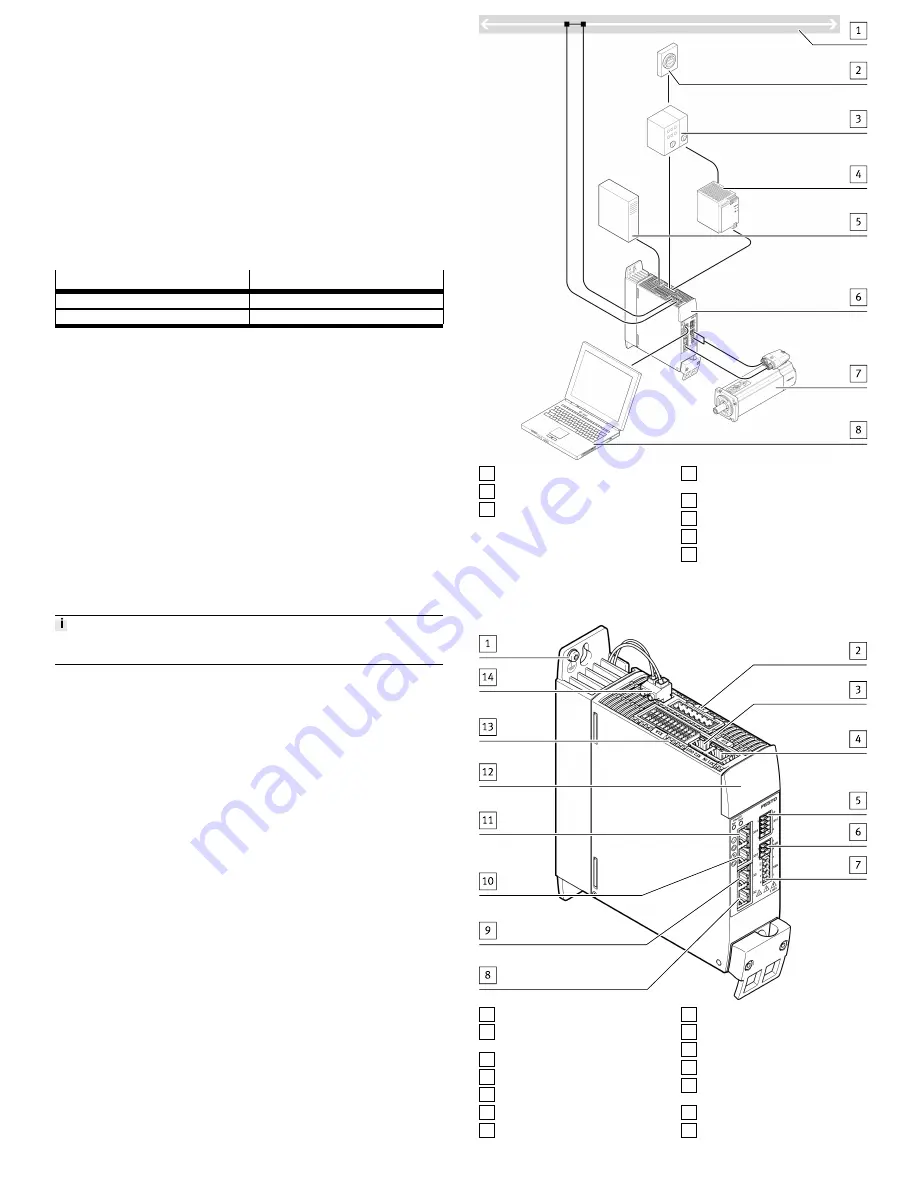
During installation and operation of this product, comply with all safety require
ments, statutes, codes, rules and standards relevant for the product, such as the
National Electrical Code (USA), Canadian Electrical Code (Canada) and regulations
of the US federal agency OSHA. When selecting the circuit breaker, comply with
the maximum permissible electrical protection for UL.
3
Additional information
–
Accessories
è
www.festo.com/catalogue.
–
Spare parts
è
www.festo.com/spareparts.
–
All available documents for the product and current versions of the firmware
and commissioning software
è
www.festo.com/sp.
4
Service
Contact your regional Festo contact person if you have technical questions
è
www.festo.com.
5
Product overview
5.1
Scope of delivery
Component
Number
Servo drive CMMTAS...
1
Instruction manual CMMTAS...
1
Tab. 6 Scope of delivery
5.2
System structure
The servo drive CMMTAS is a 1axis servo drive. Depending on the product vari
ant, the following components, which are necessary for standard applications, are
integrated into the device or into the cooling profile of the device:
–
Mains filter (guarantees immunity to interference and limits conducted emit
ted interference)
–
Electronics for intermediate circuit voltage conditioning
–
Output stage (for motor control)
–
Braking resistor (integrated into the cooling element)
–
Brake chopper (switches the braking resistor in the intermediate circuit, if and
when required)
–
Temperature sensors (for monitoring the temperature of the power module
and of the air in the device)
–
Fan in cooling profile (depending on product variant)
The servo drive features a Realtime Ethernet interface for process control. Vari
ous bus protocols are supported depending on the product design (EtherCAT, Eth
erNet/IP or PROFINET).
The device can be parameterised via a PC using either the Realtime Ethernet
interface or the separate standard Ethernet interface.
Festo recommends use of servo motors, electromechanical drives, lines and
accessories from the Festo accessory programme.
1 Bus/network
2 Main switch
3 Circuit breaker/fuses and allcur
rentsensitive RCD (residualcur
rentoperated protective device)
(optional)
4 Power supply unit for logic voltage
supply 24 V DC (PELV)
5 External braking resistor (optional)
6 Servo drive CMMTAS
7 Servo motor (here EMMEAS)
8 PC with Ethernet connection for
parameterisation
Fig. 3 System structure (example)
5.2.1
Overview of connection technology
1 PE connection, housing
2 [X9A] Mains voltage, intermediate
circuit voltage and logic voltage
3 [XF2 OUT] RTE interface port 2
4 [XF1 IN] RTE interface port 1
5 [X1C] Inputs/outputs for the axis
6 [X6B] Motor auxiliary connection
7 [X6A] Motor phase connection
8 [X2] Encoder connection 1
9 [X3] Encoder connection 2
10 [X10] Device synchronisation
11 [X18] Standard Ethernet
12 [X5] Connection for operating unit
(behind the blind plate)
13 [X1A] I/O interface
14 [X9B] Connection for braking res
istor
Fig. 4 Connections of the CMMTAS...3A