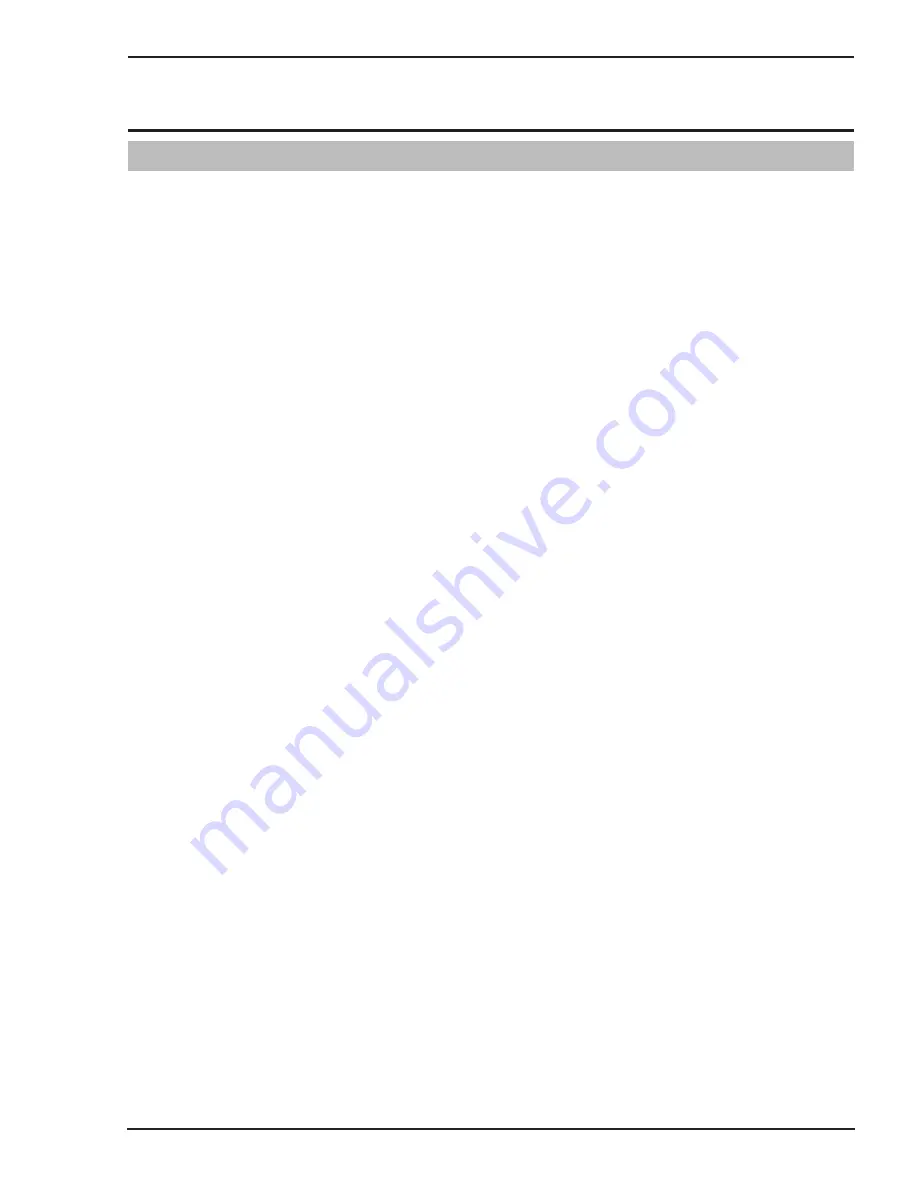
BASIC WELDING GUIDE
FIREPOWER TIG 200 AC/DC
Manual 0-5370
4-1
Basic Welding Guide
SECTION 4:
BASIC WELDING GUIDE
4.01 STICK (SMAW) BASIC WELDING TECHNIQUE
Size of Electrode
The electrode size is determined by the thickness of metals being joined and can also be governed by the type
of welding machine available. Small welding machines will only provide sufficient current (amperage) to run the
smaller size electrodes.
For thin sections, it is necessary to use smaller electrodes otherwise the arc may burn holes through the job. A
little practice will soon establish the most suitable electrode for a given application.
Storage of Electrodes
Always store electrodes in a dry place and in their original containers.
Electrode Polarity
Electrodes are generally connected to the ELECTRODE HOLDER with the Electrode Holder connected positive
polarity. The WORK LEAD is connected negative polarity and is connected to the work piece. If in doubt consult
the electrode data sheet or your nearest Accredited Firepower Distributor.
Effects of Stick Welding Various Materials
A. High Tensile and Alloy Steels
The two most prominent effects of welding these steels are the formation of a hardened zone in the weld area,
and, if suitable precautions are not taken, the occurrence in this zone of under-bead cracks. Hardened zone
and under-bead cracks in the weld area may be reduced by using the correct electrodes, preheating, using
higher current settings, using larger electrodes sizes, short runs for larger electrode deposits or tempering
in a furnace.
B. Manganese Steels
The effect on manganese steel of slow cooling from high temperatures is to embrittle it. For this reason it
is absolutely essential to keep manganese steel cool during welding by quenching after each weld or skip
welding to distribute the heat.
C. Cast Iron
Most types of cast iron, except white iron, are weldable. White iron, because of its extreme brittleness, generally
cracks when attempts are made to weld it. Trouble may also be experienced when welding white-heart malleable,
due to the porosity caused by gas held in this type of iron.
D. Copper and Alloys
The most important factor is the high rate of heat conductivity of copper, making pre-heating of heavy sections
necessary to give proper fusion of weld and base metal.
E. Types of Electrodes
Arc Welding electrodes are classified into a number of groups depending on their applications. There are a
great number of electrodes used for specialized industrial purposes which are not of particular interest for
everyday general work. These include some low hydrogen types for high tensile steel, cellulose types for
welding large diameter pipes, etc The range of electrodes dealt with in this publication will cover the vast
majority of applications likely to be encountered; are all easy to use.
Summary of Contents for TIG 200 AC/DC
Page 6: ...This Page Intentionally Blank...
Page 74: ...FIREPOWER TIG 200 AC DC APPENDIX A 2 Manual 0 5370 Appendix APPENDIX 2 200 AC DC SETUP GUIDE...
Page 75: ...APPENDIX FIREPOWER TIG 200 AC DC Manual 0 5370 A 3 Appendix A 12718...
Page 76: ...FIREPOWER TIG 200 AC DC APPENDIX A 4 Manual 0 5370 Appendix This Page Blank Intentionally...
Page 77: ...This Page Intentionally Blank...