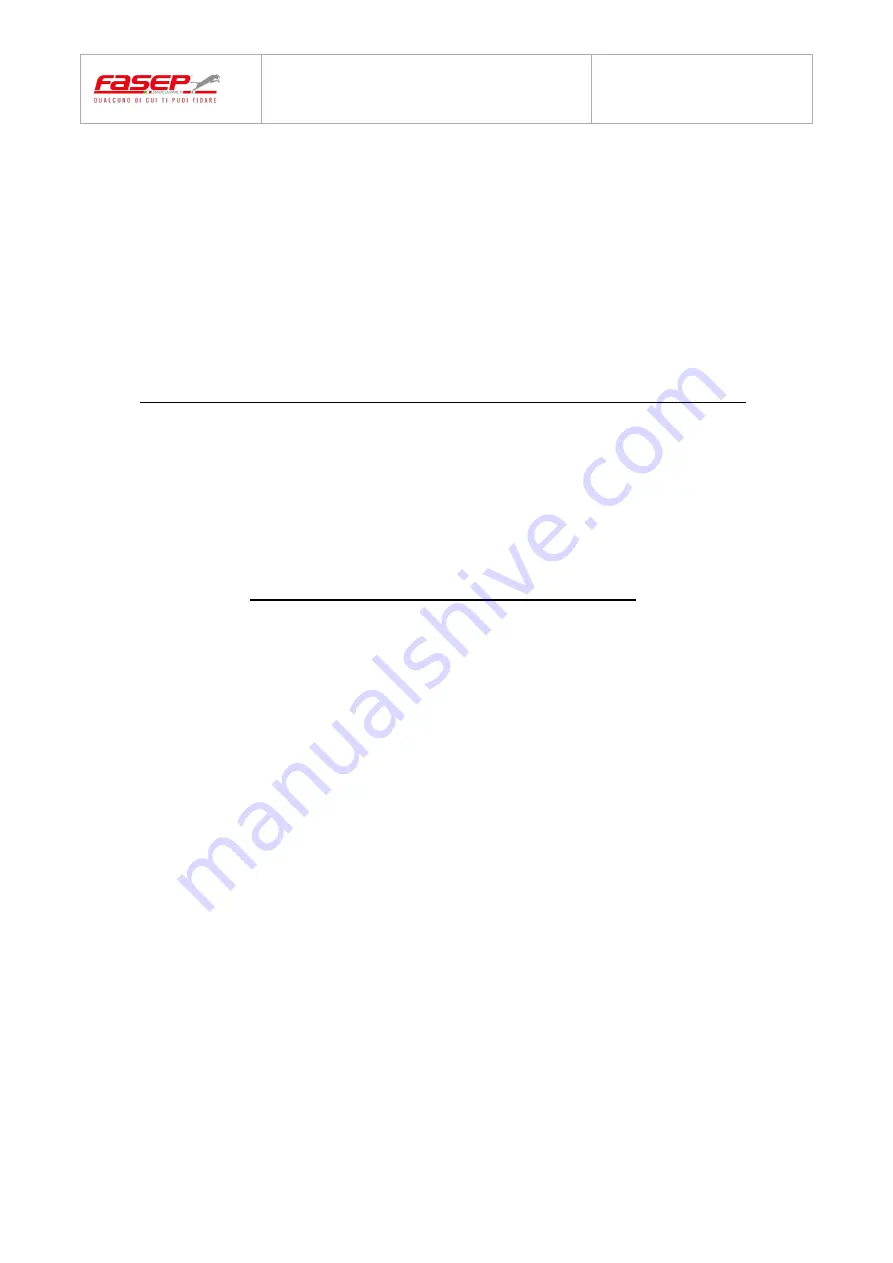
OPERATING AND MAINTENANCE MANUAL
RASE.TOP.4028
Code DOC.
UM TOP AUTOMATIC
4.0
Rev. 6
Page 9 of 86
9
1.4 - CERTIFICATION AND CE MARKING
The machine was manufactured in compliance with Directive 2006/42/EC and with the pertinent
and applicable EU Community Directives at the time it was put on the market (Fig. 1).
DECLARATION OF CONFORMITY
(Encl. II A, Part I, Selection A- Machinery Directive 2006/42/EC)
Declares under the sole resposability of its legal representative that the machine:
Name: Tyre Changer
Model RASE.TOP.4028
Year:
Serial No:
Absorbed power: 3.5 kW
Weight: 780Kg
Conforms with the safety requirements set forth by:
Machinaru Directive 2006/42/EC
Electromagnetic Compatibility Directive 2004/108/EC
Name and Surname.............................