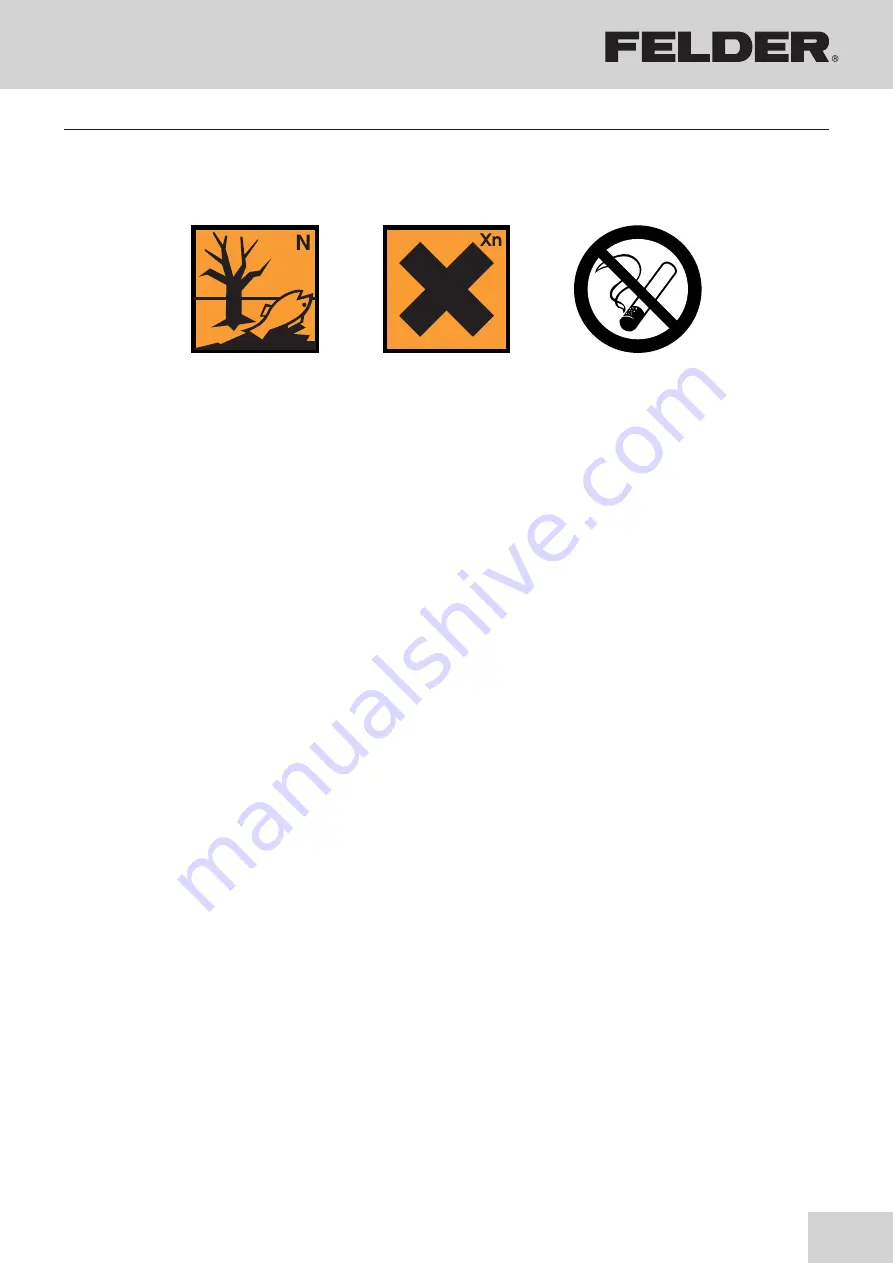
53
Edgebander
G 330 / G 360 / G 380
10.4.3 Safety instructions about the hot melt adhesives
Excerpt from the safety data sheets
Please read the complete data sheet of each hot melt adhesive!
Application purpose:
EVA - Glues (ethylene vinyl acetate) -
Basic adhesive
PUR - Glues (Polyurethane) -
Adhesive with high heat resistance and humidity resistance.
Danger indications:
R50/R53 = very poisonous to water organisms
may be harmful to waters in the long-term
Individual precautionary measures:
Ensure that the area is well ventilated.
Toxic vapours may be released if heated above the break-down point (carbon monoxide, hydrocarbons, acetic acid).
Personal protective equipment:
Observe the conventional precautionary measures when handling chemicals.
Avoid skin contact with the glue. Do not breathe in fumes.
Respirator: a respirator is necessary if ventilation/dust extraction is insufficient.
Gloves: thermally insulating gloves made of leather or thick material.
Eye protection: goggles are recommended when transferring the glue.
Personal protection: standard protective work clothing.
First aid measures:
If your skin has come into contact with the glue, apply cold water to cool down.
Do not peel off hardened glue from your skin. Consult a doctor.
Rinse your eyes with clean running water for several minutes if some of the product has gone into your eyes.
Contact a doctor.
Consult a doctor if you suffer continued complaints after swallowing some of the product.
Measures to fight fire:
Appropriate extinguisher: CO2, foam (alcohol ?), fire extinguishing powder or water spray.
Notes on disposal:
Leave to harden, remove mechanically. Small amounts may be disposed of in domestic waste.
Dispose of according to local authority regulations. The product‘s valid waste code can be found in the European
Waste Catalogue.
Environmentally
unfriendly
Harmful
Do not smoke
Maintenance/Service