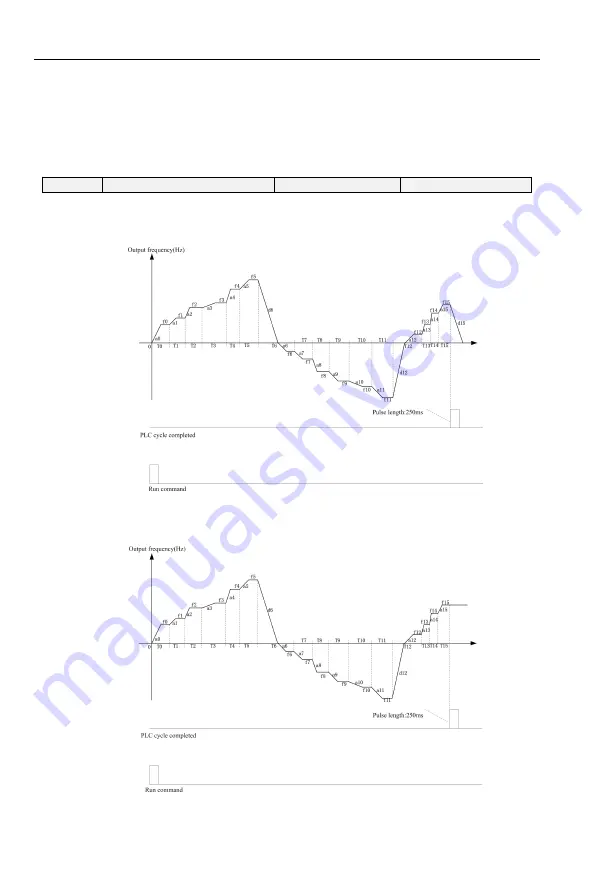
FR500A&FR510A Series Vector Control Inverter
- 124 -
1: keypad potentiometer
2: AI1
3: Process PID output
4: X7/HI pulse input
5: AI2
6: AI3
It determines the setting channel of reference 0. You can perform convenient switchover between
the setting channels. When multi-reference or simple PLC is used as frequency source, the switchover
between two frequency sources can be realized easily.
F12.17
Running mode of simple PLC
Range:0000
~
1132
Default:0000
Unit's place: PLC running mode
0: Stop after a single cycle
PLC stops upon the completion of one cycle and it won’t be started unless another run command
is given, shown as Fig. 6-22.
Fig. 6-30
1: Continue to run with the last frequency after a single cycle
After the completion of one cycle, PLC maintains the running frequency and direction of the last
step. See the figure below:
Fig. 6-31
2: Repeat cycles