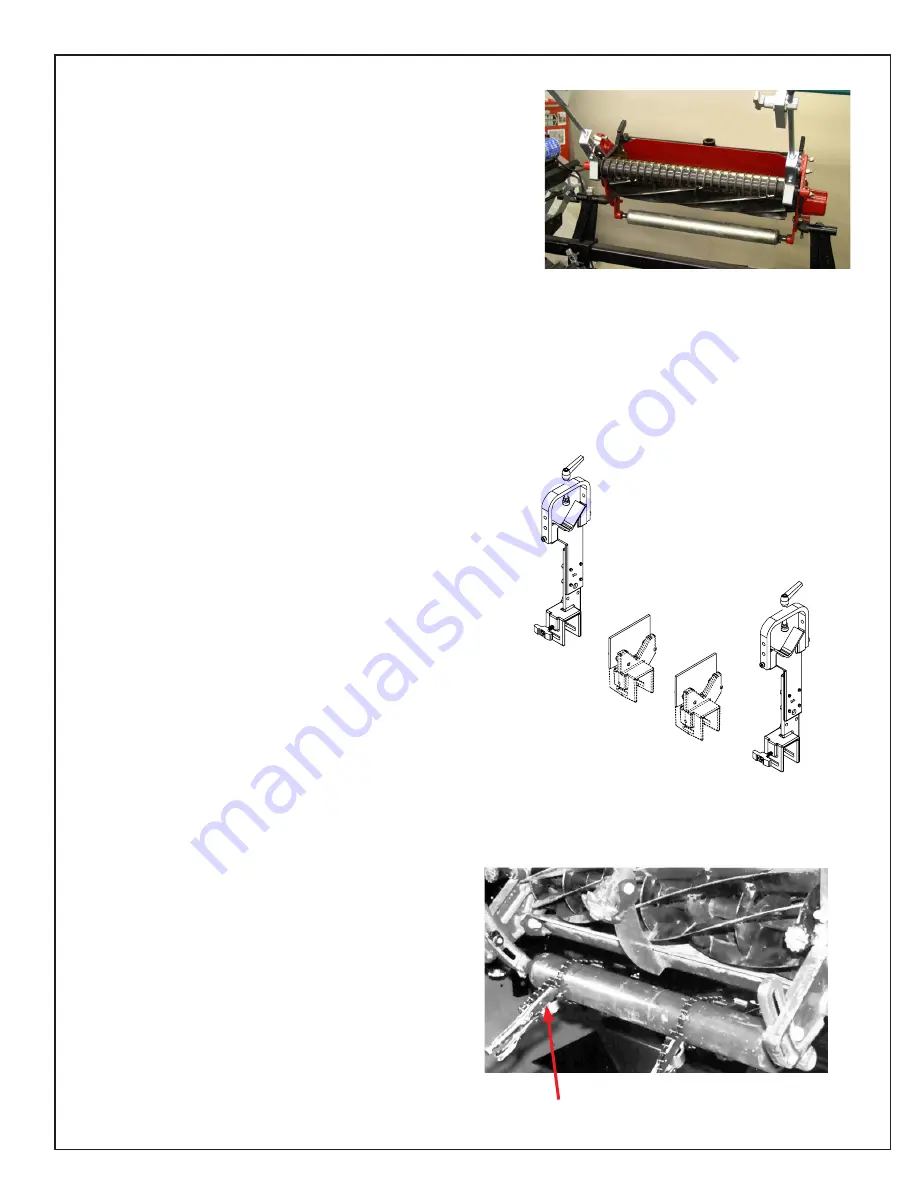
17
GETTING TO KNOW YOUR GRINDER
OPTIONAL PULL GANG BRACKETS
The
OPTIONAL
Pull Gang Reel Mount Kit 18574
consists of a lower mounting bracket that fits over the
square tooling mounting bar and two threaded locking
screws. Attached to this is the upper "V" bracket that
cradle the reel hub when in position. There are three
vertical adjustments on this fixture. The fixture will
normally be used in the upper hole position.
See FIG. 17.
These brackets can be mounted on the square
mounting bar with offset either forward or backwards,
but the normal position will be with the "V" centered
over the bar or with the offset facing the back of the
machine. The hold-down swing arm has an upper and
lower mounting position depending on mower hub
size.
The rear roller of the pull gang mowing unit attaches to
the roller supports as shown in FIG. 18.
FIG. 16
FIG. 18
CENTER MOUNTING BRACKETS
The centers mounting brackets consist of a stationary
center bracket and an adjustable center bracket. The
stationary bracket will normally be used on the left hand
side of the mounting bar when facing the reel loading
position. See FIG.16. The centering fixtures are used
primarily on greens mowers.
FIG. 17
VISE GRIP CHAIN
CLAMP