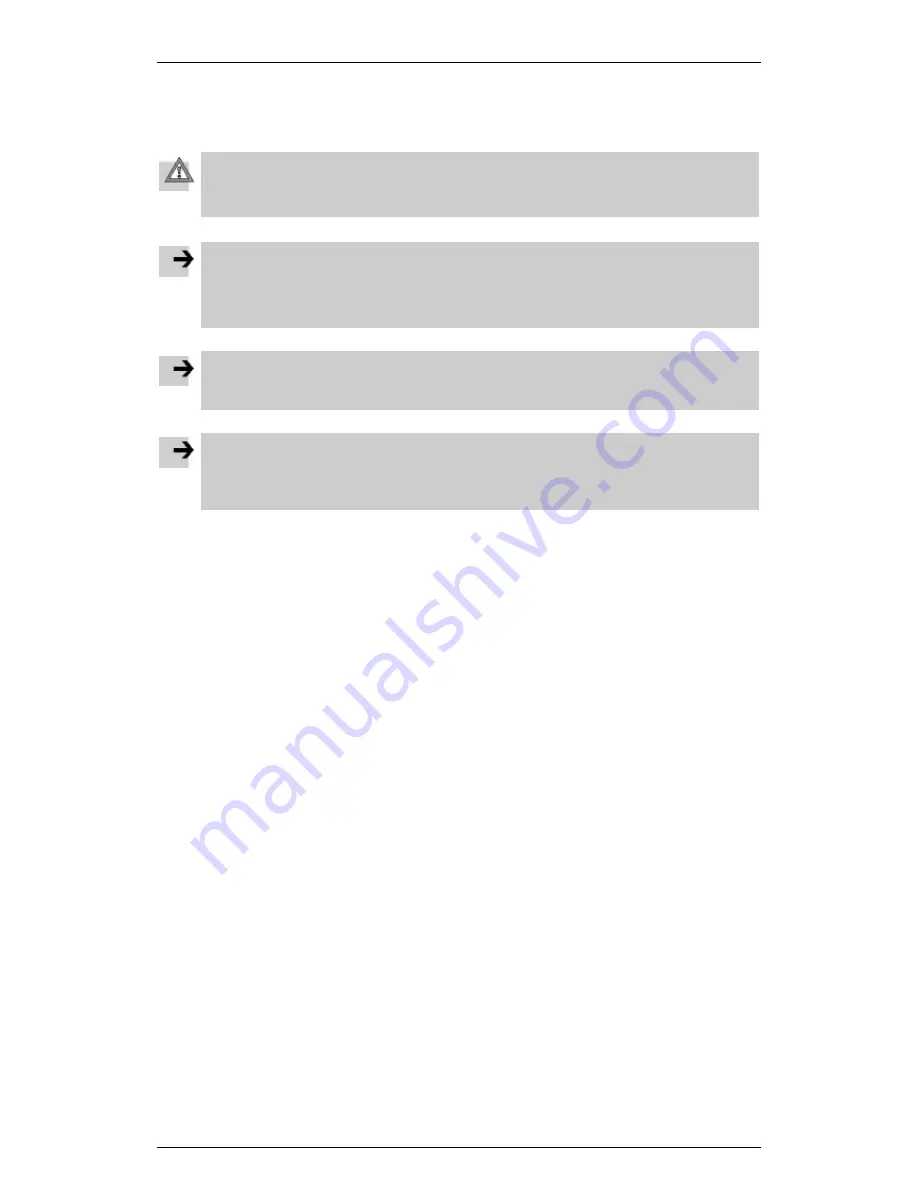
Festo control block CPX-CEC
3
Installation
3.1
General information
Caution
Risk of injury due to electric shock.
•
Always switch off the power supply before mounting or removing CPX modules.
Note
The controller CPX-CEC-...-V3 contains electrostatically sensitive components.
•
Therefore do not touch any contacts.
•
Observe the handling specifications for electrostatically sensitive devices.
Note
The controller CPX-CEC-...-V3 only supports single-channel switch-off. All inputs and outputs are
de-energised when the power supply is switched off.
Note
Check your EMERGENCY STOP circuit in order to ascertain the measures necessary for
switching your machine/system into a safe state in the event of an EMERGENCY STOP
(e.g. shutting off energy sources; load voltage supply, compressed air, etc.).
Information on mounting the CPX terminal can be found in the CPX system manual P.BE-CPX-SYS-.... .
10
Summary of Contents for CPX-CEC-C1-V3
Page 2: ......
Page 6: ......
Page 54: ...Festo control block CPX CEC Figure Settings on channel 1 Figure Settings on channel 2 48...