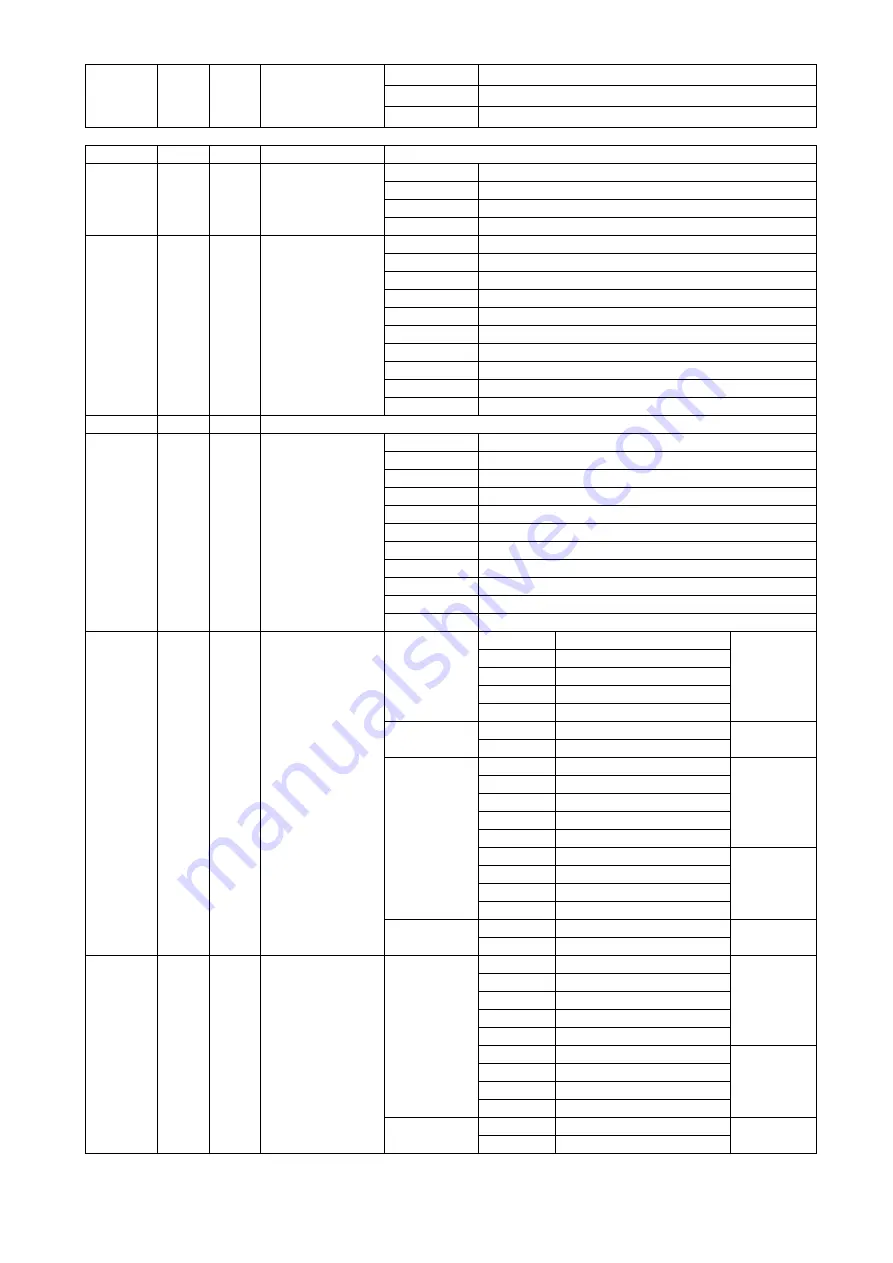
FAD-40 Technical Manual, Rev.2.1.0; February 2022
Page 28 of 55
2
Force Mode Unipolar
3
Force Mode Bipolar
4
Weight Mode Unipolar
Address R/W
Word Command
Definition
40015
R/W
1
mV operation
in Count Mode
0
5 mV
1
10 mV
2
15 mV
3
18 mV
40016
R/W
1
Digital filters
0
Fast
1
2
3
4
5
Medium
6
7
Default
8
9
Slow
40017
1
Not used
40018
R/W
1
Status of
Digital I/O
D0
Input of I/O3
D1
Input of I/O2
D2
D3
D4
D5
D6
D7
D8
Output of I/O1
D9
Output of I/O2
D10
Output of I/O3
40019
R/W
1
Setup for I/O1
and I/O2
D0…D6
0000000
Disable
I/O1 output
function
0000001
Standard setpoint
0000010
Setpoint without hyster.
0000011
Window
0000100
Host output
D7
0
Active Low
I/O1
polarity
1
Active High
D8…D14
0000000
Disable
I/O2 output
function
0000001
Standard setpoint
0000010
Setpoint without hyster.
0000011
Window
0000100
Host output
0000101
Zeroing
I/O2 input
functions
0000110
Taring
0000111
Clearing tare
0001000
Host input
D15
0
Active Low
I/O2
polarity
1
Active High
40020
R/W
1
Setup for I/O3
D0…D6
0000000
Disable
I/O3 output
function
0000001
Standard setpoint
0000010
Setpoint without hyster.
0000011
Window
0000100
Host output
0000101
Zeroing
I/O3 input
function
0000110
Taring
0000111
Clearing tare
0001000
Host input
D7
0
Active Low
I/O3
polarity
1
Active High