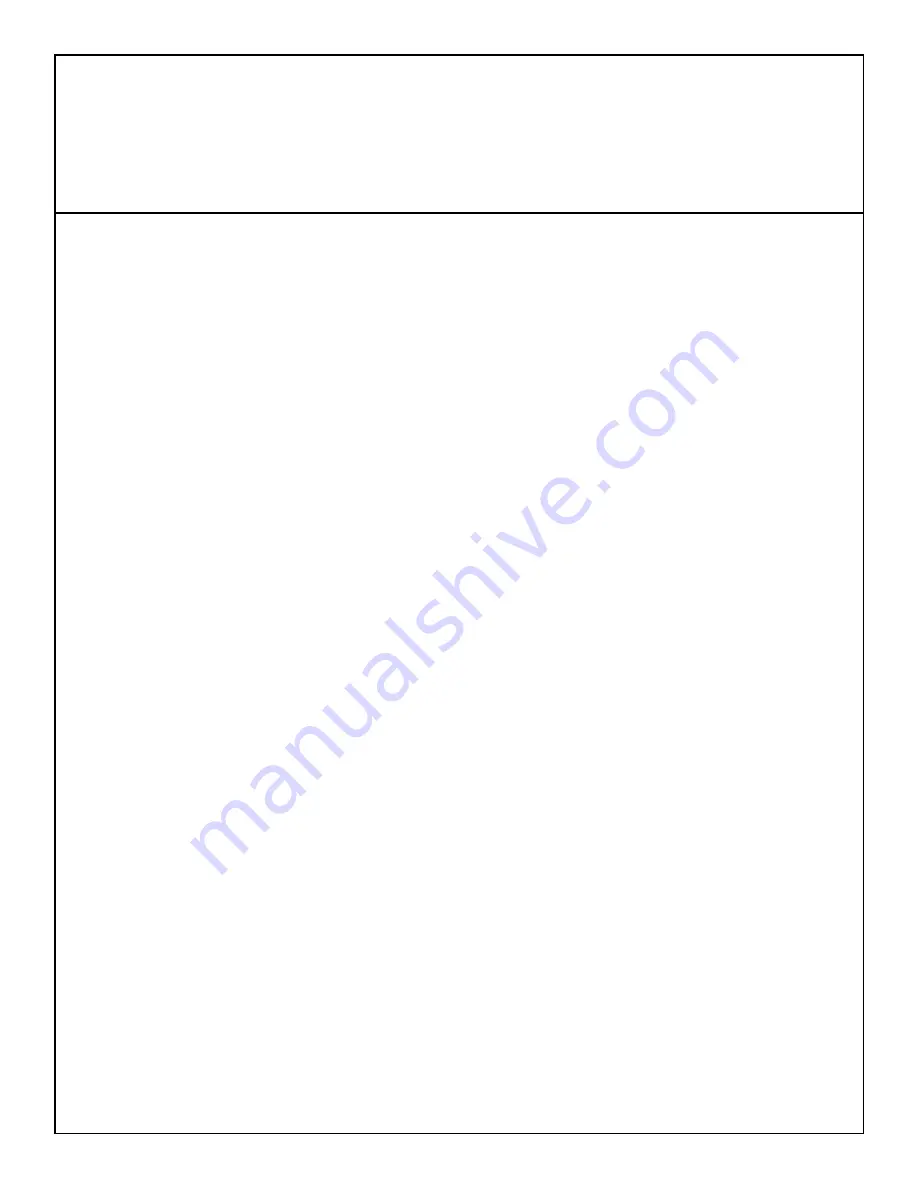
27
OPERATION
READ CAREFULLY BEFORE ATTEMPTING TO OPERATE OR SERVICE YOUR OPTIONAL ELECTRIC
WINCH OR OPTIONAL WORKSTATION! FAILURE TO COMPLY WITH INSTRUCTIONS COULD RESULT
IN PERSONAL INJURY AND/OR PROPERTY DAMAGE!
FOR YOUR OWN SAFETY AND THAT OF OTHERS, THIS EQUIPMENT MUST BE USED
AS RECOMMENDED BY THE MANUFACTURER. FAILURE TO HEED THE FOLLOWING
RECOMMENDATIONS COULD ENDANGER YOUR LIFE.
1. Maximum lifting capacity is 400 pounds (180
kg.) in single line winch operation.
DO NOT
ATTEMPT TO MOVE LOADS GREATER THAN THIS
RATINGS.
2.
NEVER CARRY
personnel on the hook/ramp or the
load.
3.
NEVER MOVE A LOAD
with this winch/
workstation until all personnel are clear.
4.
DO NOT ALLOW
unqualified personnel to operate
this unit.
5.
KEEP CLEAR OF RAMP OR WINCH WIRE ROPE
AND HOOK WHEN OPERATING.
DO NOT ATTEMPT
to guide wire rope by hand as it rewinds.
6.
AVOID
excessive inching and quick reversals of
load.
7.
BE SURE
that the power supply is disconnected
before performing maintenance and repair
procedure.
8.
DO NOT OPERATE
this unit if it is not functioning
properly.
9.
KEEP WORKSTATION/WINCHING AREA CLEAR
.
Do not allow people to remain in the
workstation/winching area. Do not stand between
the winch and load.
11.
ALLOW WORKSTATION/WINCH TO COOL
DOWN FREQUENTLY
, as the motor is designed for
intermittent duty only. When the metal motor
housing is hot to touch, it is time to let the winch
cool down.
12.
DO NOT OPERATE WORKSTATION/WINCH
WHEN UNDER THE INFLUENCE OF DRUGS,
ALCOHOL, OR MEDICATION.
13.
DO NOT USE WORKSTATION/WINCH TO HOLD
LOADS IN PLACE
. Use other means of securing
loads, such as tie down straps.
14.
USE ONLY FACTORY APPROVED SWITCHES,
REMOTE CONTROLS AND ACCESSORIES
.
Use of non-factory approved components may cause
injury or property damage and could void your
warranty.
15.
DO NOT MACHINE OR WELD ANY PART OF
THE WORKSTATION/WINCH
. Such alterations may
weaken the structural integrity of the workstation/
winch and could void your warranty.
16.
DO NOT OPERATE THIS WORKSTATION/WINCH
OUT DOORS OR IN A CORROSIVE OR EXPLOSIVE
ENVIRONMENT
.
NOTE: THE FOLLOWING APPLY TO OPERATION
OF THE WINCH ONLY
.
1.
MAINTAIN A MINIMUM OF 4 TURNS OF WIRE
ROPE
around the winch drum to prevent the wire
rope from pulling off under load.
2.
WHEN SPREADER BAR ASSEMBLY IS USED
be
sure it is properly seated in the saddle of the hook.
3.
NEVER HOOK THE WIRE ROPE BACK ON
ITSELF. USE
THE SPREADER BAR ASSEMBLY
.
Hooking the wire rope back on itself creates an
unacceptable strain on the wire rope.
4.
DO NOT
use the wire rope as a ground for
welding.
5.
NEVER TOUCH
a welding electrode to the wire
rope.
6.
INSPECT WIRE ROPE FREQUENTLY
. A frayed
wire rope with broken strands should be replaced
immediately. Never replace the wire rope with rope
of any kind or with wire rope other than the type
and size specified in the repair parts section of this
manual.
7.
USE HEAVY LEATHER GLOVES
when handling
the wire rope to eliminate the possibility of cuts
or scratches from burrs and slivers from broken
strands.