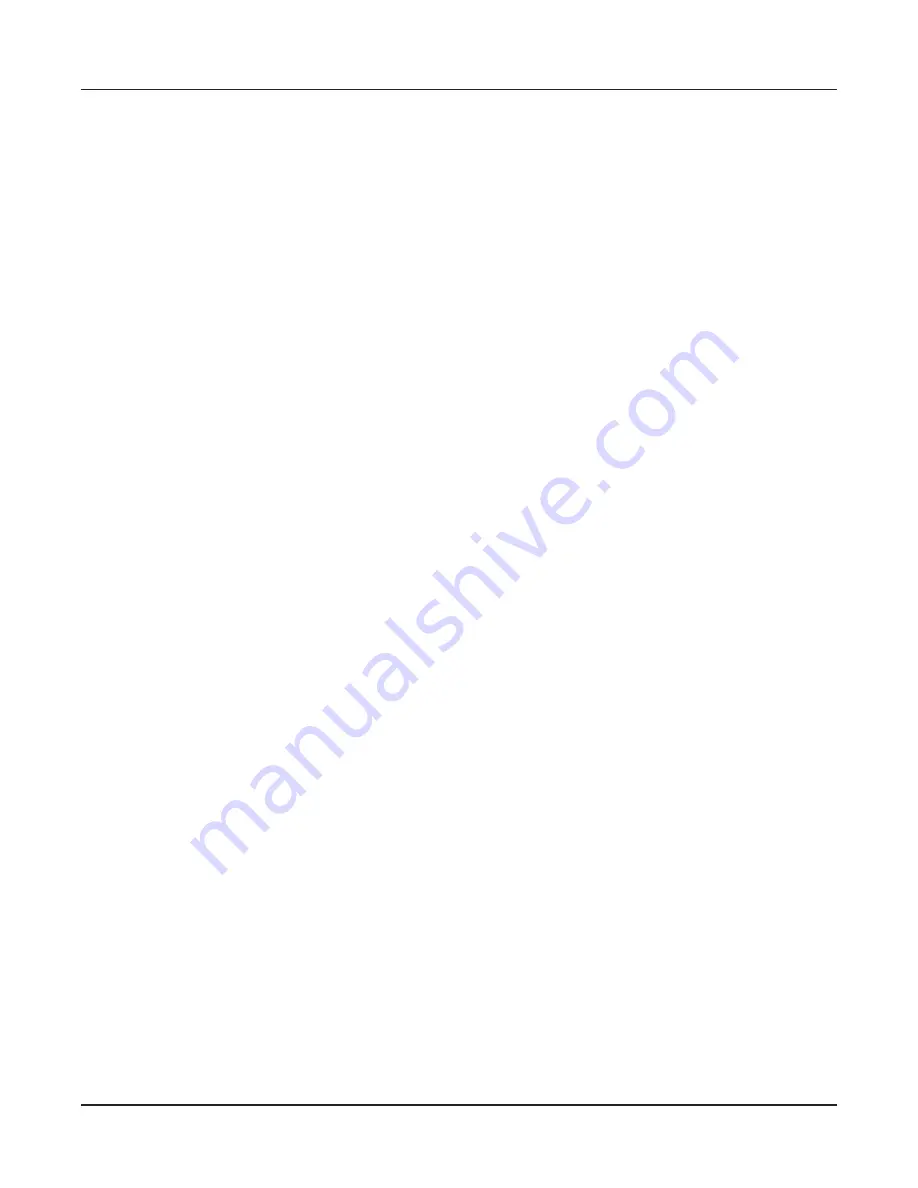
Service procedures
The service procedures contain step-by-step instruc-
tions and illustrations to explain how to service the
equipment. Service procedures cover how to replace
parts during scheduled or unscheduled maintenance,
and also include preventive maintenance procedures to
help ensure trouble-free operation of the machinery.
Note:
Information on high-pressure components (such
as swivels, filters, and tubing) is in manual M-127,
Small High-Pressure Components.
Intensifier service notes
The following list was compiled from Flow customers,
technicians, and operators. It can help to lower repair
costs, shorten repair time, and increase component life.
•
Read and understand each procedure before start-
ing any work on the intensifier pump.
•
Measure the amount of water seepage from the
end cap and end bell weep hole. If less than 2 tsp
(23 ml) per stroke and has not suddenly appeared
or increased drastically, you do not need to imme-
diately stop the pump and change seals. However
you should schedule maintenance as soon as
possible.
•
Except for a complete overhaul or repairs involving
the hydraulic oil cylinder, it is usually easier and
quicker to work on the intensifier while it is in the
cabinet (this is not recommended for dusty envi-
ronments such as paper, fiberglass or plastic
manufacturers).
•
Immediately replace all cracked check valve parts
and clean up leakage.
•
All threaded high-pressure connections require a
fresh, even coating of Blue Lubricant. Do not sub-
stitute another product.
•
Clean all parts with a clean, non-residue solvent
such as Citra-Safe or isopropyl alcohol. Use a dedi-
cated solvent tank if possible. Contamination from
other industrial parts will seriously reduce part life.
•
All parts that contain high-pressure water (cylinder,
check valve housing, tubing) are susceptible to
stress fatigue accelerated by stress risers. Stress ris-
ers are caused by scratches, nicks or other surface
disruptions. Rework damage or replace the
component.
•
High-pressure water seal life and the service life of
other parts are related to the stress put on the
parts—a function of stroke rate and water pres-
sure. Exceeding the pump ratings can lead to in-
creased cost and downtime.
•
Keep all intensifier tools supplied with the pump in
a separate locked cabinet. Substituting tools for
those supplied by or available from Flow is not
recommended.
•
Use the intensifier assembly fixture when reassem-
bling the hydraulic oil cylinder. Problems with
manifolds and leaking o-rings are significantly re-
duced when the fixture is used.
•
Keep the work area clean. When reassembling any
intensifier, remember that clean hands, shop coat,
rags, parts, tools, air, solvent, and lubricants all
contribute to lower maintenance costs and re-
duced downtime.
12 | M-310
© Flow International Corporation
ESL Intensifier