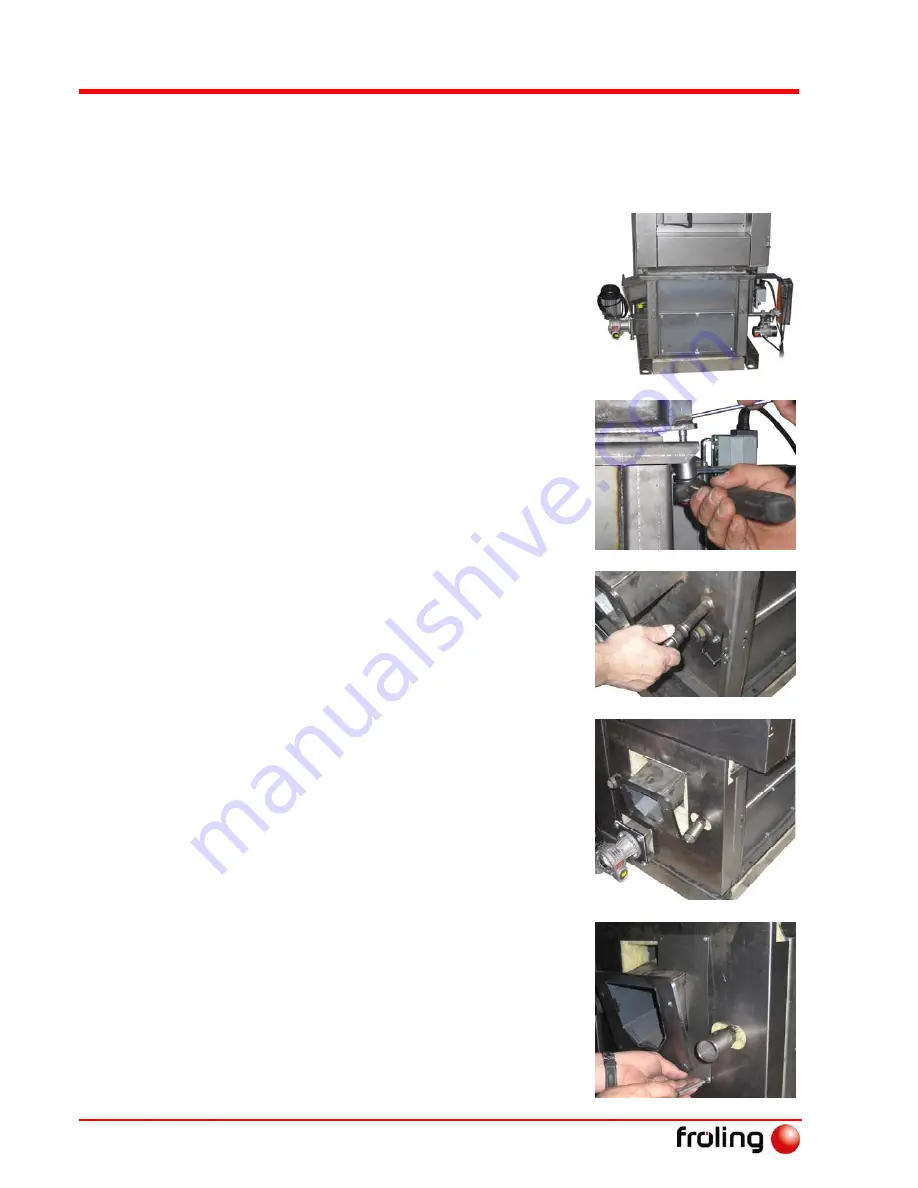
Installation
Assembly work
Page 16
M1010108_en
s
3
3.3
Assembly work
3.3.1
Installing the chamber in the boiler
The chamber can be installed with the
stoker connection on the right or the
left.
U
Turn the chamber according to the
discharge side and position on the
base of the boiler
Ensure that the seal is centred and
in the correct position.
U
Screw the chamber to the boiler
Ensure an even contact pressure.
U
Screw reducing socket onto igniter
tube
U
Attach insulation on stoker side
U
Screw in ignition sleeve on reducing
socket
Only carry out the following assembly
step on the G50 stoker shown. If you are
using a G30 stoker you must first fit the
stoker
U
Fit the stoker duct cover plates