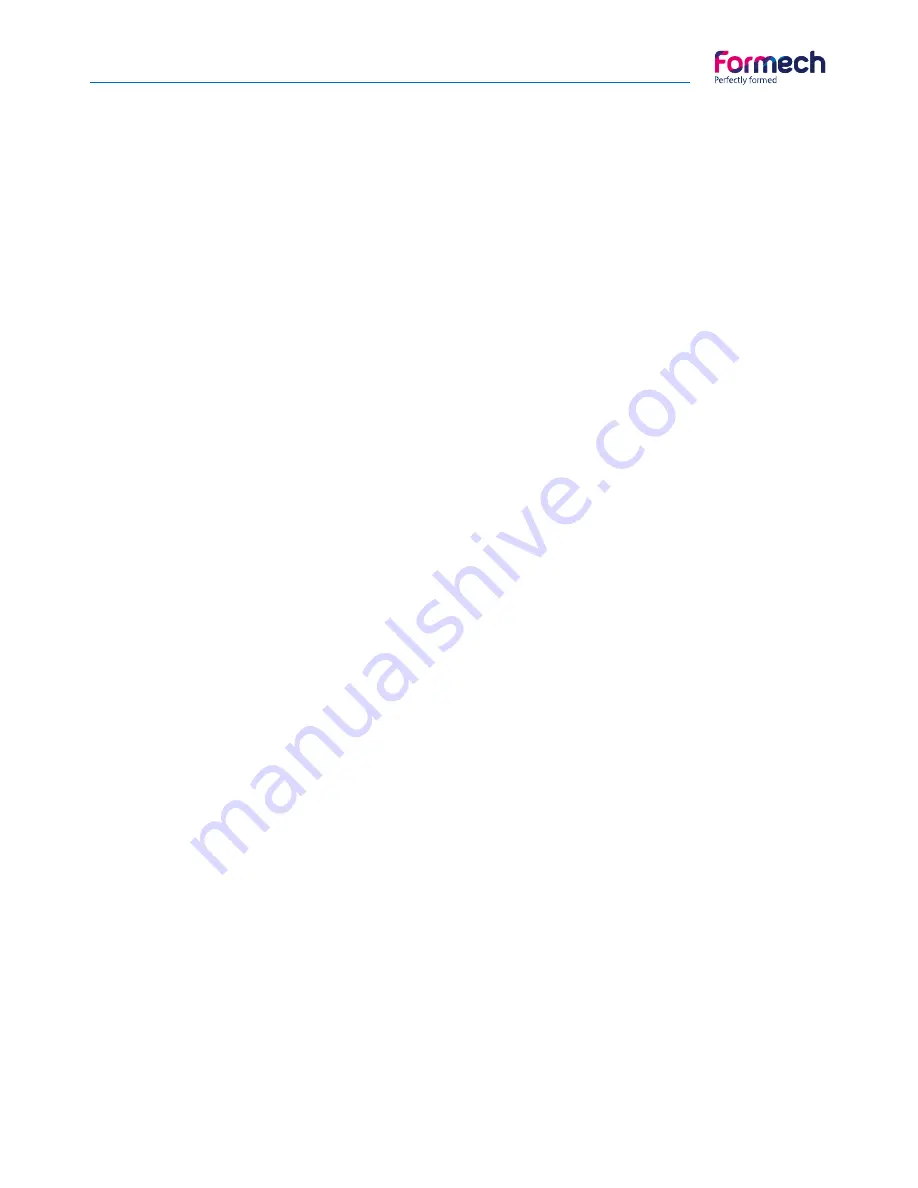
Manual - Formech Compac Mini
29
Service / Repair
Vacuum / Pressure system (continuation)
To check the entire vacuum system:
• Remove the 6 self-tapping screws securing the back panel.
• Remove the nut securing the motor capacitor to the left-hand side of the machine.
• Remove the 2 wires from the capacitor, terminating in the connector block next to the IEC socket.
• Remove all earth wires connected to the earth stud in the base of the machine.
• Remove the 4 nuts attaching the vacuum pump to the base.
• Remove the 6 self-tapping screws attaching the white front panel.
• Remove the 4 self-tapping screws along each bottom side of the machine.
• Rest the machine on its side and remove the 2 self-tapping screws in the base (roughly in the centre).
• Remove the base plate.
• Examine all piping carefully. Replace any suspect pipes.
• Remove the pipes from the vacuum\pressure valve. Take out the 2 fixing bolts.
• Blow through the single hose tail. You should feel air coming out of one hose tail on the opposite side. Ope-
rate the valve and air should pass freely through the other hose tail and shut off the first one.
• If the valve does not freely pass air or is otherwise malfunctioning then fit a new one or dismantle and
clean the faulty part.
• If the pump runs but does not appear to produce pressure or vacuum send it back to us for further evalua-
tion.
• Reassemble the machine taking great care to ensure that all electrical connections are tight and properly
insulated.
Make certain that the earth stud is tightened fully and that all earth wires are properly fixed to it.
If you are unable to cure any problem relating to your machine, or if you wish to order spare parts please
contact us at the below address, stating the model (Compac mini) the serial No. (on specification plate) and
a full description of the fault or parts you need.
Cleaning
Ensure the inside of the machine and the heater tray is cleared of dust, dirt and debris. Do not allow dirt and
loose particles to build up, particularly on the heater tray.
Lubrication
The Compac Mini requires minimum lubrication.
Apply general purpose grease to the table guide bars when required to assist with table movement.
Apply a small amount of fine silicone oil or fine oil to the heater slide bars when required to assist free move-
ment of the heater.