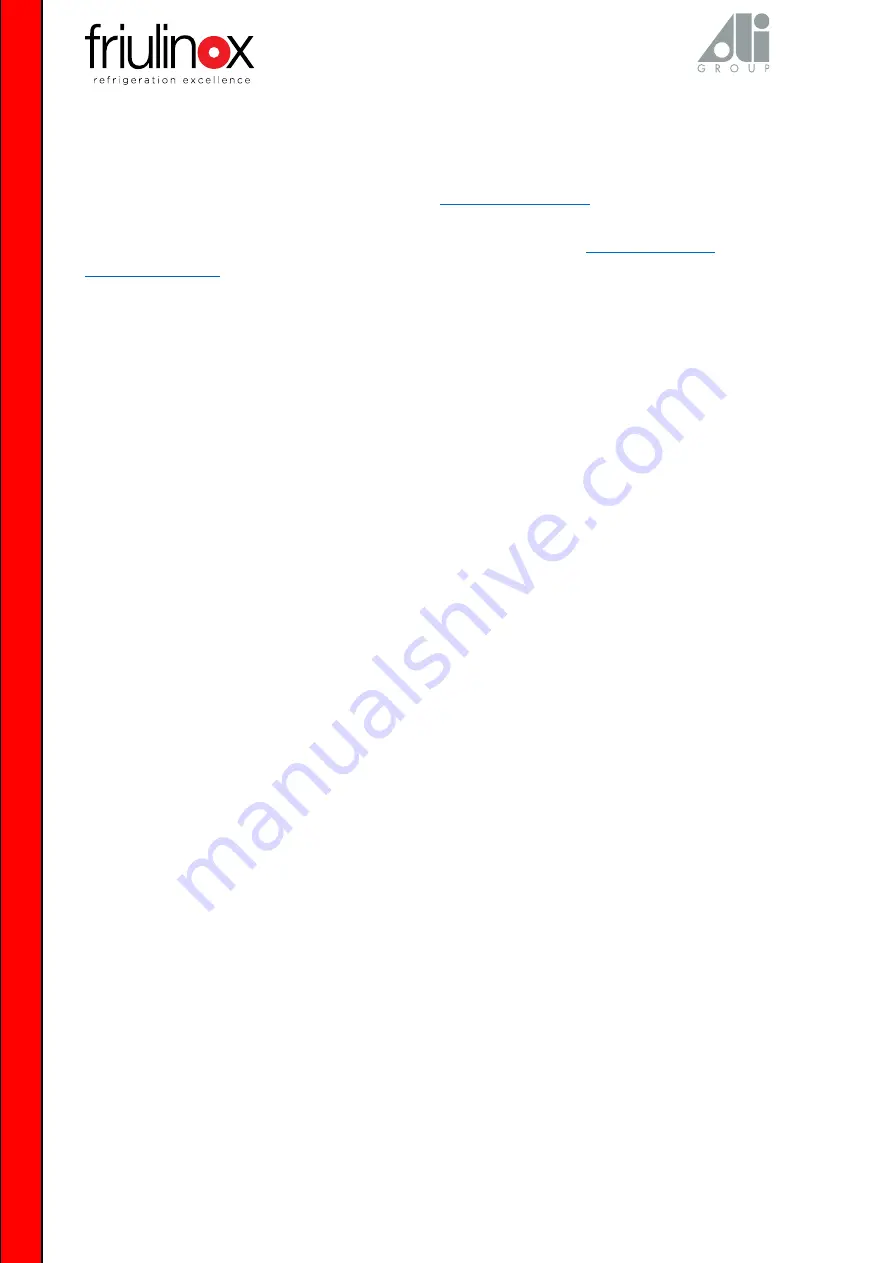
“go to
FRIULINOX ALI GROUPS.R.L. A SOCIO UNICO
88
Via Treviso,4 - 33083 Taiedo di Chions (PN) -Italy
Servi
ce
M
an
u
al
11.
SERVICE CONTACTS
For any technical request on our products, contact the FRIULINOX Technical Support on +39 0434635423 or
the Back Office on +39 0434 429086, or via e-mail to
Quotes and spare parts orders can be made directly through the website
, via e-mail to
Personnel is available from Monday to Friday from 8:30 to 12:30 and from 13:30 to 17:30.