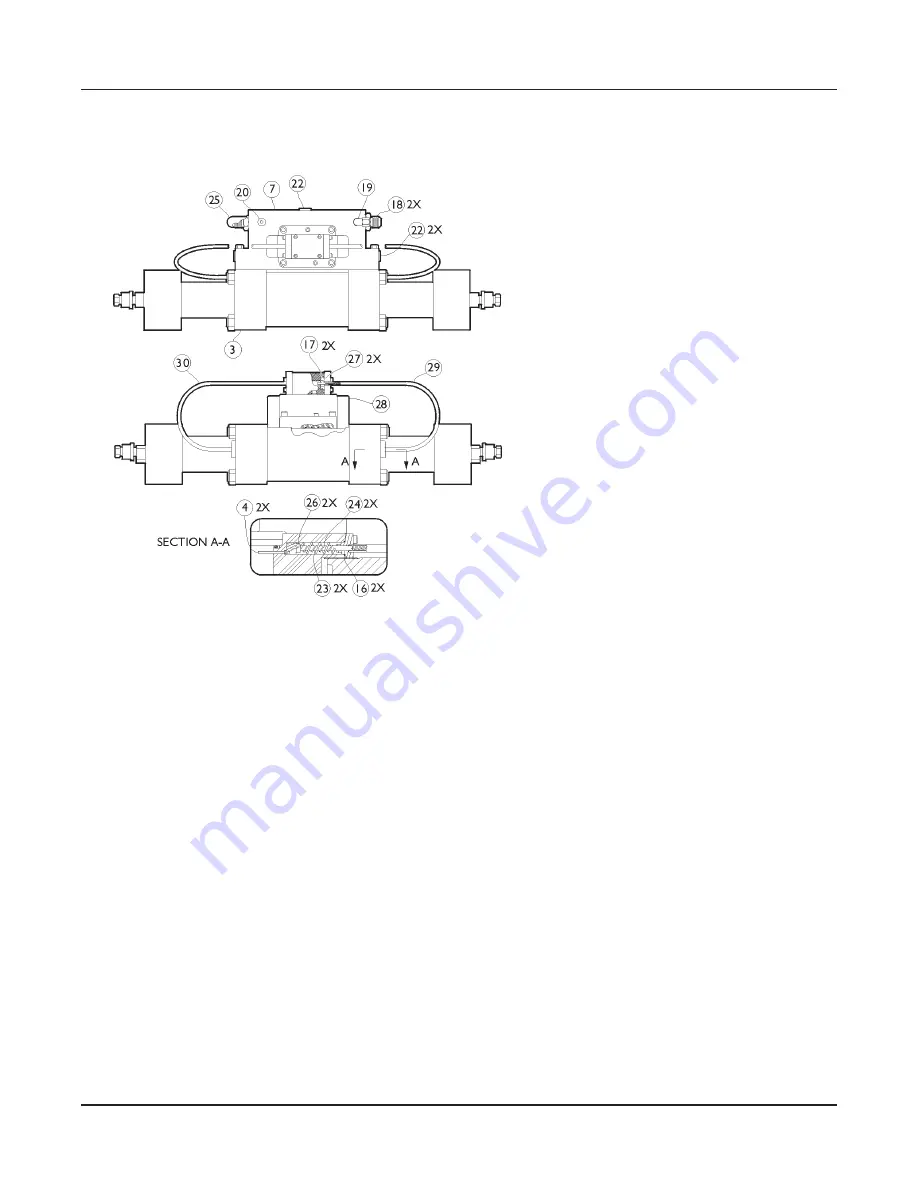
010639-X (Rev. H)
Manifold assembly, mechanical shift
Item Part #
Qty
Description
3
010558-30
1
Intensifier assembly
4
002226-1
2
Actuator pin
7
013403-1
1
Manifold
16
A-0275-014
2
O-ring
17
A-0275-019
2
O-ring
18
A-0636-23
2
Connector
19
A-0638-3
1
Elbow
20
A-0641-6
1
Plug
22
A-0641-7
3
Plug
23
A-1012
2
Spring
24
A-1713
2
Compression spring
26
B-1007-1
2
Actuating plunger
27
B-1611-1
2
Shift pin
28
A-11215
1
Shift valve/pilot valve assy
(C-2743-1, shift valve & 006869-1, pilot valve)
29
C-5461
1
Cable guide assembly, RH
30
C-5462
1
Cable guide assembly, LH
ESL Intensifier
© Flow International Corporation
M-310 | 37