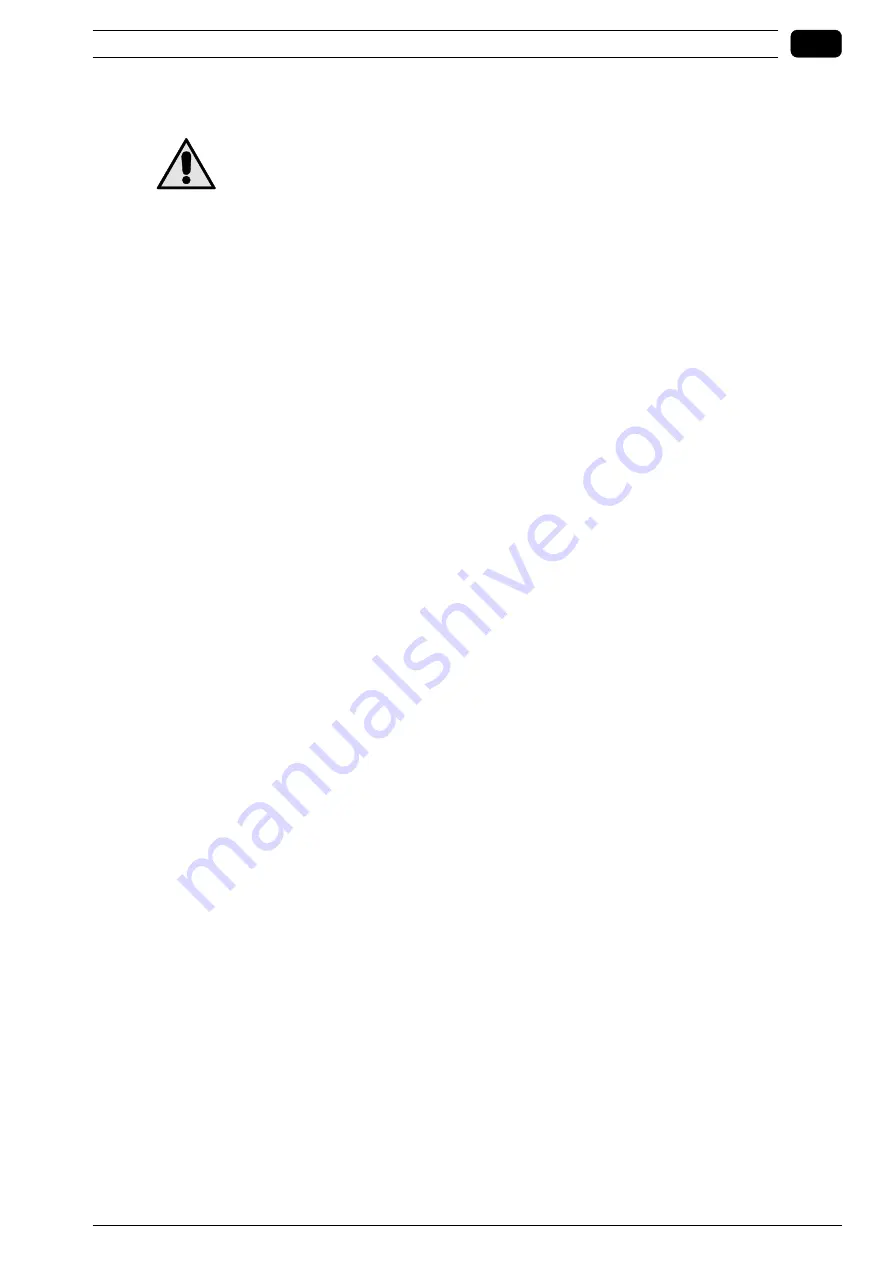
19/68
GB
USING THE COMPRESSOR
5
5
Using the compressor
In order to use the compressor in complete safety read the safety standards given
in section 1.3. before reading this section.
5.1
Preparing to use the compressor
5.1.1
Operational principle
The air taken-in by the filter passes through a valve that controls its flow rate to the screw where, mixing
with the oil, it is compressed.
The air/oil mix produced by compression reaches a tank where the initial separation by gravity is achieved;
as the oil is heavier, it settles on the bottom, it is then cooled and sent through a heat exchanger, filtered and
injected into the screw again.
The oil is required to reduce the heat produced by compression, to lubricate the bearings and to maintain
the coupling of the screw lobes. The air is sent through an oil separator filter to be additionally purified from
residue oil particles. It is cooled by means of another heat exchanger and is finally outlet to be used at low
temperature and with acceptable oil residues (
≤
1p.p.m.). A safety system controls the crucial points of the
machine and points out any abnormal conditions. The temperature of the air/oil mix at the screw outlet is
controlled by a thermostatic probe, which stops the compressor if the temperature is too high (105°C).
The electric motor is equipped with a trip switch that immediately stops the compressor in the case of an
over current caused by a mechanical or electric fault.
5.1.2
Compressor operation with inverter versions “SD” (speed driven)
Principle of the speed of the inverter controlled compressor
The mains pressure is monitored by a pressure transducer and transmitted to the frequency converter by
means of an analogue input. The rated value set is transmitted to the inverter, which compares the values
and, based on the requirements, adjusts the speed of the motor and consequently the output of
compressed air, thus adapting to the pressure requested (0,5 bar less than that set).
Speed of the motor
The operating frequency of the motor may vary from 15Hz (approx.) to 65Hz (approx.), depending on the
models there may be some differences.
Whatever the case, you are recommended never to modify the speed values set by the manufacturer. A
slower or faster speed set negligently could irreparably damage the motor.
The motor is designed to run continuously in the frequency range set during testing.
The motor has a power “plus” to compensate for filter clogging or possible pressure leaks.
Adjustment
Min. P.:
Shut-down pressure
Max. P.:
Transfer pressure to idle running
Inverter controlled compressors entail the following three phases:
-
Operation with speed modulation following the pressure set
-
Idle operation
-
stand-by.
The motor varies the speed by modifying the speed of the compressor unit, therefore modifying the air
output.
Summary of Contents for AIRBLOK 40
Page 44: ...44 68 GB 7 DRAWINGS AND DIAGRAMS ...
Page 45: ...45 68 GB DRAWINGS AND DIAGRAMS 7 ...
Page 46: ...1 4 CF75G AIRBLOK40 SD ...
Page 49: ...2 4 CF75G AIRBLOK40 SD ...
Page 51: ...3 4 CF75G AIRBLOK40 SD ...
Page 53: ...4 4 CF75G AIRBLOK40 SD ...
Page 55: ...1 4 CF90LD1 AIRBLOK50 SD ...
Page 58: ...2 4 CF90LD1 AIRBLOK50 SD ...
Page 60: ...3 4 CF90LD1 AIRBLOK50 SD ...
Page 62: ...4 4 CF90LD1 AIRBLOK50 SD ...
Page 66: ...46 68 GB 7 DRAWINGS AND DIAGRAMS ...
Page 67: ...Date Job description Hours of use Operator ssignature ...