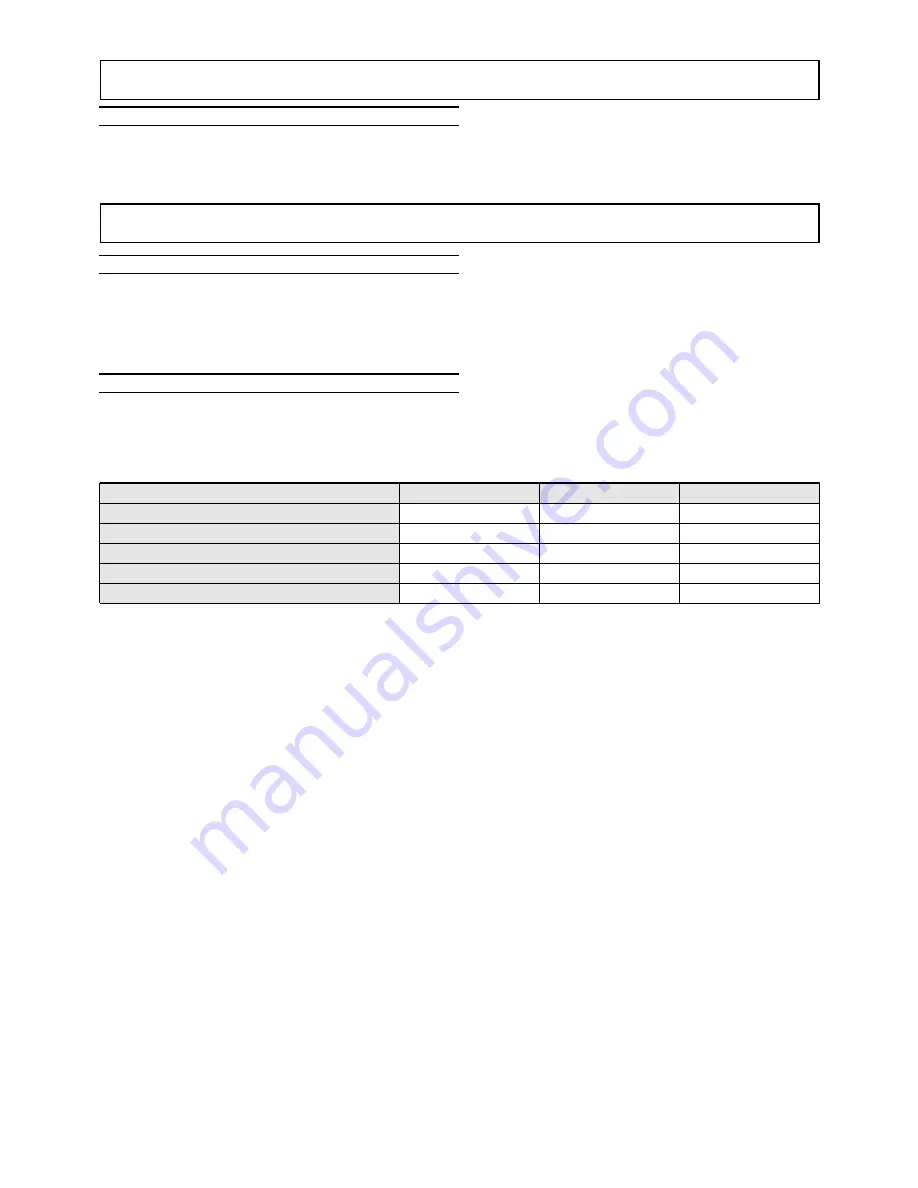
39
SETTING AT WORK
General rules
To validate the contractual warranty, the machine must only be set at work by an authorized assistance center.
Before it is called, check to make sure that all parts of the installation have been completed, that the unit is levelled,
the plumbing connections made with the relative air vent and that the electrical connections have been made.
MAINTENANCE
General rules
Maintenance is of extreme importance if the system is to operate in a regular way and give fade-free service. Have
extraordinary maintenance work done by qualified and authorized personnel. Comply with the safety precautions
given in the relative section of this manual and take all the necessary precautions.
The following information is only a guide for the end user.
Routine maintenance
The inspections described below to which the unit must be subjected do not require specific technical know-how.
They merely include a few simple checks involving certain parts of the unit.
Call an authorized assistance center if actual maintenance work is required.
The table below gives a recommended list of inspections which should be carried out at the indicated frequencies.
DESCRIPTION
Visual inspection of the structure of the unit
Inspection of the hydraulic circuit
Inspection of the electrical system
Inspection of the condensing section
Reading and recording of operating parameters
WEEKLY
•
MONTHLY
•
•
•
EVERY SIX MONTHS
•
• Visual inspection of the structure of the unit
When checking the condition of the parts that form the structure of the unit, pay particular attention to the parts lia-
ble to rust. If traces of rust are noted, they must be treated with rust-inhibitor paint in order to eliminate or reduce
the problem. Check to make sure that the external panels of the unit are well fixed.
Bad fixing gives rise to noise and abnormal vibrations.
• Inspection of the hydraulic circuit
Check visually to make sure that there are no leaks from the hydraulic circuit. If the pumping module accessory is
installed, it is advisable to make sure that the water filter is clean.
• Inspection of the electrical system
Make sure that the power cable that connects the unit to the distribution panel is not torn, cracked or damaged in a
way that could impair its insulation.
• Inspection of the condensing section
WARNING: The finned pack exchanger has fins made of aluminium or some other thin material, thus even acci-
dental contact could cause cuts. Comply with the instructions in the relative section.
• Condensing bank
In view of the function of this component, it is very important for the surface of the exchanger to be as free as pos-
sible from clogging caused by items that could reduce the air flow rate of the fan and, thus, the performances of the
unit itself. The following operations may be required:
- Remove all impurities (such as paper scraps, leaves, etc., etc.) that could be clogging the surface of the bank either
by hand or using a brush (comply with the above mentioned safety prescriptions).
- If the dirt has deposited on the fins and is difficult to remove by hand, use a jet of compressed air or pressurized
water on the aluminium bank surface, remembering to direct the jet in a vertical direction to prevent the fins from
being damaged.
- “Comb” the bank with the relative tool, using the appropriate comb spacing for the fins if some parts of them are
bent or squashed.
• Helical electric fans
Visually ionspect these parts to make sure that the electric fans are well fixed to the bearing grille and that this lat-
ter is fixed to the structure of the unit. Bad fixing leads to noise and abnormal vibrations.
• Reading and recording the operating parameters
This can only be done if the optional “pressure gauge kit” is available.
Summary of Contents for RPA 16
Page 14: ...14 DIMENSIONS Overall dimensions of the units Mod 16 19 Mod 24 30 Mod 38 42 50...
Page 19: ...19 ELECTRICAL CONNECTIONS Wiring diagram for models 24 30 2 38 2...
Page 20: ...20 ELECTRICAL CONNECTIONS Wiring diagram for models 30 3 38 3 42 3 50 3...
Page 42: ...42...
Page 44: ...NOTE...
Page 45: ...NOTE...
Page 46: ...NOTE...