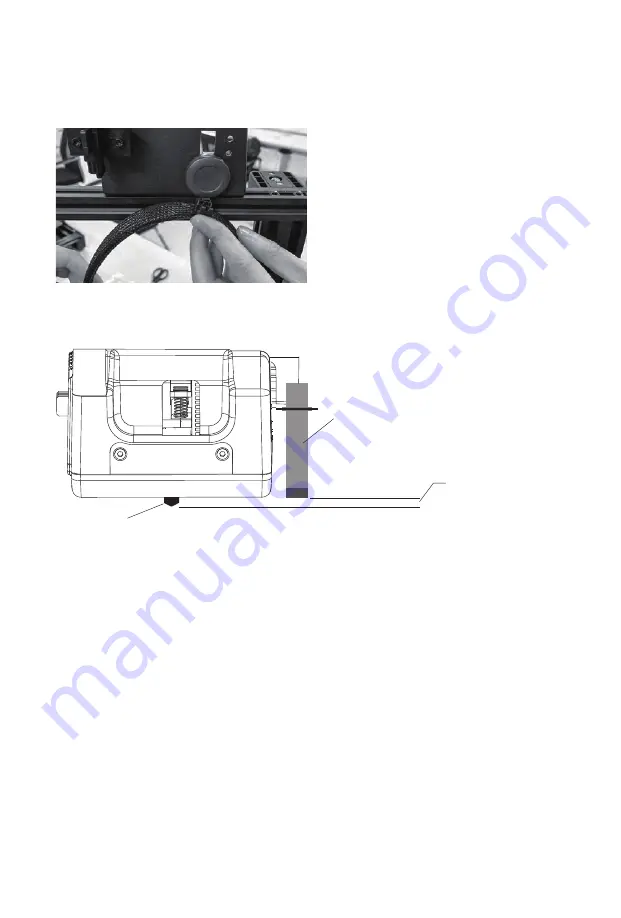
19
7. Clip sensor cable into pulley clip on the top of filament fixed seat for sensor cable is too long.
Sensor
Height difference
Nozzle
8. After installation completed, please compare the height between the nozzle and the bottom
of the sensor. The sensor should be 1-2 mm higher than the nozzle. You can adjust the sensor
height by adjusting nuts on the sensor.
Summary of Contents for THOR300T
Page 21: ...20 3 Z T Z T 5 M5 25 4 M4 6 5 M4 8 4 M4 5 8 4 1 300T 2 6...
Page 22: ...21 11 9 10 7 8 12...
Page 23: ...22 1 400T 500T 2 3 5 4 6...
Page 24: ...23 7 8 9 Z T Z T 11 M5 25 4 M4 6 5 M4 8 4 M4 5 8 10...
Page 27: ...26 1 2 T 3 T T 4 T T 5 T 6 T...
Page 28: ...27 7 L L 8 L 9 M5 25 4 10 M4 5 L 4 8 11 T T T...
Page 29: ...28 12 M4 8 T 4 13 T 14 15 M4 6 16...
Page 30: ...29 17 M4 6 18 19 Z Steeper Z Z 20 X Steeper X X X...
Page 31: ...30 21 Z 23 X Max X X X 24 25 26 22 Z Z T...
Page 32: ...31 2 x 120mm 3 X 4 X 6 5 1...
Page 33: ...32 7 Tools Home Yes Thor 4 Print Preheat Tools...
Page 34: ...33 8 A4 A4 Thro...
Page 35: ...34 3 Filament 4 load 1 2 Tools 5 Extruder 100 Cancel Print Preheat Tools...
Page 38: ...37 1 2 3 4 5 6...
Page 39: ...38 7 8 1 2 2mm...
Page 40: ......