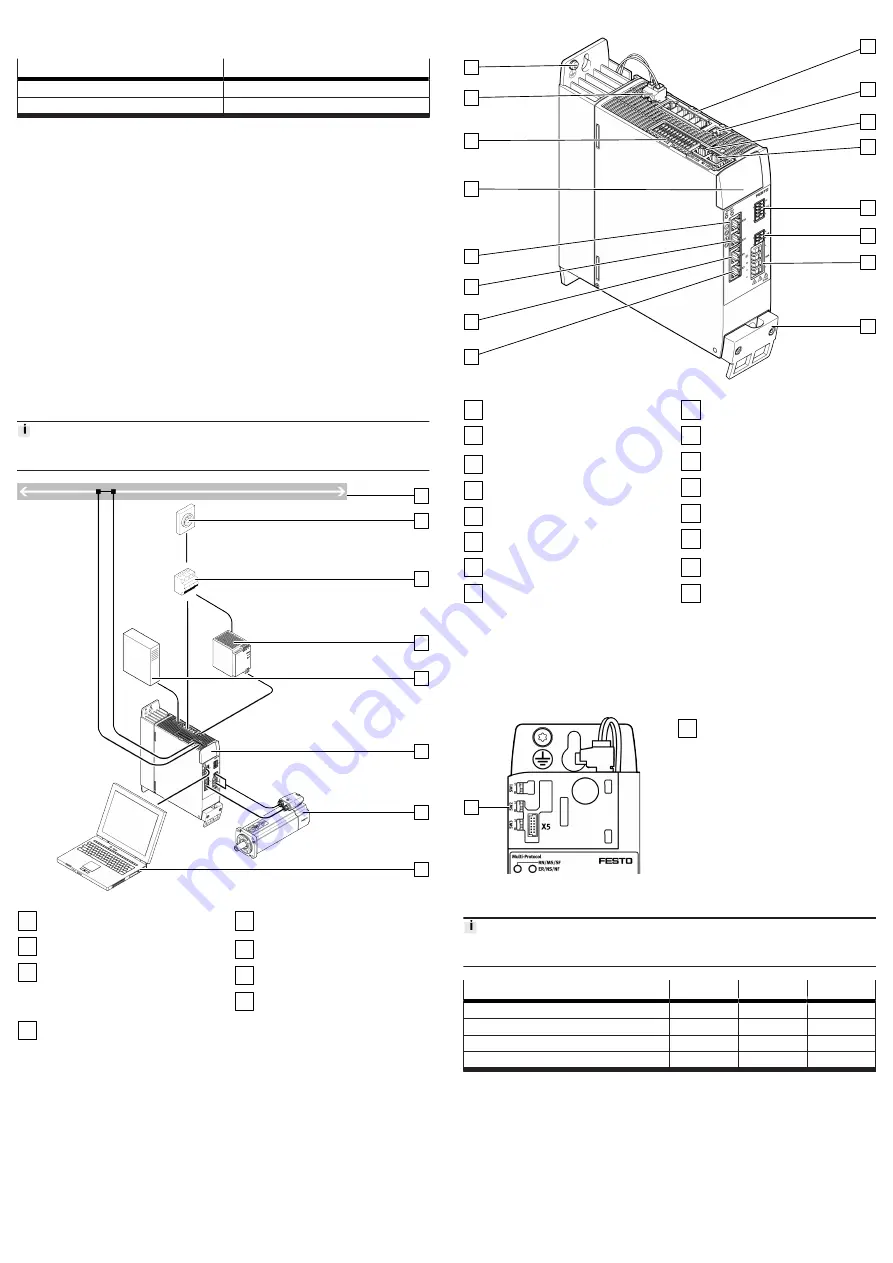
4
Product overview
4.1
Scope of delivery
Component
Number
Servo drive CMMT-AS-...
1
Operating instructions CMMT-AS-...
1
Tab. 6: Scope of delivery
4.2
System structure
The servo drive CMMT-AS is a 1-axis servo drive. Depending on the product
variant, the following components, which are necessary for standard applications,
are integrated into the device or into the cooling profile of the device:
–
Mains filter (guarantees immunity to interference and limits conducted emis-
sions)
–
Electronics for DC link voltage conditioning
–
Power stage (for motor control)
–
Braking resistor (integrated into the cooling element)
–
Brake chopper (switches the braking resistor in the DC link circuit, if and when
required)
–
Temperature sensors (for monitoring the temperature of the power module and
of the air in the device)
–
Fan in the cooling profile (depending on product variant)
The servo drive features a real-time Ethernet interface for process control. Var-
ious bus protocols are supported depending on the product design (EtherCAT,
EtherNet/IP or PROFINET).
The device can be parameterised via a PC using either the real-time Ethernet
interface or the separate standard Ethernet interface.
Festo recommends use of servo motors, electromechanical drives, lines and
accessories from the Festo accessory programme.
1
2
3
4
5
6
7
8
Fig. 1: System structure (example)
1
Bus/network
2
Main switch
3
Automatic circuit breaker/fuses
and all-current-sensitive RCD
(residual current device)
(optional)
4
Fixed power supply for logic
voltage supply 24 V DC (PELV)
5
External braking resistor
(optional)
6
Servo drive CMMT-AS
7
Servo motor (here EMME-AS)
8
PC with Ethernet connection for
parameterisation
4.2.1
Overview of connection technology
1
2
3
4
5
6
7
8
9
10
11
12
13
14
15
16
Fig. 2: Connections of the CMMT-AS-C2-11A-P3 (example)
1
PE connection, housing
2
[X9A] Mains and DC link circuit
connection
3
[X9C] Logic voltage
4
[XF2 OUT] RTE interface port 2
5
[XF1 IN] RTE interface port 1
6
[X1C] inputs/outputs for the axis
7
[X6B] motor auxiliary connection
8
[X6A] motor phase connection
9
Shield clamp of motor cable
10
[X2] encoder connection 1
11
[X3] encoder connection 2
12
[X10] device synchronisation
13
[X18] standard Ethernet
14
[X5] connection for operator unit
(behind the blind plate)
15
[X1A] I/O interface
16
[X9B] connection for braking
resistor
4.3
Set bus protocol
The CMMT-AS-...-MP product variant supports several bus protocols.
The following options are available for setting the protocol:
–
automatic detection by the CMMT-AS-...-MP
–
Configuration in the CMMT-AS plug-in
–
direct specification via SW1 to SW3
1
Fig. 3: Switches SW1, SW2, SW3 with
the CMMT-AS-...-MP
1
Switches SW1, SW2, SW3
Protocols supported by the firmware version used
è
Manual/online help plug-in,
software, function, fieldbus, device profile.
Protocol
Size 3
Size 2
Size 1
Auto (detection or parameterisation)
0
0
0
PROFINET
0
0
1
EtherCAT
0
1
0
EtherNet/IP
0
1
1
Tab. 7: Switch setting bus protocol
The switches can be adjusted with a small slotted head screwdriver.
The switch position is evaluated once when the device is started.
4.4
Safety sub-functions
4.4.1
Function and application
The servo drive CMMT-AS-...-S1 has the following safety-related performance fea-
tures:
–
Safe torque off (STO)
–
Safe brake control (SBC)