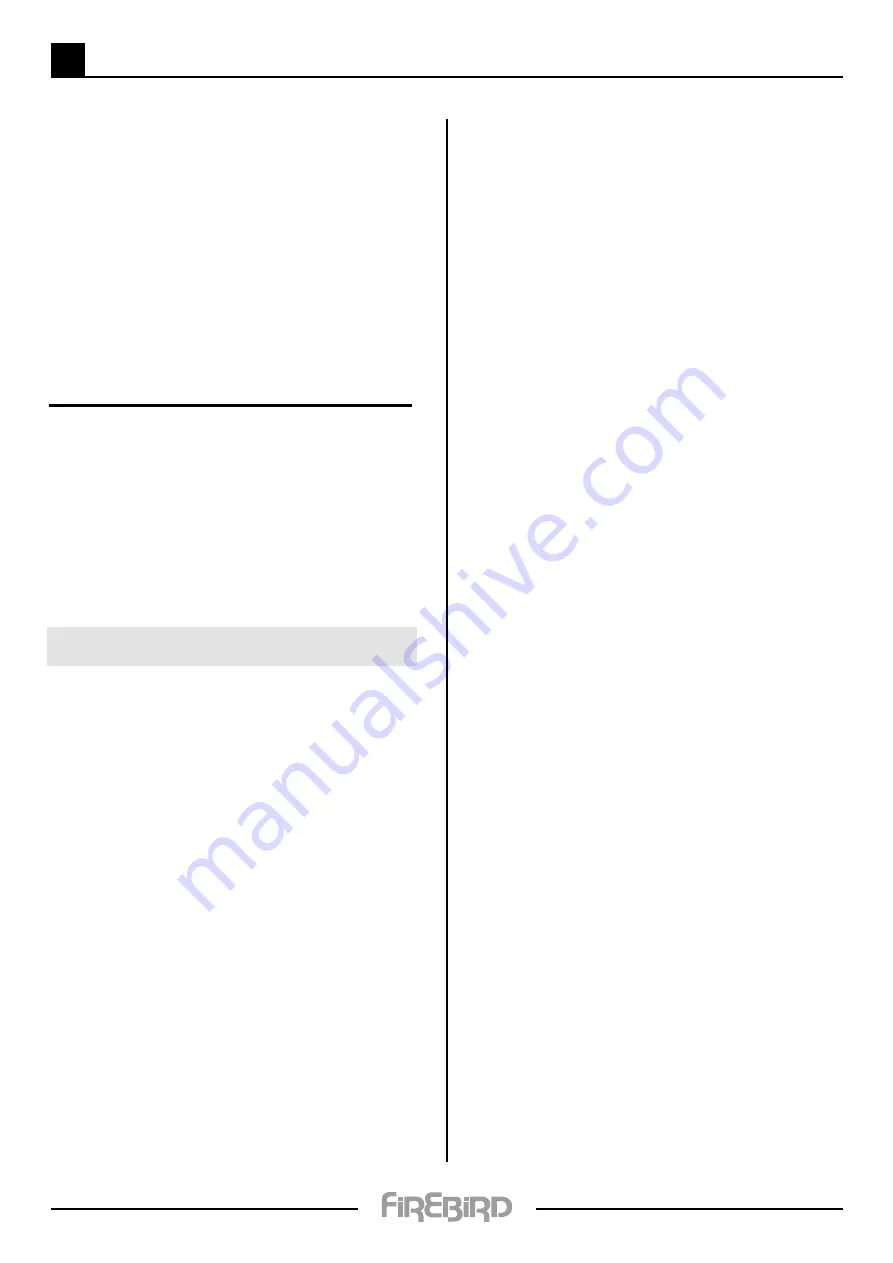
6
CoMMIssIonIng
oil supply:
u
The burner is set for Diesel 35 Second gas Oil
u
Check that there is a good quality filter on the line with
an isolating valve.
u
There should be a remote sensing fire valve.
u
If a deaerator is required, fit the bypass screw in the
diesel pump. Check that the second flexible diesel line
is approved by the manufacturer.
u
Verify that the diesel tank has been installed correctly
as per building standards.
Boiler check:
u
Baffles should be checked as they many have been
disturbed during transport.
u
Check that the condensate trap is fitted securely,
primed with water and piped out into a suitable drain.
It is easier to check the trap when the boiler door is
removed.
u
The boiler door should be refitted, complete with
graphite seal and then tightened.
Flue check:
u
The flue must be fitted correctly, with a fall back to the
boiler. Note: internal fall of 2.5˚ within the flue.
u
For concentric balanced flue:
- the cone supplied should be inserted in to the end
of the flue;
- the wall plate should be fitted with an opening
for air under the flue;
- check that the flue guard is fitted.
u
When installing a Systempac, the 90˚ bend should be
fitted pointing up.
Burner set-up:
u
Check that the nozzle is the right size for the type of
boiler and for the system heat demand.
u
Set the air to what is required for the nozzle size +.5 on
the dial - example: the factory setting for a Firebird C26
has a Danfoss 0.6 80˚ eS nozzle with a pump pressure
of 10.5 bar. Please refer to the burner manual for the air
setting.
u
Check all connections for possible leaks.
u
Turn on the oil supply and switch on power to the
boiler.
u
Set the thermostat at minimum.
u
Use a smoke gun to check clean combustion.
Flue gas analysis and fine tuning of burner:
u
ensure flue gas is over 50˚C when setting CO
2.
u
allow the boiler to run for a period of time before fine
tuning to the Firebird settings.
u
This fine tuning should be done with the boiler in the
condition it is going to be operating at, that is, if a
balanced flue is installed, the air hose is fixed on the
burner. In the case of a Slimline Heatpac, ensure that
the door is closed for a period of time before setting
the analyser on the system.
CoMMIssIonIng
u
It is the responsibility of the installer/end user to
ensure that the boiler is properly commissioned
when first used.
u
the boiler should be commissioned by a
competent, qualified engineer, preferably familiar
with Firebird products.
u
the commissioning card should be completed and
posted to Central Heating new Zealand within 28
days of installation and a copy should be retained
by the commissioning engineer.
u
the system should be checked thoroughly.
ProCedures
dIesel tank
The installation of the Diesel tank and supply line should
comply with all the instructions shown earlier in this
manual. Consult OFTeC Book 3.
If a single supply line is used, ensure that the bottom of
the tank is above the burner. a suction line system via a
deaerator should be used where the level of the diesel in
the tank may fall below the level of the oil burner pump.
Check and ensure correct grade fuel oil
has been supplied.
CHeCklIst For InstallIng and
CoMMIssIonIng a FIreBIrd BoIler
Pre-installation check:
u
Is the following documentation included with the
boiler, installation manual, burner book?
u
Is the base on which the boiler is to be installed solid?
u
allow sufficient room for future servicing of the boiler.
where does the flue terminate:
u
Make sure there is no window, door or fence within 1
metre of the flue-terminal.
u
If the flue terminates in a corner or into an allyway,
re- circulation of the combustion gases in the air intake
could occur. a plume dispersal may be required or
an alternative flue arrangement might be available.
Contact the Central Heating New Zealand technical
department.
u
The appropriate class 1 flue must be used with a
conventional flue installation. Contact Central Heating
New Zealand if unsure.
Power supply:
u
Is a timed and permanent power supply available, via a
fused spur with a 5amp fuse.
32