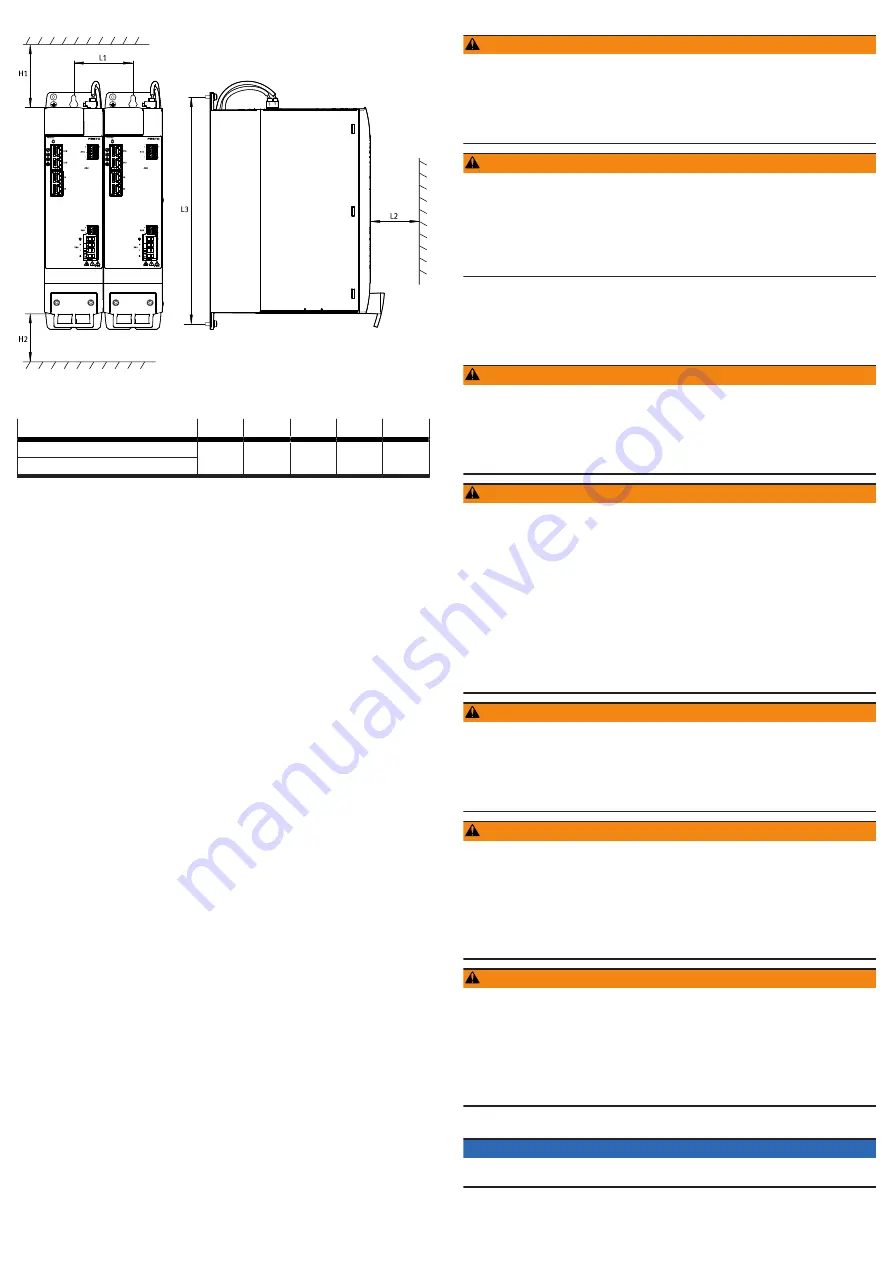
Mounting distances for CMMT-AS-C7/C12-11A-P3...
Fig. 4: Mounting distances and installation clearance for CMMT-AS-C7/
C12-...-11A-P3 (3-phase)
Servo drive
H1
H2
1)
L1
L2
L3
CMMT-AS-C7-11A-P3...
[mm]
100
70
78
70
300
CMMT-AS-C12-11A-P3...
[mm]
1) An installation clearance of 150 mm is recommended for compliance with clearance H2 and for optimum
routing of the motor and encoder cables on the underside of the housing!
Tab. 11: Mounting distances and installation clearance for CMMT-AS-C7/C12-11A-
P3...
This means that a minimum lateral distance of approx. 3 mm (78 mm - 75 mm)
must be observed in relation to neighbouring CMMT-AS devices.
For adjacent third-party devices, Festo recommends a distance of at least 10 mm
(surface temperature of third-party device max. 40°C). The double mating plug
for cross-wiring of the connection [X9A] protrudes by approx. 6
…
7 mm over the
right side of the device. However, this does not create an obstacle for arraying
additional CMMT-AS.
6.2
Installation
Assembly instructions
–
Use a control cabinet with degree of protection IP54 or higher.
–
Always install device vertically in the control cabinet on a closed surface (mains
supply lines [X9A] point upwards).
–
Screw device flat to a sufficiently stable mounting surface so that good
heat transfer from the cooling element to the mounting surface is ensured
(e.g. screw to the rear wall of the control cabinet).
–
Maintain minimum distances and installation clearance to guarantee sufficient
air flow. The ambient air in the control cabinet must be able to flow through the
device from bottom to top without hindrance.
–
Take into account the required clearance for the wiring (connecting cables of
the device must be routed from above and from the front).
–
Do not mount any temperature-sensitive components near the device. The
device can become very hot during operation (switch-off temperature of the
temperature monitoring function
è
Technical data).
–
When assembling several devices in a device compound, consider general rules
for cross-wiring. For DC link coupling, higher-power devices must be placed
closer to the mains supply.
–
If there is a voltage supply to the device when the control cabinet is open,
vertical access to the bottom and top of the device must be prevented.
For mounting on the rear wall of the control cabinet, the servo drive cooling
element has a slot on the top in the shape of a keyhole and an ordinary slot on the
bottom.
Assembly of the servo drive
WARNING
Danger of burns through hot escaping gases and hot surfaces.
In case of error, incorrect wiring or incorrect polarity of the connections [X9A],
[X9B] and [X6A], internal components can be overloaded. High temperatures can
develop and hot gases can be released.
• Have an authorised electrician perform the installation according to the docu-
mentation.
WARNING
Danger of burns from hot housing surfaces.
Metallic housing parts can accept high temperatures in operation. In particular,
the braking resistor installed in the profile on the back side can become very hot.
Contact with metal housing parts can cause burn injuries.
• Do not touch metallic housing parts.
• After the power supply is switched off, let the device cool off to room tempera-
ture.
•
Mount the servo drive on the rear wall of the control cabinet with suitable
screws while complying with the assembly instructions.
7
Installation
7.1
Safety
WARNING
Risk of injury from electric shock.
Contact with live parts at the power connections [X6A], [X9A] and [X9B] can result
in severe injuries or death.
• Do not pull out power supply plugs while live.
• Before touching, wait at least 5 minutes after switching off the load voltage to
allow the intermediate circuit to discharge.
WARNING
Risk of injury from electric shock.
The leakage current of the device to earth (PE) is
>
3.5 mA AC or 10 mA DC.
Touching the device housing if there is a fault can result in serious injuries or
death.
Before commissioning, also for brief measuring and test purposes:
• Connect PE connection on the mains side at the following positions:
• Protective earth connection (earthing screw) of the housing
• PE pin of the connection [X9A] (power supply)
The cross section of the PE conductors must be at least equal to the
cross section of the mains conductor L at [X9A].
• Connect motor cable to connection [X6A] and the shield of the motor cable on
the front side to PE via the shield clamp of the servo drive.
• Observe the regulations of EN 60204-1 for the protective earthing.
WARNING
Danger of burns through hot escaping gases and hot surfaces.
In case of error, incorrect wiring or incorrect polarity of the connections [X9A],
[X9B] and [X6A], internal components can be overloaded. High temperatures can
develop and hot gases can be released.
• Have an authorised electrician perform the installation according to the docu-
mentation.
WARNING
Risk of injury from electric shock in the event of incomplete insulation at the
power connections [X6A], [X9A] and [X9B].
Before operating, plugging in or unplugging the operator unit CDSB or a con-
nector from a hot-plug-capable interface, the following points must be fulfilled:
• The conducting lines at the device are completely insulated.
• The protective earthing (PE) and the shield connection are correctly connected
to the device.
• The housing is free of damage.
WARNING
Risk of injury due to overheating and electric shock with faulty live components
Closing the branch-circuit protective device with faulty live components may
cause fire or electric shock.
• The opening of the branch-circuit protective device may be an indication that
a fault current has been interrupted. To reduce the risk of fire or electric
shock, current-carrying parts and other components of the controller should
be examined and replaced if damaged. If burnout of the current element of
an overload relay occurs, the complete overload relay must be replaced.
Information for operation with safety functions
NOTICE
Check the safety functions to conclude the installation process and after every
modification to the installation.
During installation of safety-related inputs and outputs, also observe the fol-
lowing: