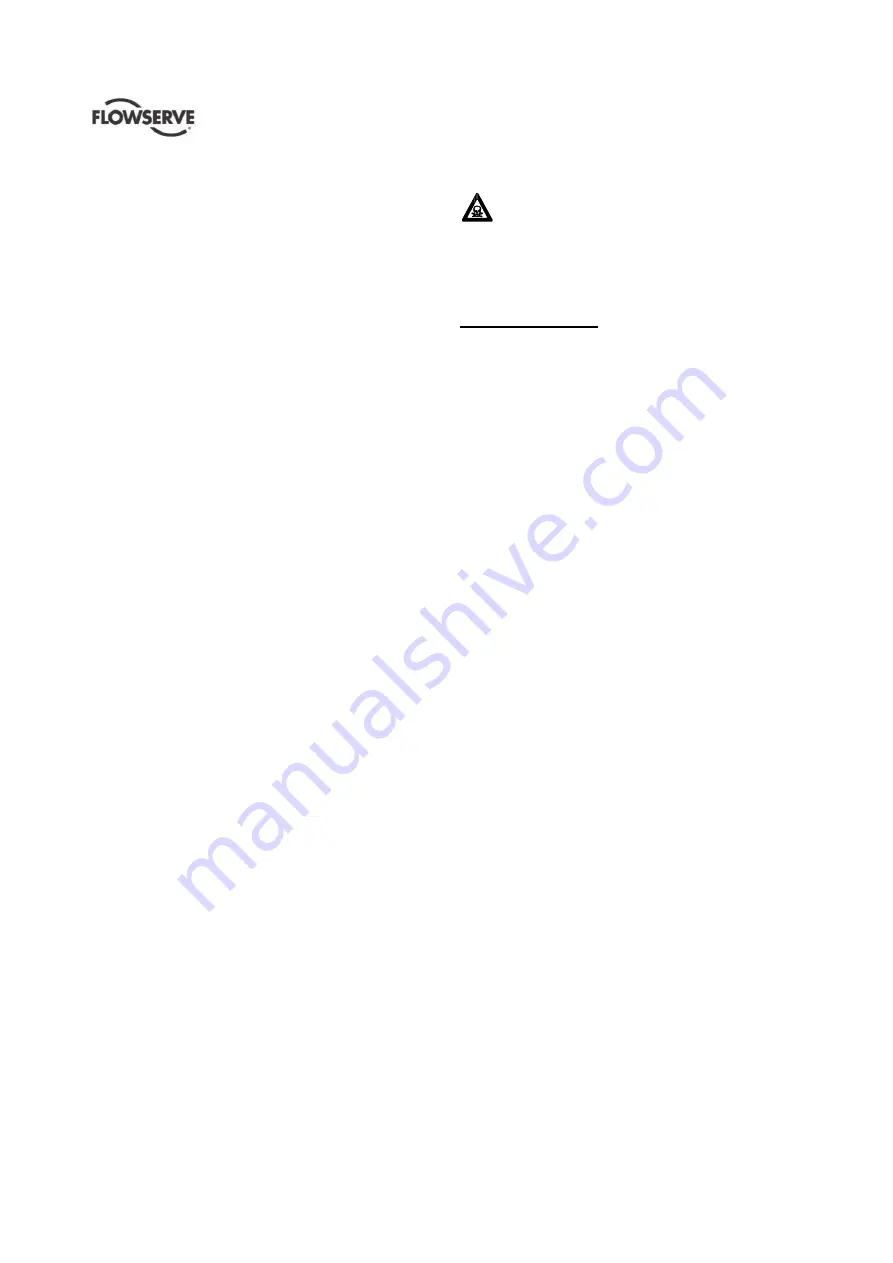
USER INSTRUCTIONS POLYCHEM GRP ENGLISH 71569132 12-04A
Page 11 of 52
flowserve.com
All loose unmounted items are packaged in a
waterproof plastic bag and placed under the
coupling guard. Larger items are boxed and
metal banded to the baseplate. For pumps not
mounted on a baseplate, the bag and/or box is
placed inside the shipping container.
Inner surfaces of the bearing housing, shaft (area
through bearing housing) and bearings are
coated with Cortec VCI-329 rust inhibitor, or
equal. (Note: bearing housings are not filled with
oil prior to shipment.)
Regreasable bearings are packed with grease.
(EXXON POLYREX EM for horizontal pumps.)
Exposed shafts are taped with Polywrap.
Flange covers are secured to both the suction
and discharge flanges.
Assemblies ordered with external piping, in some
cases components may be disassembled for
shipment.
The pump must be stored in a covered, dry location.
2.4.2 Long term storage
Long term storage is defined as more than six
months, but less than 12 months. The procedure
Flowserve follows for long term storage of pumps is
given below. These procedures are in addition to the
short term procedure.
Each assembly is hermetically (heat) sealed from
the atmosphere by means of tack wrap sheeting
and rubber bushings (mounting holes).
Desiccant bags are placed inside the tack
wrapped packaging.
A solid wood box is used to cover the assembly.
This packaging will provide protection for up to twelve
months from humidity, salt laden air, dust etc.
After unpacking, protection will be the responsibility of
the user. Addition of oil to the bearing housing will
remove the inhibitor. If units are to be idle for
extended periods after addition of lubricants, inhibitor
oils and greases should be used. Every three
months, the pump shaft should be rotated
approximately 10 revolutions.
2.5 Recycling and end of product life
At the end of the service life of the product or its
parts, the relevant materials and parts should be
recycled or disposed of using an environmentally
acceptable method and local requirements. If the
product contains substances that are harmful to the
environment, these should be removed and disposed
of in accordance with current regulations.
This also includes the liquids and or gases that may
be used in the "seal system" or other utilities.
Make sure that hazardous substances are
disposed of safely and that the correct personal
protective equipment is used. The safety
specifications must be in accordance with the current
regulations at all times.
3 DESCRIPTION
3.1 Configurations
PolyChem GRP chemical process pumps are end
suction, single stage, centrifugal pumps. The GRP
family conforms to ASME B73.5M as a non-metallic
wet end, end suction, centerline discharge
arrangement. There is also a self-priming option
available. These pumps are made of a glass-
reinforced polymer that is designed to handle a wide
range of chemicals. PolyChem GRP pumps may
often be used as a cost-effective solution where
stainless steel, Alloy 20, Monel, Nickel, Hastelloy ™,
and even titanium metal pumps are used.
3.2 Name nomenclature
The pump size will be engraved on the nameplate
typically as below:
2K 4 X 3G
–
13 / 12.5
Frame size:
“2K’ indicates a medium size pump frame with a
Mark3 power end - in this example, a Group 2.
1J or 1K = Group 1 (small frame)
2K = Group 2 (medium frame)
3J = Group 3 (large frame
–
2
⅜
in. shaft)
4J = Group 4 (large frame
–
2 ¾ in. shaft)
Power end:
Mark 3A
–
Standard
ANSI 3A
–
Optional (3 year guarantee)
“4” = Nominal suction port size.
“3” = Nominal
discharge port size.
“G” = PolyChem GRP pump line
“GS” = Self
-primer version
Nominal maximum impeller diameter:
“13” = 13 in
. diameter
Actual impeller size:
“12.5” = 12 ½ in. diameter
An example of the nameplate used on the PolyChem
GRP pump is shown below. This nameplate, which is
always mounted on the Mark 3 bearing housing, is
shown in figure 3-1.