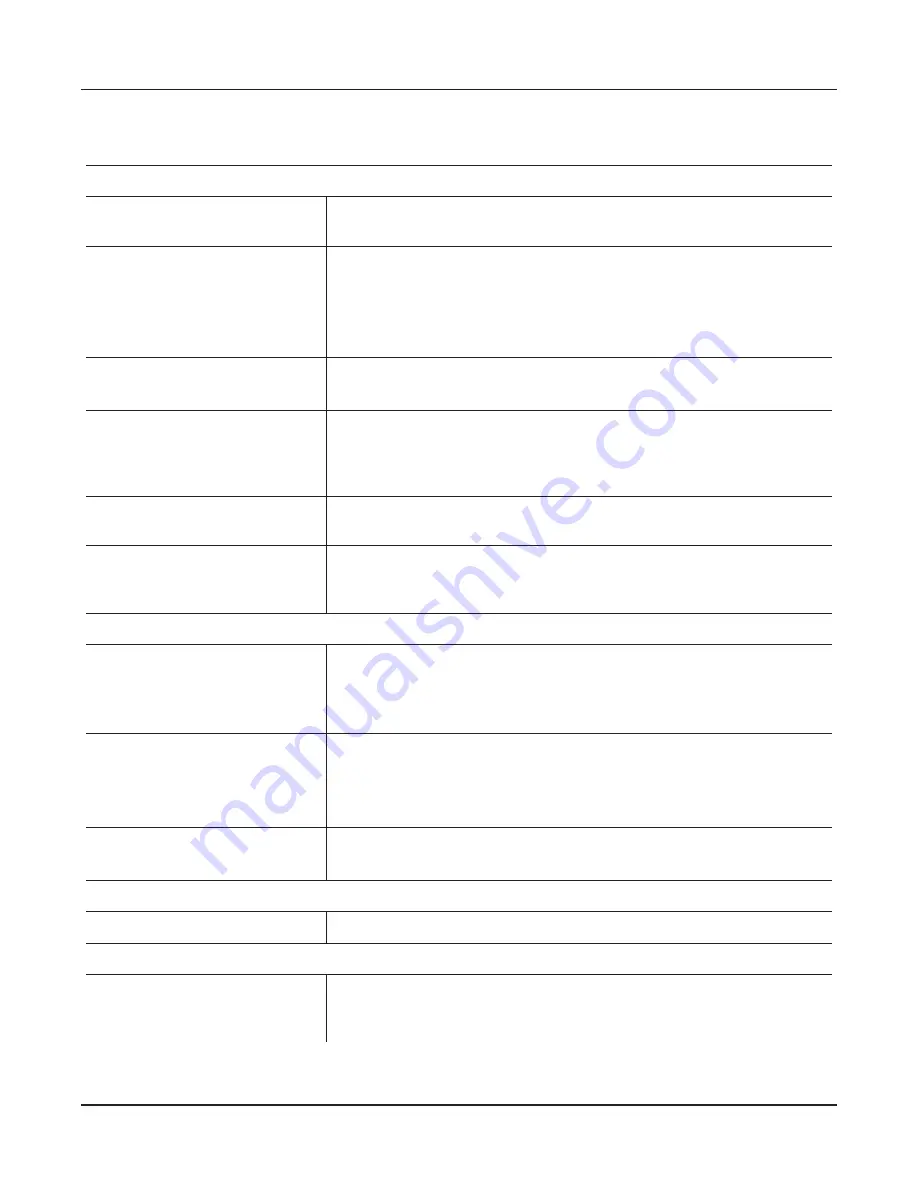
Troubleshooting guide
1. Intensifier strokes unevenly
Leaky check valve (inlet or outlet) on
one side only
Replace or rework the check valves as necessary. For best results, lap or re-
place all check valves at the same time.
Foreign particles trapped between
check valve and seat
1. Remove the end cap(s). Eliminate the sources of contamination to prevent
problem from recurring.
2. Examine the check valves and remove any foreign material. Relap if neces-
sary.
3. Clean all parts and reassemble.
Worn/bent shift cable or associated
parts (mechanical shift only)
1. Remove the shift cable guide.
2. Install the spare shift cable guide and recheck. Replace any worn parts.
High-pressure water plunger has
separated from the oil piston
Associated with a drop in output water pressure and flow. Avoid prolonged
operation under this condition—it will cause severe damage to the intensifier.
Disassemble the hydraulic oil cylinder and piston and replace parts if defec-
tive.
Wrong shift/actuator pins installed
Replace with bronze shift/actuator pins (002226-1 mechanical shift; B-1702-1
electric shift).
Debris in shift circuit
Check spool movement on both the pilot and shift valves. Inspect spools for
defects. Hand lap with 600 grit paper. If unable to remove defects, replace
valve.
2. Intensifier knocks severely
Low inlet water pressure to the in-
tensifier
1. Make sure the inlet water pressure output is above the required minimum
for your intensifier pump.
2. Replace filters in filtration system; make sure they are replaced in the same
order they were removed.
Intensifier inlet passages clogged by
debris or corrosion
1. Inspect the filtered water inlet lines.
2. Remove the end cap. Inspect and remove any foreign material clogging the
inlet passages.
3. Inspect the check valve.
Sticky outlet check valve poppet
1. Remove the end cap.
2. Relap the check valve poppet and the insert; reinstall.
3. Oil leakage from end bell weep hole
Worn end bell oil seal
Replace the end bell oil seals. Replace all oil seals at the same time.
4. Oil leaking from manifold/end bell interface
Defective/worn o-ring seals, or loose
manifold mounting screws or port
plugs on valve
Retorque the manifold mounting screws, following the torque values provided
in this section. If leak will not stop, replace the o-ring interface seals between
the manifold and the end bells. Lap manifold if the o-ring surface is nicked.
© Flow International Corporation
M-310 | 9
ESL Intensifier