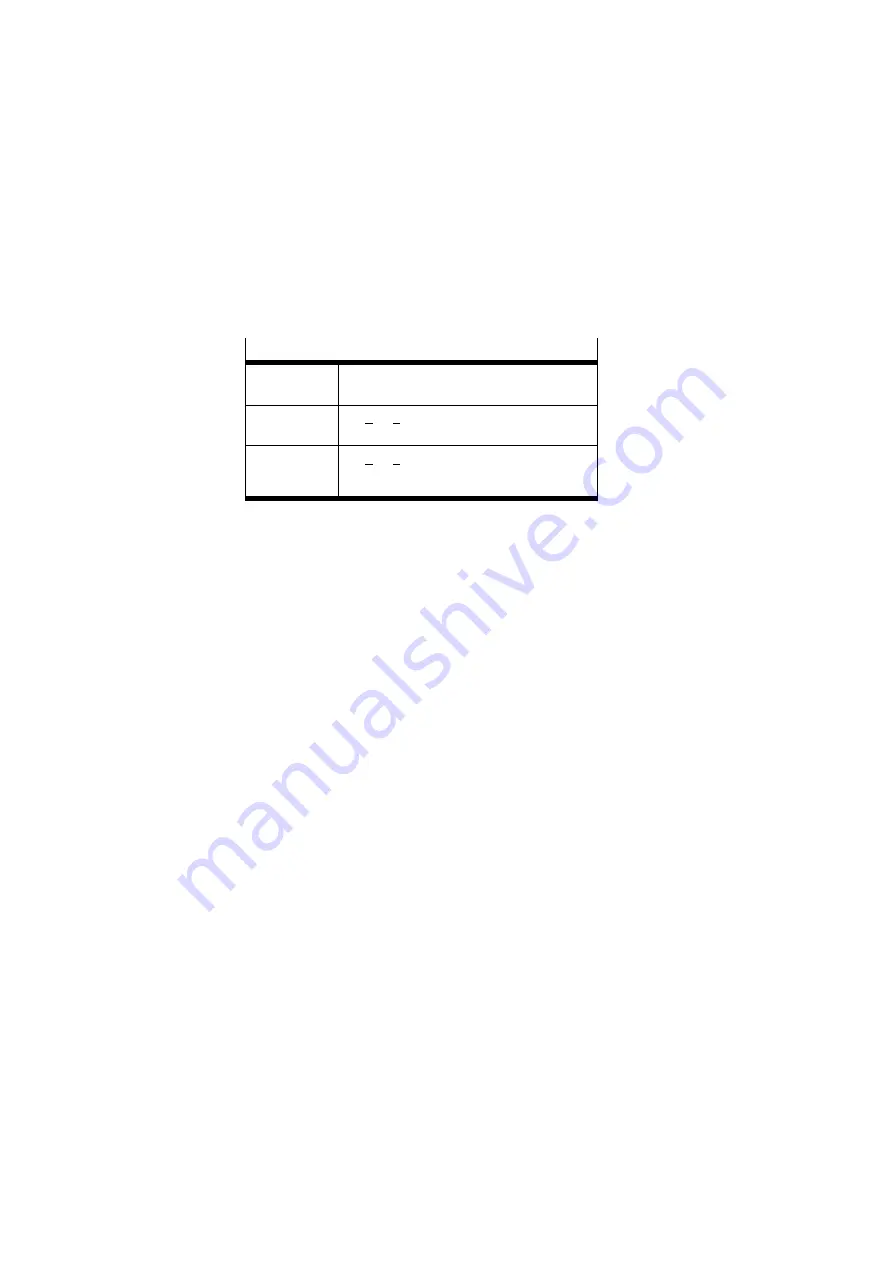
2. Commissioning
2-6
Festo P.BE-CP-CO2-EN en 0107NH
2.2
Commissioning on a CANopen master
This chapter describes the configuration and addressing of a
CPV valve terminal on a CANopen interface or CANopen
master.
The following standards are observed:
Standards
DS 201
DS 207
CAN Application Layer CAL
DS 301, V4.01
The Draft Standard 301 is based on the CAL
based communication profile.
DS 401, V2.0
The Draft Standard 401 defines the device
profiles for input and output modules within
CANopen.
In order to understand this chapter, you should be familiar
with CANopen and the specifications DS 301 and DS 401.
Summary of Contents for CP-A08...-M12 Series
Page 2: ......
Page 4: ...Contents and general instructions II Festo P BE CP CO2 EN en 0107NH ...
Page 8: ...Contents and general instructions VI Festo P BE CP CO2 EN en 0107NH ...
Page 14: ...Contents and general instructions XII Festo P BE CP CO2 EN en 0107NH ...
Page 15: ...Installation 1 1 Festo P BE CP CO2 EN en 0107NH Chapter 1 ...
Page 55: ...Commissioning 2 1 Festo P BE CP CO2 EN en 0107NH Chapter 2 ...
Page 83: ...Diagnosis 3 1 Festo P BE CP CO2 EN en 0107NH Chapter 3 ...
Page 100: ...3 Diagnosis 3 18 Festo P BE CP CO2 EN en 0107NH ...
Page 101: ...Technical data and accessories A 1 Festo P BE CP CO2 EN en 0107NH Appendix A ...
Page 106: ...A Technical data and accessories A 6 Festo P BE CP CO2 EN en 0107NH ...
Page 110: ...A Technical data and accessories A 10 Festo P BE CP CO2 EN en 0107NH ...
Page 111: ...Examples B 1 Festo P BE CP CO2 EN en 0107NH Appendix B ...
Page 118: ...B Examples B 8 Festo P BE CP CO2 EN en 0107NH ...
Page 119: ...Index C 1 Festo P BE CP CO2 EN en 0107NH Appendix C ...
Page 120: ...C Index C 2 Festo P BE CP CO2 EN en 0107NH Contents C Index C 1 ...