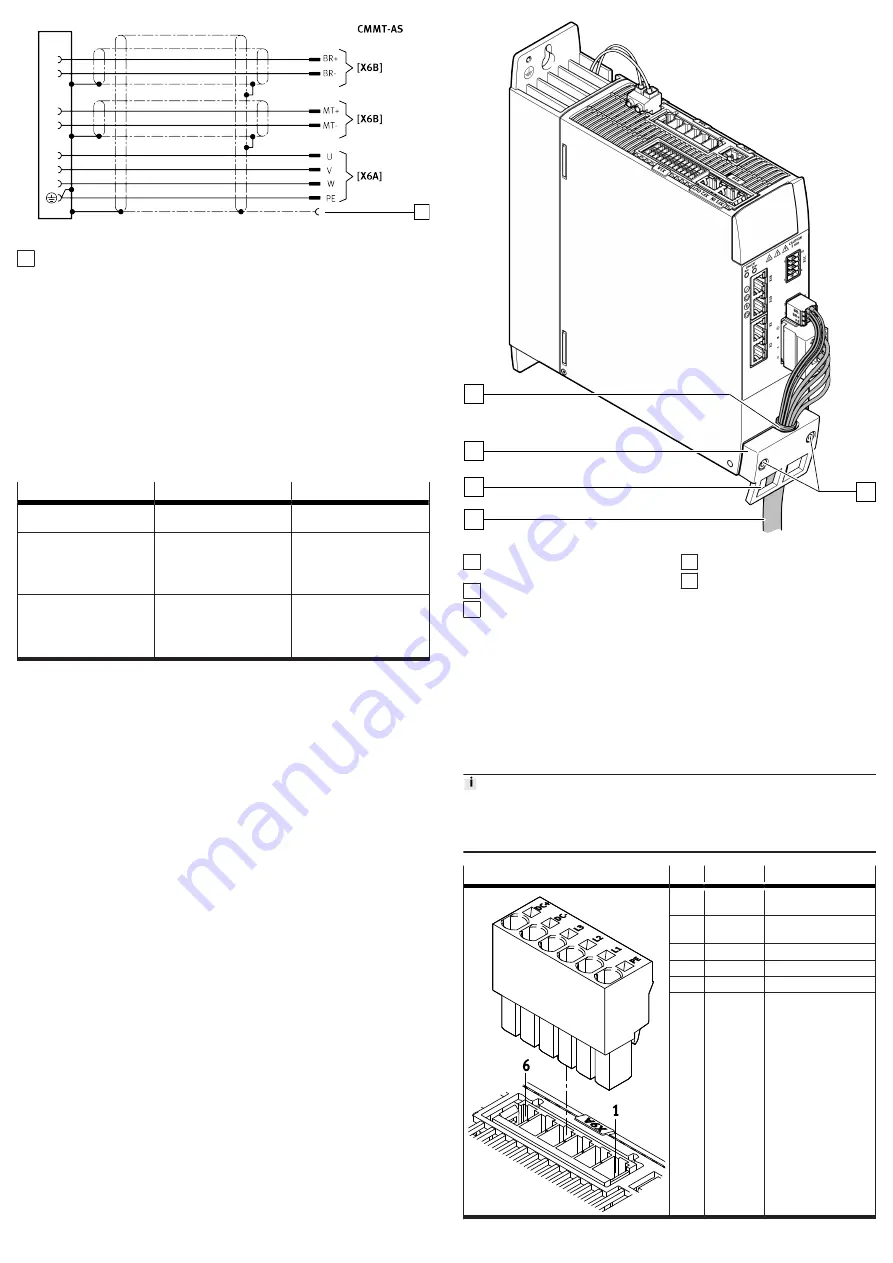
1
Fig. 10: Shared shield support of all cable shields (example)
1 Shield sleeve
Option 2: the outside shield of the motor cable is connected separately over a
wide surface area below the shield clamp on the front of the CMMT-AS. The inside
shields are connected separately to the designated FE pin of the connection [X6B].
•
Make unshielded cable ends as short as possible.
Mounting the shield clamp
The lower section on the front of the housing is used as a shield support surface.
The shield support surface, together with the shield clamp, allows the motor cable
shield to be connected over a wide surface area
1. Using the shield clamp, press the motor cable shield or the conductive shield
end sleeve of the motor cable onto the shield support surface of the housing.
2. Using a size T20 TORX screwdriver, tighten the retaining screws (2x) of the
shield clamp. Pay attention to the clamping range and observe the tightening
torque specified below.
Characteristic
Value
Comments
Clamping range
11 mm … 15 mm
Diameter of the stripped cable
or shield sleeve
Tightening torque for the
retaining screws in the case of
block mounting
1.8 Nm ± 15%
In the case of block mounting,
the shield clamp makes full
contact with the base of
the housing (cable diameter
11 mm)
Minimum tightening torque
with larger cable diameter
(
>
11 mm … 15 mm)
0.5 Nm ± 15%
With a higher tightening
torque, make sure the con-
necting cable does not get
crushed in the clamping area
due to excessive pressure.
Tab. 37: Tightening torque and clamping range CMMT-AS-...-C2/C3/C5-11A-P3
1
2
3
4
5
Fig. 11: Shield clamp of the motor cable
1 Retaining screws of the shield
clamp
2 Motor cable
3 Cut-out for mounting cable
binders (2x)
4 Shield clamp
5 Motor cable shield connected over
a large surface area below the
shield clamp
Motor cable shield support on the motor side
Detailed information on the motor-side connection with motor cables from Festo
è
Assembly instructions for the motor cable
•
Connect all shields to the PE over a wide surface area on the motor side,
e.g. via the shield connection provided on the motor connector or the shield
support surface in the motor junction box.
7.10
Power and logic voltage supply
7.10.1
[X9A], power supply and DC link circuit connection
The connections for the power voltage supply and the DC link circuit are not
protected against wiring errors. The reversal of the connections results in a device
defect during switch-on.
With cross-wiring, observe the polarity of the DC link connection on all devices.
[X9A]
Pin
Function
Description
6
DC+
DC link circuit positive
potential
5
DC-
DC link circuit negative
potential
4
L3
Mains supply phase L3
3
L2
Mains supply phase L2
2
L1
Mains supply phase L1
1
PE
Protective earthing
Tab. 38: Power supply and DC link circuit