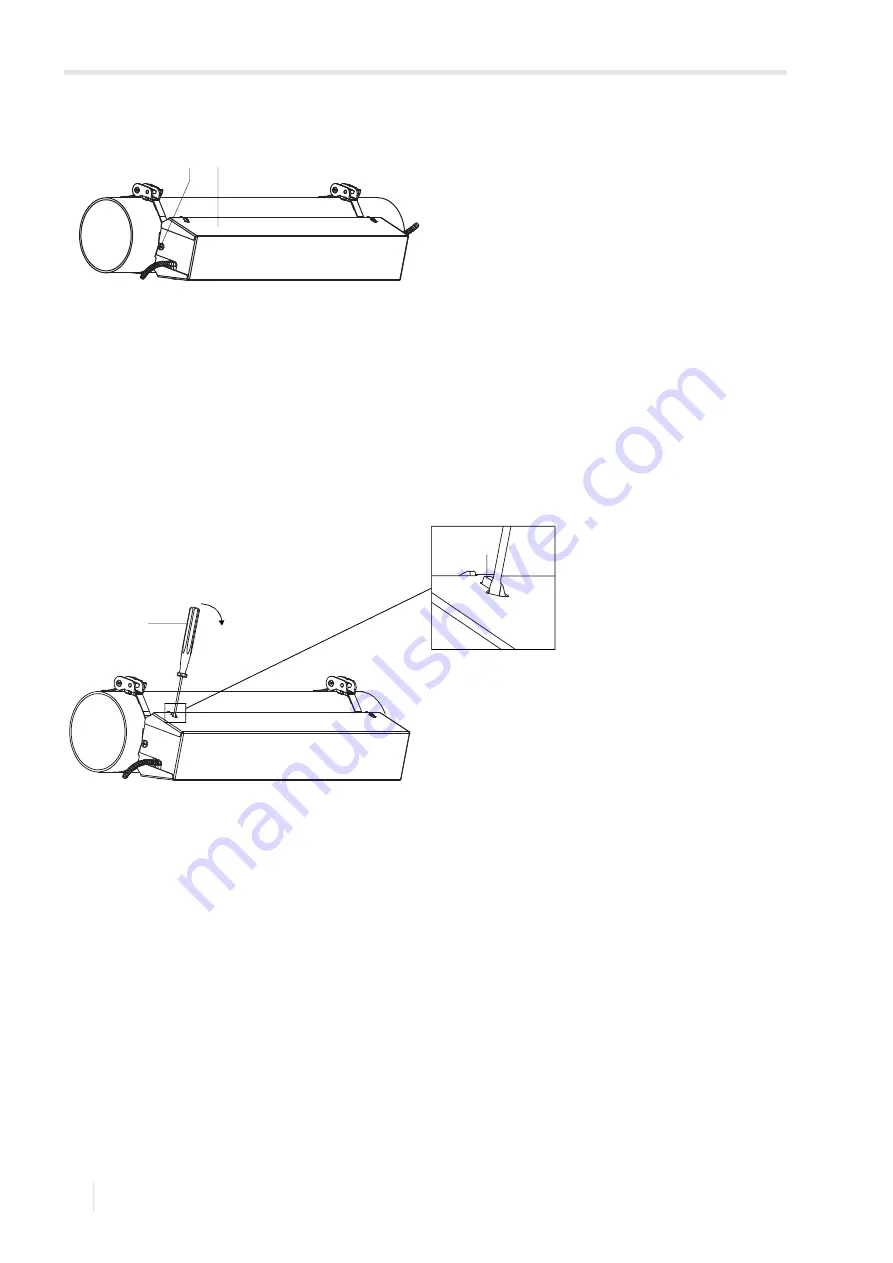
6 Mounting
6.2 Transducers
FLUXUS G801
2020-06-26, UMFLUXUS_G801V1-0EN
56
Remove the cover from the mounted transducer mounting fixture Variofix C as follows:
• Use a lever tool to remove the cover.
• Insert the lever tool in one of the 4 openings of the cover (see Fig. 6.51).
• Press the lever tool against the fixture.
• Bend the cover outwards and release it from the anchoring.
• Repeat the steps for the other 3 openings.
• Remove the cover from the rail.
Fig. 6.50: Variofix C with transducers on the pipe
1 – screw
2 – cover
Fig. 6.51: Removal of the cover
1 – lever tool
2 – fixture
1
2
2
1