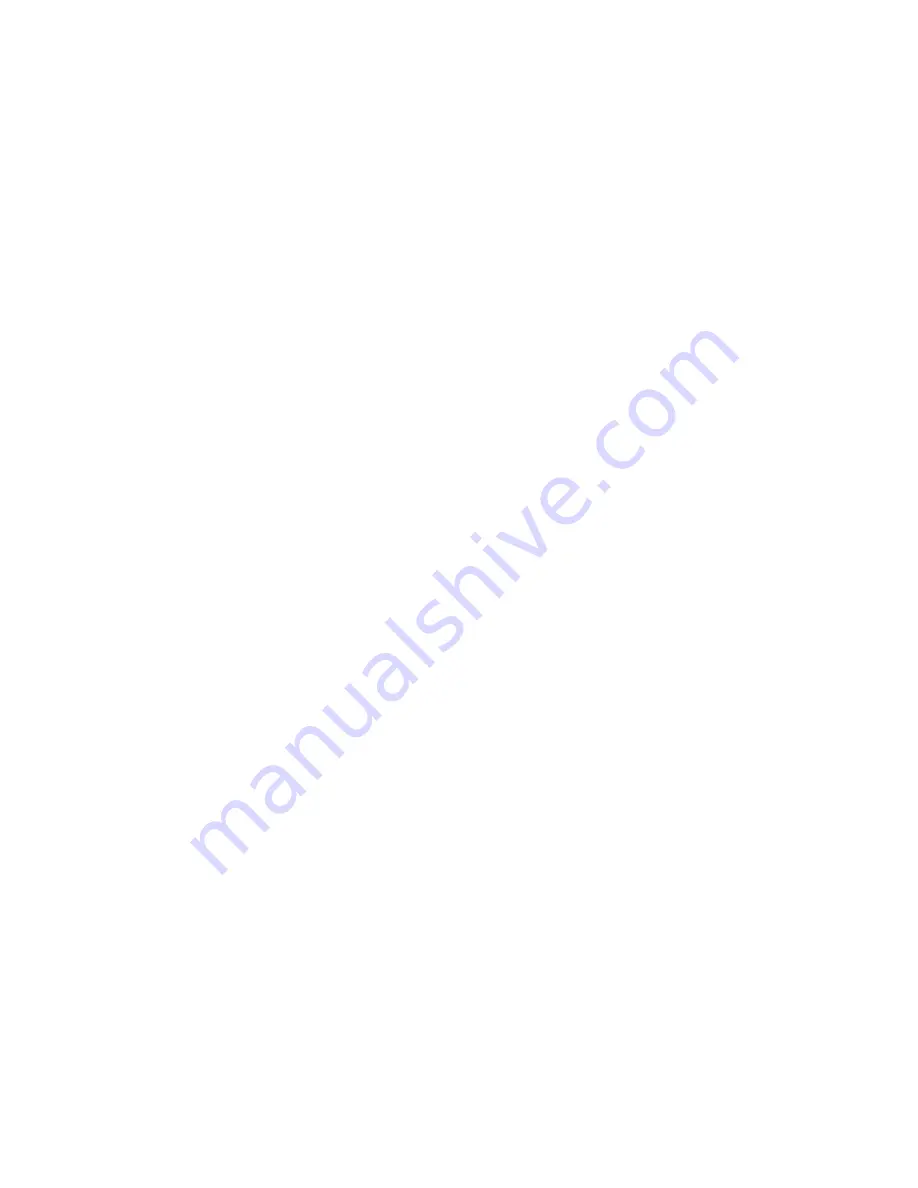
- 10 -
Remote Refrigeration Operation
The remote models manufactured before 12/1/19 are designed to use 134A refrigerant and after 12/1/19 are
designed to use R531a refrigerant and shipped from the factory with the evaporator coil, expansion valve,
drier filter, sight glass and refrigerant solenoid valve. The required high-low-pressure control and remote
condenser can be provided as a factory option and will be required to be charged with 134a or R531A
refrigerant after installation.
The unit temperature is controlled by an electronic control that senses air temperature and opens and closes
the refrigerant solenoid valve as required to maintain proper temperature.
Once proper temperature is reached the solenoid valve closes and shuts off the refrigeration flow to the unit
and initiates a pump down cycle. This will allow the remote low pressure switch to open and shut off
remote compressor. The solenoid will remain closed until the electronic control probe reaches its “cut in”
set point. The electronic control will also sense a frosted coil that requires a defrost cycle and closes
solenoid until defrost is complete. There are also a defined number of scheduled defrosts that also insures a
full defrost occurs.
Remote Refrigeration Installation
The condensing unit and pressure control are optionally supplied from the factory for remote location
installation. A remote high low-pressure switch must be mounted and wired by the installer. The high low-
pressure switch must be wired in series with the compressor power supply as shown in diagram below.
1.
Mount condensing unit as close to the remote display case as practical. All refrigeration and/or
electrical materials between the condensing unit and display case are to be supplied by installing
contractor.
2.
Route properly sized and designed refrigeration lines from the condensing unit to the cabinet. Follow
line sizing charts and piping instructions in the condenser unit’s manufacturers instruction manual.
Horizontal suction lines should be pitched downward towards the condensing unit at least ½” per 10’
run to aid the oil drainage. A “P” trap must be installed in the suction line at the foot of every riser to
insure oil return. Dry nitrogen must be used to flow through tubing while brazing refrigeration lines.
3.
Suction line must be insulated the entire length with Armaflex (or equivalent). Do not run liquid line
inside insulation with suction line.
4.
The remote high/low-pressure control must be mounted, wired and set by the installer.
5.
Leak check condensing unit, cabinet, and all connecting tubing. Cabinet and condensing unit tubing
should be checked to insure no leaks occurred during shipping or from rough handling.
Make certain all refrigeration valves are opened and evacuate system below 500 microns. System must
hold below 500 microns for 1 minute with pump isolated. Charge the system with refrigerant type
specified on the data plates.
Summary of Contents for ITR Series
Page 14: ...14 Counter ITR60 Self Contained Counter ITRSS60 Self Contained...
Page 15: ...15 Floor ITR ITRSS 36 Self Contained...
Page 16: ...16 Floor ITR ITRSS 48 Self Contained Floor ITR60 Self Contained...
Page 17: ...17 Floor ITRSS60 Self Contained Refrigerated Remote Models...
Page 18: ...18 All ITR Counter Remote All ITR Floor Remote All ITRSS Counter Remote...
Page 19: ...19 All ITRSS Floor Remote Floor ITD ITDSS NON Refrigerated...