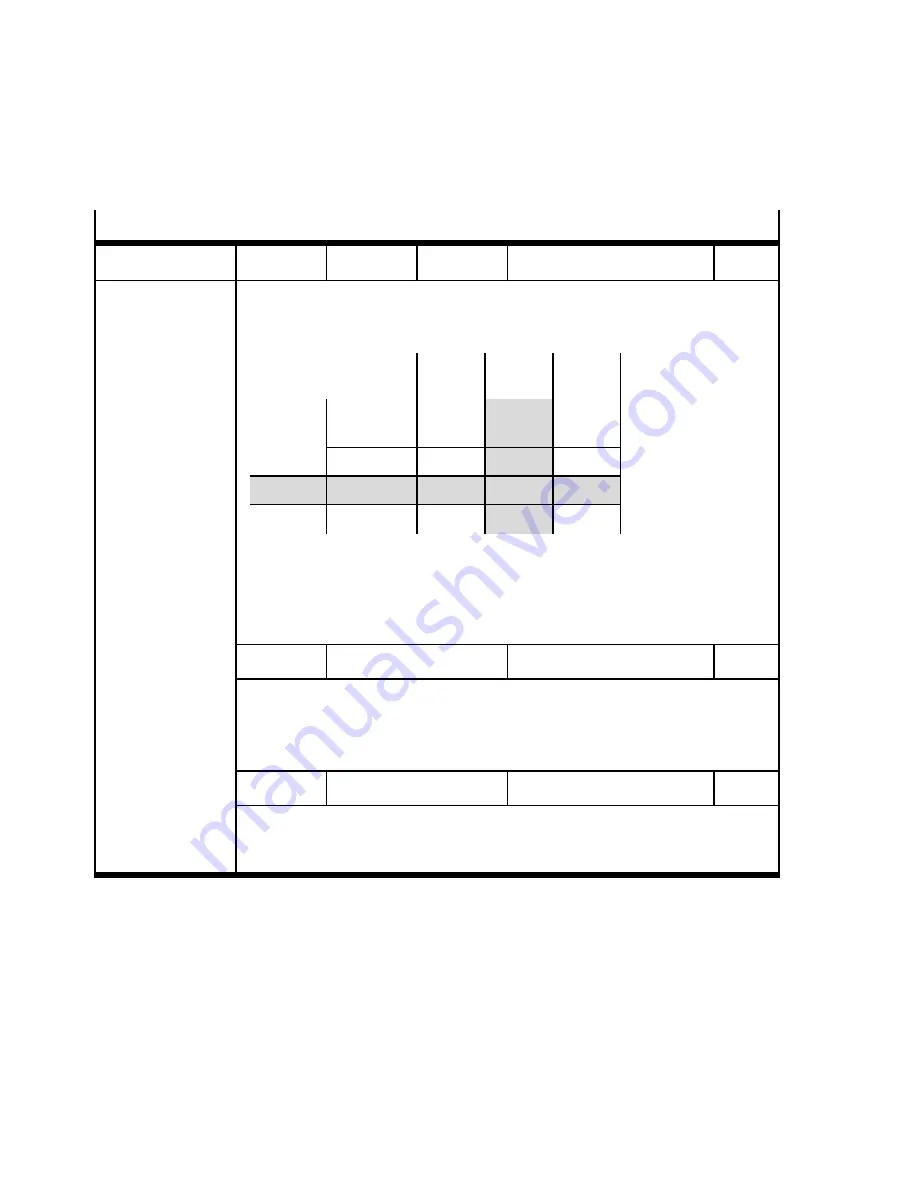
B. Supplementary information
B-20
Festo P.BE-MTR-DCI-IO-EN en 1209d
Record_Table_Element
CI access
20E0h
01h...03h
Struct
uint16, int32
rw
Description
Editing the entries in the position table:
1. Selecting the line (= position number) with Object 2032
2. Selection of the column under subindex 20E0: 01...03
20E0/01 20E0/02
V
20E0/03
Record
number
Pos. set
mode
Target
position
Profile
velocity
02
2032h
}
03
<1>
<...>
...
The values are only saved in the position table with this command; no move-
ment is made.
With Object 20E0, access is made partly to the same parameter as with the
corresponding Objects 607A, 6081.
Different data types are converted accordingly when they are read and written.
Positioning Mode 20E0h
01h
uint16
rw
Positioning mode
Values:
0 (0x0000):
absolute positioning (default)
1 (0x0001):
relative positioning
Target Position 20E0h
02h
int32
rw
Target position in increments (compare target position, Object 607A).
Value range: -2
31
...+(2
31
-1) (0x80000000...0x7FFFFFFF)
Default: 0
Summary of Contents for MTR-DCI-...IO Series
Page 1: ...Description MTR DCI IO Description 539616 en 1209d 763197 Motor unit MTR DCI ...
Page 4: ...Contents and general instructions II Festo P BE MTR DCI IO EN en 1209d ...
Page 8: ...Contents and general instructions VI Festo P BE MTR DCI IO EN en 1209d ...
Page 19: ...System summary 1 1 Festo P BE MTR DCI IO EN en 1209d Chapter 1 System summary ...
Page 35: ...Mounting 2 1 Festo P BE MTR DCI IO EN en 1209d Chapter 2 Mounting ...
Page 43: ...Installation 3 1 Festo P BE MTR DCI IO EN en 1209d Chapter 3 Installation ...
Page 58: ...3 Installation 3 16 Festo P BE MTR DCI IO EN en 1209d ...
Page 79: ...Commissioning 5 1 Festo P BE MTR DCI IO EN en 1209d Chapter 5 Commissioning ...
Page 120: ...6 Operating maintenance and diagnosis 6 12 Festo P BE MTR DCI IO EN en 1209d ...
Page 121: ...Technical appendix A 1 Festo P BE MTR DCI IO EN en 1209d Appendix A Technical appendix ...
Page 175: ...Index C 1 Festo P BE MTR DCI IO EN en 1209d Appendix C Index ...
Page 176: ...C Index C 2 Festo P BE MTR DCI IO EN en 1209d Contents C Index C 1 ...