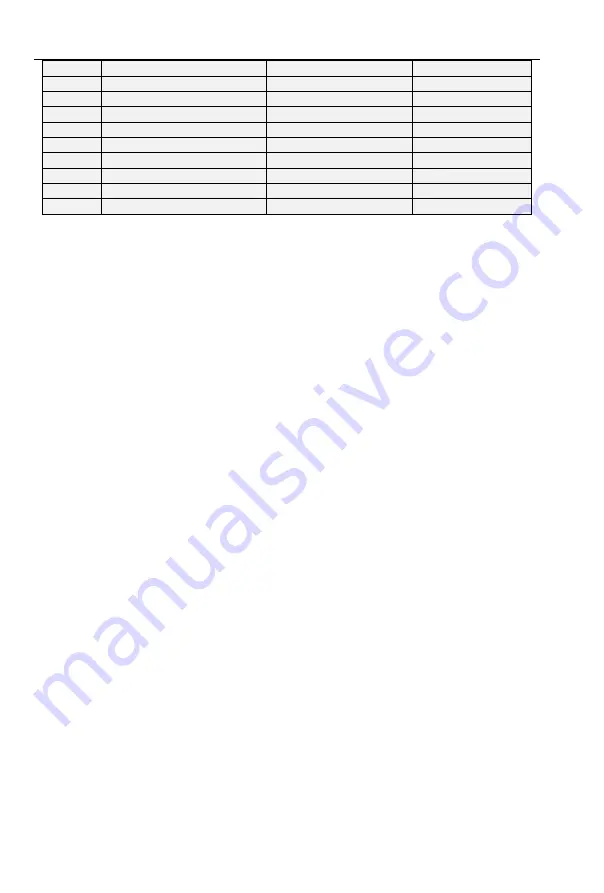
FR500A&FR510A Series Vector Control Inverter
- 142 -
F21.23
Carry amount 3 high value
Range
:
0
~
9999
Default
:
0
F21.24
Carry amount 3 low value
Range
:
0
~
9999
Default
:
0
F21.25
Carry amount 4 high value
Range
:
0
~
9999
Default
:
0
F21.26
Carry amount 4 low value
Range
:
0
~
9999
Default
:
0
F21.27
Carry amount 5 high value
Range
:
0
~
9999
Default
:
0
F21.28
Carry amount 5 low value
Range
:
0
~
9999
Default
:
0
F21.29
Carry amount 6 high value
Range
:
0
~
9999
Default
:
0
F21.30
Carry amount 6 low value
Range
:
0
~
9999
Default
:
0
F21.31
Carry amount 7 high value
Range
:
0
~
9999
Default
:
0
F21.32
Carry amount 7 low value
Range
:
0
~
9999
Default
:
0
Simple carry control is performed when F21.00 is selected as 4:
1) After the frequency converter receives the operation command, it immediately locks in the
current position, and the "positioning completion" terminal outputs ON signal.
2) When the output of "positioning completion" terminal is ON, if receiving the rising edge of
"positive carry" or "reverse carry" terminal from OFF to ON, that is to say, detecting the combination
state of "carry selection terminal 1-3" at the moment, determining the carry, and then starting to speed
up the operation to the set frequency. Acceleration time is set by F03 function codes and set frequency
by F01 function selection. At this time, the operation process is exactly the same as the normal speed
control operation.
3) When approaching the set position, the acceleration and deceleration time selected according
to F03 functional codes will stop. When the motor stops, it reaches the target position and is locked in
the target position. When the error between detection position and setting time of encoder is less than
the setting value of F21.03 and the duration reaches the setting value of F21.04, it is considered that
the positioning is completed and the switch output "positioning is completed" terminal output ON
signal.
4) During the period when the output of the "positioning completion" terminal is ON, if the rising
edge of the "positive carry" or "reverse carry" terminals from OFF to ON is detected, the next carry is
carried out from step 2.
★:
Note
:
1. In simple carry control, the direction of rotation of the motor is determined by the "forward carry" and
"reverse carry" terminals, which have nothing to do with the direction of the operation command.
2. The rising edge of "forward carry" or "reverse carry" terminals from OFF to ON can only be accepted
during the completion of the previous positioning, and the terminal signals of "forward carry" or "reverse
carry" are not accepted when the previous positioning is not completed.
3. The combination state of "carry selection terminals 1-3" is detected at the rising edge of "forward
carry" or "reverse carry" terminals from OFF to ON. Therefore, please determine the status of carry
terminals before the rising edge.
4. When the deceleration stops near the set position, the deceleration time is set by F03 functional codes.
The deceleration mode is linear deceleration, and the S-curve and DC braking mode are invalid.
5. When the carry instruction value is small, it can't reach the set frequency. After accelerating to a certain
frequency, it can directly decelerate and stop, as shown in Curve B of Figure 6-31.
6. If there is a stop command in the simple carry process, exit the carry control and stop according to the
set deceleration time, as shown in Fig. 6-31 Curve C.
7. Simple carry control can adjust F21.01 parameters appropriately. Increasing this value can increase the
rapidity of position control and the holding force when servo stops, but too large this value may cause
vibration and overshoot.
8. When there is a deceleration ratio between encoder and motor, please set F08.27 correctly.
The setting of carry instruction value: Each carry is composed of 8-bit 10-digit numbers of high
and low bits, and the setting range is 0-999999. The definition of carry is the distance of motor rotation
starting from the current servo lock position. Please set the carry according to 4 times of the number of
encoder pulses.
For example, using 1024 line encoder, if you want to carry 20 revolutions, then carry:
1024 (number of coder lines)* 20 (number of rotating cycles)* 4 (frequency doubling)= 81920,
Set carry high (such as F21.17) = 8, carry low (such as F21.18) = 1920.
By inputting different combinations of "carry selection terminals 1-3" into the switch quantity, up to