 EN 7 Replacing the SB 60i R inner liner Removing the inner liner 1 2 3 4 7 1 2 3 4...
Page 128: ...128 Inserting the inner liner 1 2 3 4 1 2 3 4...
Page 133: ...133 EN Removing the CrashBox PAP from the robot 1 2 3 4 5 6 1 2 3 4 5 6...
Page 135: ...Technical data...
Page 136: ......
Page 146: ......
Page 147: ......