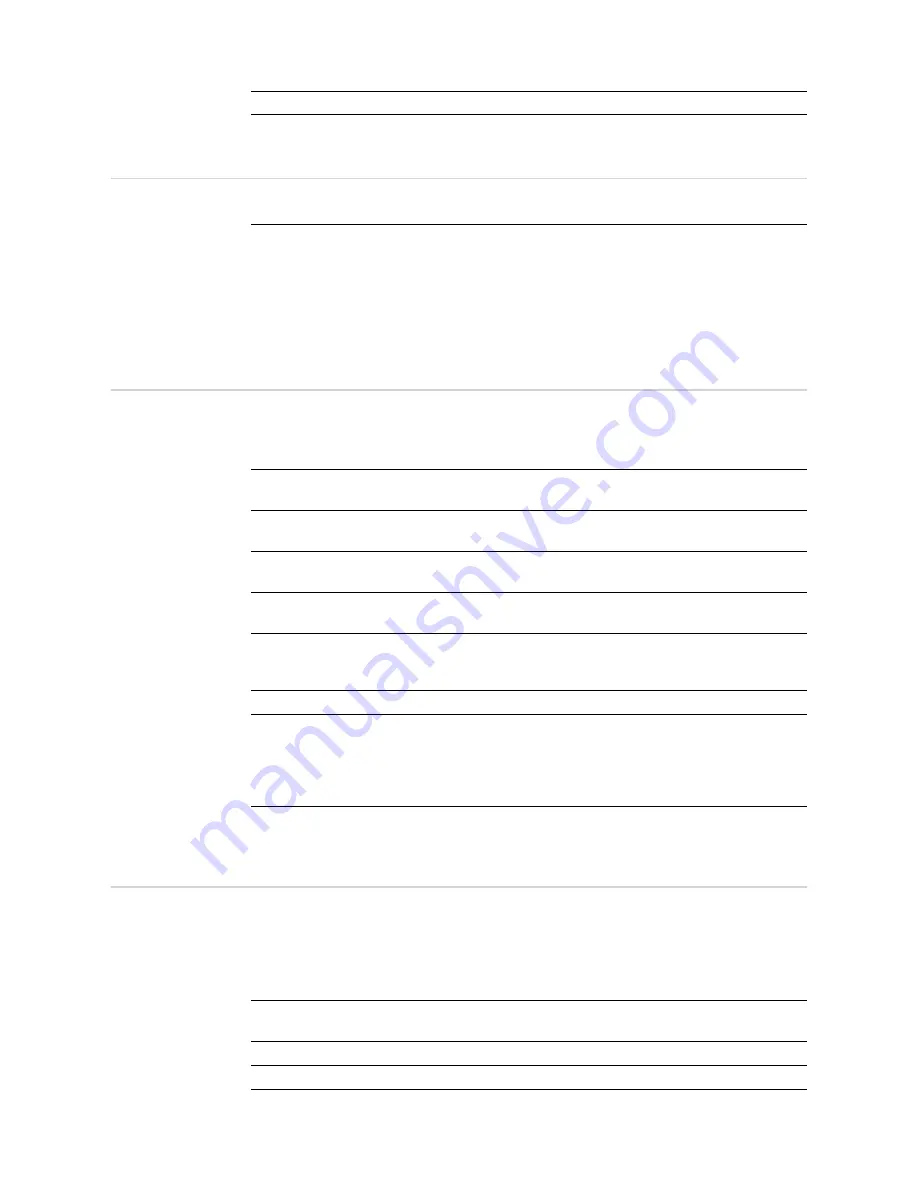
16
Close the shielding gas cylinder valve if no welding is taking place.
If the shielding gas cylinder is not connected, leave the valve cap in place on the cylinder.
The manufacturer's instructions must be observed as well as applicable national and inter-
national regulations for shielding gas cylinders and accessories.
Danger from es-
caping shielding
gas
Risk of suffocation from the uncontrolled escape of shielding gas
Shielding gas is colourless and odourless and, in the event of a leak, can displace the ox-
ygen in the ambient air.
-
Ensure an adequate supply of fresh air with a ventilation rate of at least 20 m³/hour.
-
Observe safety and maintenance instructions on the shielding gas cylinder or the main
gas supply.
-
Close the shielding gas cylinder valve or main gas supply if no welding is taking place.
-
Check the shielding gas cylinder or main gas supply for uncontrolled gas leakage be-
fore every start-up.
Safety measures
at the installation
location and dur-
ing transport
A device toppling over could easily kill someone. Place the device on a solid, level surface
such that it remains stable
-
The maximum permissible tilt angle is 10°.
Special regulations apply in rooms at risk of fire or explosion
-
Observe relevant national and international regulations.
Use internal directives and checks to ensure that the workplace environment is always
clean and clearly laid out.
Only set up and operate the device in accordance with the degree of protection shown on
the rating plate.
When setting up the device, ensure there is an all-round clearance of 0.5 m (1 ft. 7.69 in.)
to ensure that cooling air can flow in and out freely.
When transporting the device, observe the relevant national and local guidelines and ac-
cident prevention regulations. This applies especially to guidelines regarding the risks aris-
ing during transport.
Do not lift or transport operational devices. Switch off devices before transport or lifting.
Before transporting the device, allow coolant to drain completely and detach the following
components:
-
Wirefeeder
-
Wirespool
-
Shielding gas cylinder
After transporting the device, the device must be visually inspected for damage before
commissioning. Any damage must be repaired by trained service technicians before com-
missioning the device.
Safety measures
in normal opera-
tion
Only operate the device when all safety devices are fully functional. If the safety devices
are not fully functional, there is a risk of
-
injury or death to the operator or a third party
-
damage to the device and other material assets belonging to the operator
-
inefficient operation of the device
Any safety devices that are not functioning properly must be repaired before switching on
the device.
Never bypass or disable safety devices.
Before switching on the device, ensure that no one is likely to be endangered.
Summary of Contents for TPS/i Robotics Pull
Page 2: ...2...
Page 4: ...4...
Page 19: ...General information...
Page 20: ......
Page 41: ...Controls connections and mechani cal components...
Page 42: ......
Page 57: ...Installation conventional robot...
Page 58: ......
Page 60: ...60...
Page 70: ...70 3 3 Steel inner liner 1 1 1 1 2 3...
Page 73: ...73 EN 1 2...
Page 75: ...75 EN 2 Fitting the inner liner unreeling wirefeeder Split Box SB 500i R 1 2 3 4 2 1 2 3 4...
Page 76: ...76 Fitting the inner liner SplitBox WF 25i with inter nal inner liner 1 2 3 4 1 2 3 4...
Page 78: ...78 3 Fitting the inner liner unreeling wirefeeder wire buffer 1 2 3 4 3 1 2 3 4...
Page 79: ...79 EN 5 Fitting the inner liner unreeling wirefeeder Split Box SB60i 1 2 3 4 5 1 2 3 4...
Page 84: ...84...
Page 85: ...Installation PAP...
Page 86: ......
Page 88: ...88 Fitting the SplitBox Fitting the SB 500i R PAP 1 2 1 2...
Page 91: ...91 EN 5 6 Installing the CrashBox i Dum my on the robot 1 2 3 6 7 1 2 3...
Page 95: ...95 EN 3 3 Steel inner liner 1 1 1 1 2 3...
Page 98: ...98 1 2...
Page 101: ...101 EN 2 3 4 Fitting the inner liner unreeling wirefeeder wire buffer 1 2 2 3 4 1 2...
Page 104: ...104...
Page 105: ...Start up...
Page 106: ......
Page 109: ...109 EN Inserting replac ing the WF 25i Ro bacta Drive feed rollers 1 2 3 4 5 6 1 2 3 4 5 6...
Page 110: ...110 7 8 9 10 11 12 7 8 9 10 11 12...
Page 111: ...111 EN Inserting replac ing the WF 60i Ro bacta Drive CMT feed rollers 1 2 3 4 5 6 1 2 3 4 5 6...
Page 112: ...112 7 8 9 10 11 12 7 8 9 10 11 12...
Page 117: ...Troubleshooting maintenance and disposal...
Page 118: ......
Page 126: ...126 Replacing the WF Robacta Drive gas saver nozzle 1 2 3 4 5 6 1 2 3 4 5 6...
Page 127: ...127 EN 7 Replacing the SB 60i R inner liner Removing the inner liner 1 2 3 4 7 1 2 3 4...
Page 128: ...128 Inserting the inner liner 1 2 3 4 1 2 3 4...
Page 133: ...133 EN Removing the CrashBox PAP from the robot 1 2 3 4 5 6 1 2 3 4 5 6...
Page 135: ...Technical data...
Page 136: ......
Page 146: ......
Page 147: ......