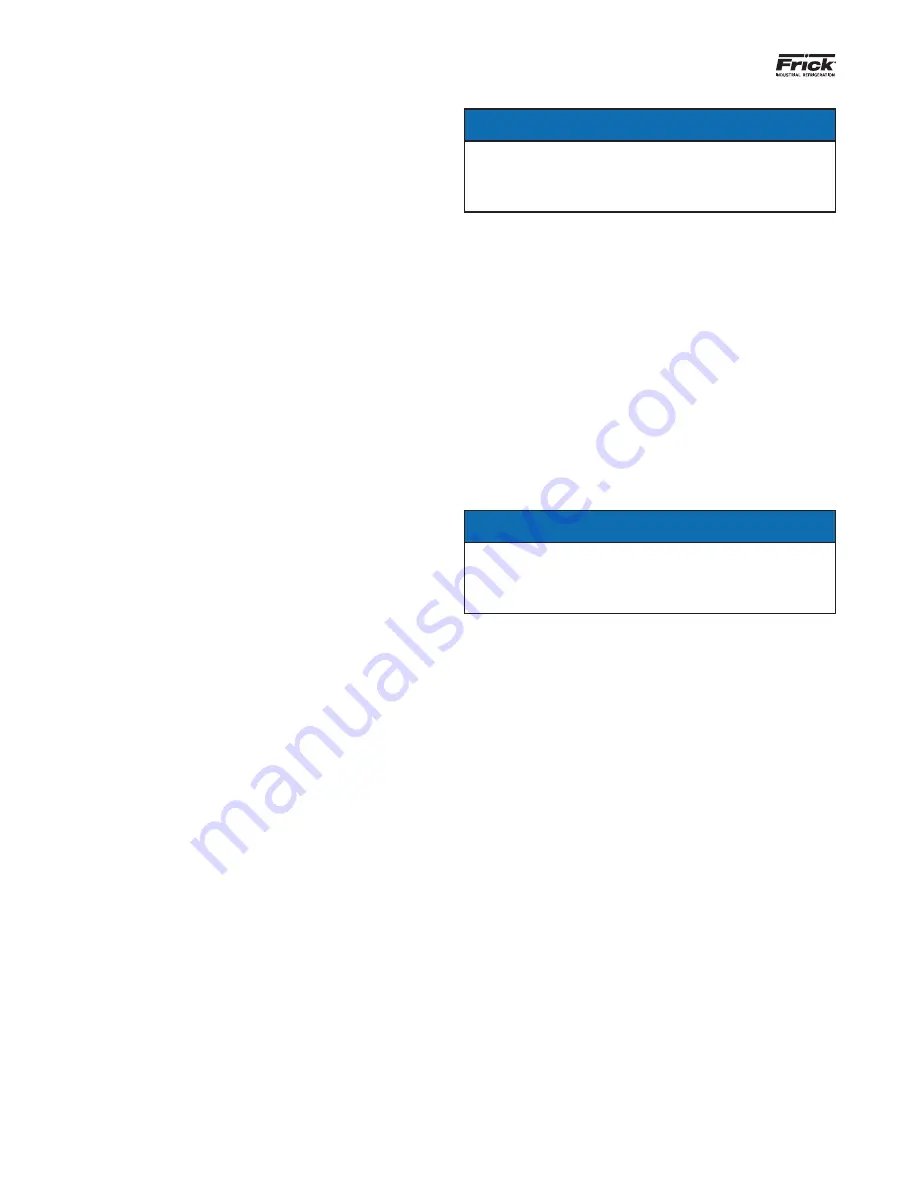
140.925-IOM (APR 2019)
Page 30
XLP3 EVAPORATIVE CONDENSERS
MAINTENANCE
transfer, promote corrosion, and promote the growth of
potentially harmful organisms such as Legionella.
•
To avoid biological contamination and minimize the risk
of Legionella, initiate the biocide treatment program at
start-up and continue on a regular basis thereafter in
accordance with the treatment supplier’s instructions.
• Bleed/blowdown or chemical treatment used for corrosion
and scale control alone is not adequate for control of
biological contamination.
• Introduce solid or granular biocides through a chemical
“pot” feeder installed in parallel with the system circulating
pump. Diluted liquid biocides may be added directly to the
cold water basin.
Long Term Care of Stainless Steel
When the percentage of chromium in steel exceeds 10.5%, it is
called stainless steel. The chromium in the steel reacts with the
oxygen in the air to form a chromium-oxide surface layer, also
called the passivation layer that provides the corrosion resistance
in stainless steel.
Frick’s Manufacturing Process
Frick takes precautions to prevent cross-contamination, process-
ing galvanized and stainless steel parts separately. Also, stainless
steel brushes are used to clean welds on stainless parts and care
is taken to avoid scratching parts during processing. Organic
cleaners are used to clean the finished product prior to shipping.
Jobsite Considerations
While stainless steel itself does not rust so long as the chromium-
oxide surface layer is intact, it is not immune to contamination
from its surroundings. Some common sources of surface con-
tamination are:
• Dirt and soil
• Shop oil or grease that may carry other contaminants such
as metal chips
• Machining or welding galvanized steel at the jobsite may
cause debris to impinge itself into the stainless steel
These contaminants can deposit on the surface and scratch the
passivation layer or prevent it from re-forming. They can also
get trapped underneath the passivation layer and reduce cor-
rosion resistance.
Recommended Cleaning Procedure
Stainless steel needs to be cleaned regularly to maintain the
corrosion resistance as well as to maintain the overall aesthetics
of the stainless steel.
It is fairly simple to clean most contaminants off the surface of
stainless steel. Most dirt and soil can be cleaned with a clean
cloth, warm water, and mild detergent. For persistent dirt, a little
vinegar can be added in the cleaning water. It is important to
always rinse the surface with warm water and wipe with a dry
cloth after any cleaning, whether mild or aggressive.
• Fingerprints, mild stains or grease spots can be cleaned
using organic solvents such as acetone, methyl or ethyl
alcohol, or mineral spirits. Stainless steel wipes or glass
cleaners commonly available in stores may also be used.
NOTICE
Never use chloride or chlorine based solvents such as
bleach or muriatic (hydrochloric) acid to clean stainless
steel. It is important to rinse the surface with warm water
and wipe with a dry cloth after cleaning.
• Occasionally the surface of stainless steel can get iron
chips or shavings embedded in it from having galvanized
steel machined or welded in the vicinity. The iron chips
can start to rust, reducing the corrosion resistance
of the stainless steel, and stain the surface giving the
impression that the stainless steel is rusting. These types
of contaminants require more aggressive cleaning. Mild
abrasives such as Scotch-Brite™ products may be used
where aesthetic considerations are not important followed
by solvent cleaning with organic solvents as described
above. It is important to rinse the surface with warm water
and wipe with a dry cloth after cleaning.
• If the iron chips are not removed with the Scotch-Brite™
Products, electro-chemical cleaning may be required. Frick
uses commercially available equipment for electrochemical
cleaning in the field. Contact your local Frick Representative
for more information.
NOTICE
Long term care of stainless steel information reprinted
with permission from “The Care and Cleaning of Stainless
Steel”; Specialty Steel Industry of North America; http://
www.ssina.com.
System Cleaning
Coil Cleaning
The outside of the coil may require occasional cleaning. The
chemicals used must be compatible with the materials being
treated. For example, the standard coil outside is galvanized
steel. The inside of the coil is black carbon steel. For specific
recommendations on coil cleaning, contact a qualified consultant.
Weld Byproduct Cleaning
The installation and manufacturing processes commonly used for
field assembly of steelpiped systems may leave weld byproducts
inside coils and connecting piping (especially in refrigeration
systems). It is common practice to install filters and/or strain-
ers that remove contaminants during initial system operation.
Shortly after system start-up, the filters and/or strainers should
be cleaned or replaced.
BLEED RATE
In evaporative cooling, evaporation of a small portion of the recir-
culating spray water as it flows through the equipment causes the
cooling effect. As this water evaporates, the impurities originally
present remain in the recirculating water. The concentration of
the dissolved solids increases over time and can reach unaccept-
able levels. In addition, airborne impurities are often introduced
into the recirculating water. If these impurities and contaminants
are not effectively controlled, they can cause scaling, corrosion,
and sludge accumulations that reduce heat transfer efficiency
and increase system operating costs, potentially shortening