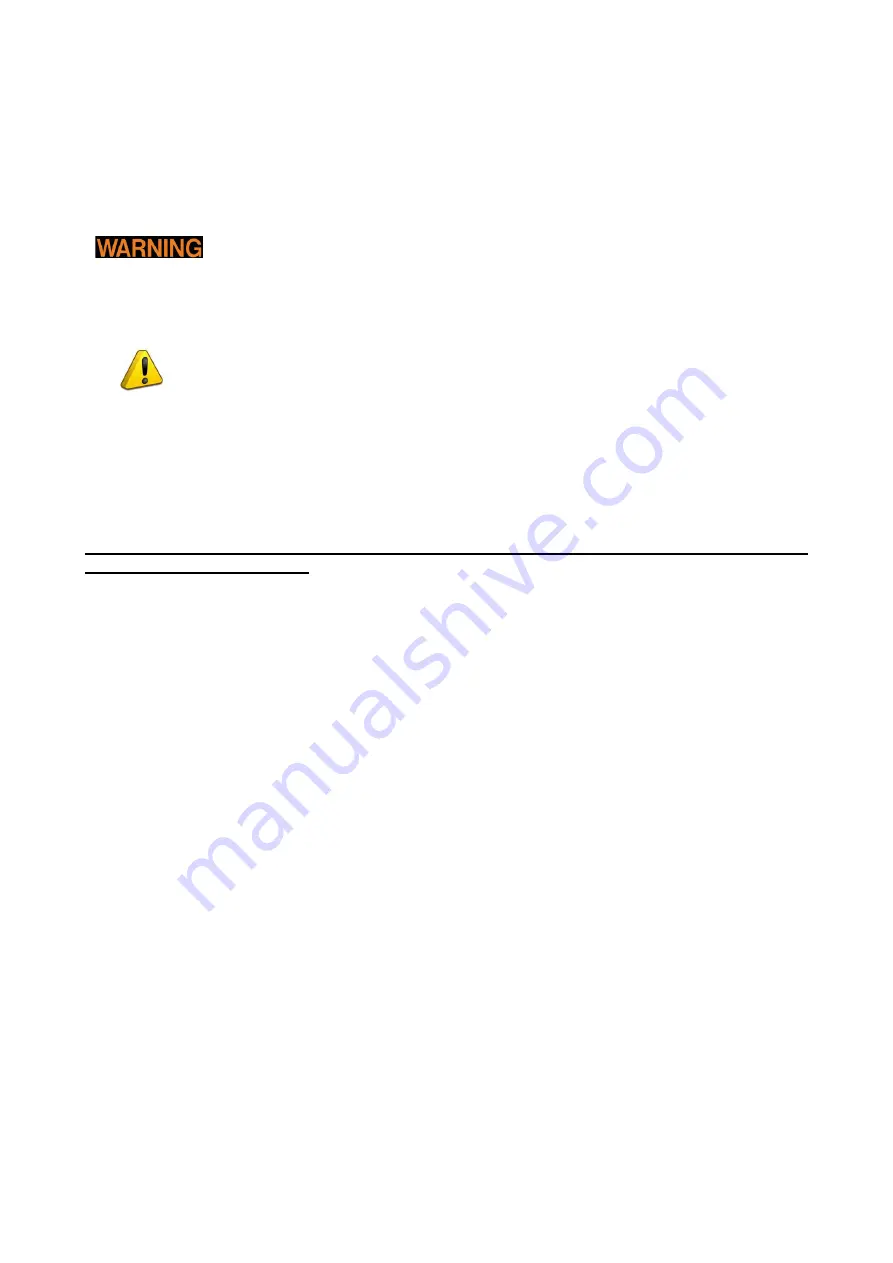
21
9.
BEFORE EACH START
Have a look of the emergency drops tubes , and check eventually gasoline leakage from that hole
Verify the Check-List of the aircraft manufacturer and depending on engine type
used. Verify that the level of the fuel is sufficient to support the planned travel.
Verify that the fuel valves are open.
Before every flight and especially when a long time travel is planned, it is
essential to check that there are no leaks in the gasoline system, as it might
occur, for many reasons, a leak that could be small at the beginning, but it may
increase over time. This loss would lead to a leakage of gas which inevitably
reduces the estimated autonomy of the flight, as well as be the cause of possible
fires.
With this regards, you must follow the precautions described below every time you "close"
the contact "Master switchs!
Whenever you connect the Master switchs ":
nobody or nothing must be near the propeller.
it is necessary to be always on board in order to be able to interrupt the contact
quickly (master).
keep the throttle completely closed.
Action brakes half
Place wedges in the wheels
Keep magnets in OFF position