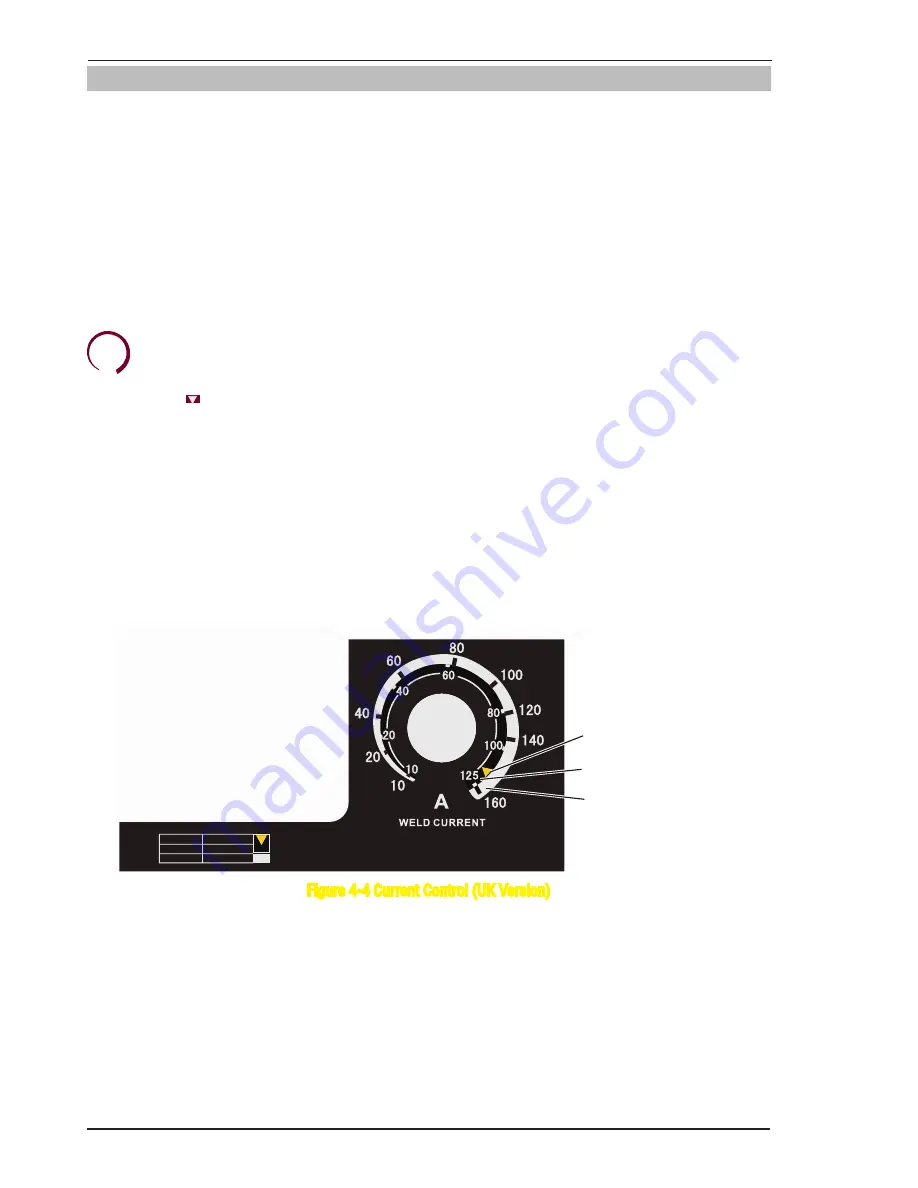
FIREPOWER 160 S
OPERATION
Operation 4-4
Manual 0-5371
4.04 Welding Current Control Explanation (UK Version)
32 Amp Outlet
The mains power 32 Amp circuit breaker or fuse should not trip at this Weld Current value when STICK welding.
The environmental conditions that may cause the mains power 32 Amp circuit breaker or fuse to trip are:
a) High ambient temperature
b) Worn parts in circuit breaker
c) Using an extension cable
d) Low line mains power voltage
Output Scale for 110V
The inside number scale identifies the available output weld current for STICK or LIFT TIG weld modes.
STICK Mode:
Identifies the STICK weld point for 32 Amp outlet.
Exceeding these points will cause nuisance tripping of the circuit breaker or fuse.
LIFT TIG Mode: A 32 Amp outlet is capable of supplying enough input power for all LIFT TIG output weld current
values.
Nuisance tripping should not occur on a 32 Amp outlet.
Output Scale for 230V
The outside number scale identifies the available output weld current for STICK or LIFT TIG weld modes.
Nuisance tripping should not occur on a 32A 230V outlet for both STICK & LIFT TIG Modes.
67,&.
FAULT
/,)7 7,*
32A OUTLET
STICK
TIG
230V
110V
TIG/STICK
32A OUTLET
16A OUTLET
PROCESS
Art#: A-09903_AB
32 Amp Outlet
Output Scale for 110V
Output Scale for 230V
Figure 4-4 Current Control (UK Version)
Summary of Contents for TIG 160S
Page 6: ...This Page Intentionally Blank ...
Page 18: ...FIREPOWER 160 S INTRODUCTION Introduction 2 2 Manual 0 5371 Notes ...
Page 30: ...FIREPOWER 160 S SAFETY AND INSTALLATION Safety and Installation 3 12 Manual 0 5371 Notes ...
Page 40: ...FIREPOWER 160 S THEORY OF OPERATION Theory of Operation 5 2 Manual 0 5371 Notes ...
Page 54: ...FIREPOWER 160 S TROUBLESHOOTING Troubleshooting 6 14 Manual 0 5371 Notes ...
Page 59: ...DISASSEMBLY PROCEDURE FIREPOWER 160 S Manual 0 5371 7 5 Disassembly Procedure 4 Art A 09866 ...
Page 66: ...FIREPOWER 160 S DISASSEMBLY PROCEDURE Disassembly Procedur 7 12 Manual 0 5371 Notes ...
Page 69: ...ASSEMBLY PROCEDURES FIREPOWER 160 S Manual 0 5371 8 3 Assembly Procedures 8 Art A 09883 ...
Page 74: ...FIREPOWER 160 S ASSEMBLY PROCEDURES Assembly Procedures 8 8 Manual 0 5371 Notes ...
Page 78: ...FIREPOWER 160 S REPLACEMENT PARTS Replacement Parts 9 4 Manual 0 5371 Notes ...
Page 80: ...FIREPOWER 160 S ACCESSORIES Accessories 10 2 Manual 0 5371 Notes ...
Page 83: ......