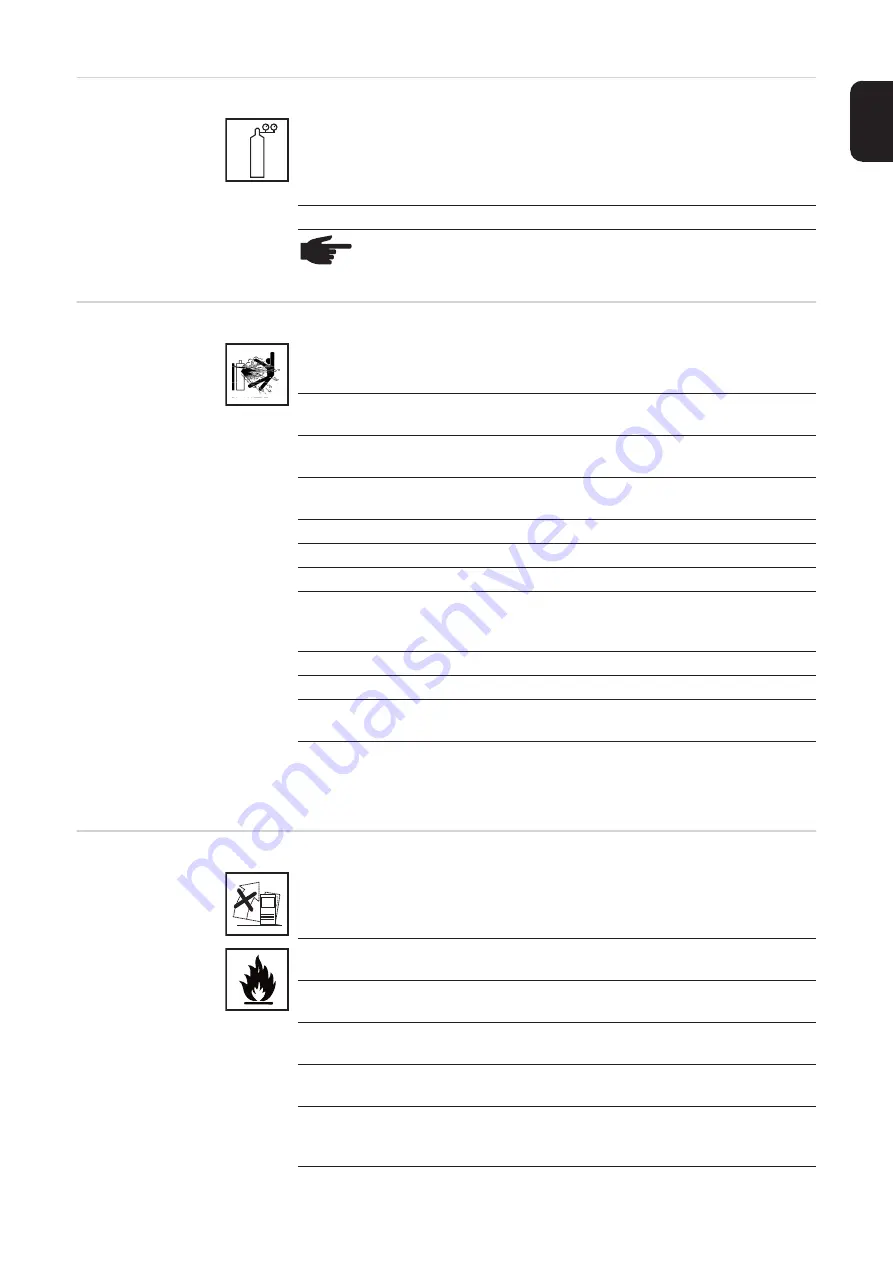
19
EN
Factors affecting
welding results
Danger from
shielding gas cyl-
inders
Safety measures
at the installation
location and dur-
ing transport
The following requirements with regard to shielding gas quality must be met if
the welding system is to operate in a correct and safe manner:
-
Size of solid matter particles < 40
μ
m
-
Pressure dew point < -20 °C
-
Max. oil content < 25 mg/m³
Filters must be used if necessary.
NOTE!
There is an increased risk of soiling if ring mains are being
used
Shielding gas cylinders contain gas under pressure and can explode if dam-
aged. As the shielding gas cylinders are part of the welding equipment, they
must be handled with the greatest of care.
Protect shielding gas cylinders containing compressed gas from excessive
heat, mechanical impact, slag, naked flames, sparks and arcs.
Mount the shielding gas cylinders vertically and secure according to instruc-
tions to prevent them falling over.
Keep the shielding gas cylinders well away from any welding or other electrical
circuits.
Never hang a welding torch on a shielding gas cylinder.
Never touch a shielding gas cylinder with an electrode.
Risk of explosion - never attempt to weld a pressurised shielding gas cylinder.
Only use shielding gas cylinders suitable for the application in hand, along with
the correct and appropriate accessories (regulator, hoses and fittings). Only
use shielding gas cylinders and accessories that are in good condition.
Turn your face to one side when opening the valve of a shielding gas cylinder.
Close the shielding gas cylinder valve if no welding is taking place.
If the shielding gas cylinder is not connected, leave the valve cap in place on
the cylinder.
The manufacturer's instructions must be observed as well as applicable na-
tional and international regulations for shielding gas cylinders and accesso-
ries.
A device toppling over could easily kill someone. Place the device on a solid,
level surface such that it remains stable
-
The maximum permissible tilt angle is 10°.
Special regulations apply in rooms at risk of fire or explosion
-
Observe relevant national and international regulations.
Use internal directives and checks to ensure that the workplace environment
is always clean and clearly laid out.
Only set up and operate the device in accordance with the degree of protec-
tion shown on the rating plate.
When setting up the device, ensure there is an all-round clearance of 0.5 m (1
ft. 7.69 in.) to ensure that cooling air can flow in and escape unhindered.
When transporting the device, observe the relevant national and local guide-
lines and accident prevention regulations. This applies especially to guidelines
regarding the risks arising during transport.
Summary of Contents for MagicWave 2200 Comfort
Page 2: ...2...
Page 4: ...4...
Page 10: ...10...
Page 23: ...General information...
Page 24: ......
Page 27: ...Control elements and connections...
Page 28: ......
Page 39: ...Installation and commissioning...
Page 40: ......
Page 45: ...Welding...
Page 46: ......
Page 89: ...Setup settings...
Page 90: ......
Page 170: ...170...
Page 171: ...Troubleshooting and maintenance...
Page 172: ......
Page 183: ...183 EN Disposal Dispose of in accordance with the applicable national and local regulations...
Page 184: ...184...
Page 185: ...Appendix...
Page 186: ......
Page 195: ...Spare parts and circuit diagrams...
Page 196: ...196 Spare parts list TransTig MagicWave 2200 Comfort...
Page 197: ...197...
Page 198: ...198 Spare parts list TransTig MagicWave 2500 3000...
Page 200: ...200 Spare parts list TransTig 4000...
Page 201: ...201...
Page 202: ...202 Spare parts list MagicWave 4000...
Page 203: ...203...
Page 204: ...204...
Page 205: ...205 Circuit diagrams MagicWave 2200 Comfort V 12 06 2014...
Page 206: ...206 Circuit diagrams MagicWave 2500 Comfort...
Page 207: ...207 Circuit diagrams MagicWave 3000 Comfort...
Page 208: ...208 Circuit diagrams MagicWave 4000 Comfort V 17 12 2012 1 2...
Page 209: ...209 V 17 12 2012 2 2...
Page 210: ...210 Circuit diagrams TransTig 2200 Comfort V 14 12 2010...
Page 211: ...211 Circuit diagrams TransTig 2500 Comfort...
Page 212: ...212 Circuit diagrams TransTig 3000 Comfort...
Page 213: ...213 Circuit diagrams TransTig 4000 Comfort V 17 12 2012...
Page 214: ......
Page 215: ......